20 марта 2008
Часть II. Процедуры определения параметров точности оборудования
Статистическое определение параметров точности оборудования
Оценка точности автомата в общем случае происходит путем анализа некоторой выборки – т.е. установки группы компонентов на ПП, измерении отклонения их положения от номинального и последующего проведения статистического анализа полученных данных.
Предположим, с помощью исследуемого автомата на печатную плату было установлено n компонентов, после чего была измерена ошибка размещения каждого ЭК, т.е. отклонение центра его реального положения на ПП от номинального (по осям X, Y или углу θ).
Важно отметить, что результаты данной процедуры будут в значительной степени зависеть от того, проводится ли она на откалиброванном оборудовании или нет. Также должны быть сведены к минимуму факторы, не относящиеся к автомату: геометрические размеры компонентов и рисунка платы должны быть изготовлены с достаточной точностью, чтобы это не влияло на результаты эксперимента, напряжение питания и давление в пневматической системе должны хорошо контролироваться и т.д.
Считая закон распределения положения компонента нормальным, можно определить несмещенные оценки математического ожидания и среднеквадратичного отклонения по выборке из n компонентов по следующим формулам:
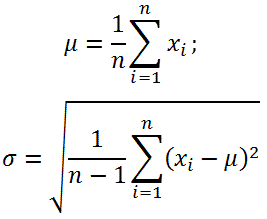
Определив данные оценки, можно указать вероятность попадания случайной величины в стандартный диапазон, симметричный относительно нуля и кратный среднеквадратическому отклонению: ± 1 σ, ± 2 σ и т.д.
Стандартизованная процедура оценки точности для автоматов установки компонентов
Чтобы обеспечить как производителей автоматов установки компонентов, так и их пользователей стандартной процедурой оценки точности такого оборудования, Ассоциацией IPC в 2002 году был выпущен специальный стандарт IPC-9850 «Surface Mount Placement Equipment Characterization» – «Определение параметров оборудования для установки компонентов поверхностного монтажа» [4].
Точность в данном стандарте вычисляется двумя способами:
1) Отдельно для осей X, Y и угла θ при Cpk = 1,33 и Cpk = 2.
2) Комплексно, с объединением в одном значении ошибок установки по осям X, Y, Z и углу θ, для показателя перекрытия вывода и КП платы 50% и 75%.
Первый способ является традиционным для производителей сборочного оборудования. Важно отметить, что стандарт предусматривает указание точности при строго определенных значениях показателя работоспособности процесса. Отметим, что корректно сравнивать значения погрешностей двух моделей оборудования можно лишь в том случае, когда оба из них приводятся при одном и том же значении Cpk.
Расчет заключается в определении отклонений симметричного допуска автомата при известных значениях μ, σ и приведенных выше значениях Cpk :

Вычисленные значения по осям X, Y и углу θ записываются в отчетную форму.
Второй способ в большей степени принимает во внимание последующий процесс пайки установленных на плату компонентов. Он позволяет учесть случаи, когда отдельные составляющие суммарной погрешности установки попадают в допустимый диапазон, но в комплексе не обеспечивают формирование требуемой геометрии паяного соединения.
Перекрытие КП платы и вывода на 50 и 75% выбрано разработчиками стандарта, исходя из следующих соображений. Стандартом IPC-A-610D «Критерии качества электронных сборок» [5] предусмотрено разделение электронной аппаратуры на классы:
Class 1 – электронные устройства общего назначения;
Class 2 – специализированные электронные устройства, для которых обязательными являются требования сохранения характеристик в процессе длительной эксплуатации;
Class 3 – электронные устройства с высокими характеристиками, для которых важнейшими требованиями являются сохранение высоких эксплуатационных параметров, при этом условия функционирования могут быть жесткими, а изделие должно функционировать бесперебойно в течение требуемого времени.
Требования к устройствам различных классов с точки зрения точности установки ЭК на плату отличаются по максимально допустимому выступанию вывода за пределы КП – на 50% от ширины вывода для изделий 1 и 2 класса, и на 25% – 3 класса, что соответствует требованиям к минимально допустимой ширине образованного паяного соединения – не менее 50% перекрытия вывода ЭК и КП для изделий 1 и 2 класса, и не менее 75% – для изделий 3 класса [5, 6].
В стандарте приведены формулы для расчета перекрытия, отдельно для компонентов с выводами по двум и четырем сторонам корпуса, а также для компонентов с матричными выводами на основе двумерной математической модели. Размеры КП при этом берутся из стандарта IPC-782A (который в настоящее время заменен на более современный стандарт IPC-7351A).
Процедура расчета при втором подходе следующая:
- определяются ошибки установки компонентов по осям X, Y, Z и углу θ;
- определяются значения перекрытий выводов отдельно по каждому установленному компоненту согласно формулам стандарта IPC-9850;
- определяются среднее перекрытие μ (в %) и его среднеквадратическое отклонение σ;
- определяются два значения Cpk – для 50% и 75% перекрытия соответственно по следующим формулам:
для 50% перекрытия и
для 75% перекрытия.
Вычисленные значения Cpk отражаются в отчетной форме в качестве результатов.
Под ошибкой установки компонентов в стандарте понимается расстояние между действительным центром установленного на плату компонента и его номинальным положением, определенным согласно CAD-данным относительно реперных знаков тестовой платы. Ошибка определяется по взаимно перпендикулярным осям X и Y, а также по углу θ поворота ЭК вокруг его центра тяжести в плоскости XY; ось X располагается параллельно надписи на тестовой плате, а ось Y – перпендикулярно ей.
Определение повторяемости
Повторяемость согласно стандарту IPC-9850 определяется как среднеквадратическое отклонение ошибки установки компонентов, т.е. представляет собой σ. Результаты отражаются в отчетной форме по осям X, Y и углу θ.
Применяемое измерительное оборудование
После установки компонентов на тестовую плату необходимо точно измерить координаты их расположения на ней и определить ошибку установки по обеим осям и углу. Проведение таких измерений с использованием системы технического зрения (СТЗ) автомата не даст статистически достоверных результатов, так как точность результатов измерений будет иметь тот же порядок, что и определяемая ошибка установки ЭК на плату. Кроме того, автомат не обеспечит достаточной гибкости проведения подобных измерений, так как задача организации разнообразных статистических экспериментов выходит за рамки его функционального назначения. Процедура калибровки, заложенная в ПО автомата, в общем случае отличается от проводимой согласно стандарту IPC-9850, и может не предоставлять пользователю полный набор требуемой статистической информации.
Вследствие этого для проведения измерений следует пользоваться специальными установками – координатно-измерительными машинами (КИМ). Они обеспечивают высокую точность измерений, обладают развитыми возможностями по реализации различных статистических экспериментов и обработке полученной информации.
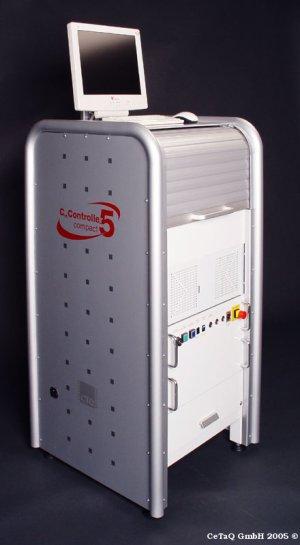
Рис. 10. Внешний вид КИМ CmController 5 Compact производства компании CeTaQ GmbH. Фото с сайта www.cetaq.net
В качестве примера такого оборудования можно привести изображенную на рис. 10 портальную модель CmController 5 Compact производства компании CeTaQ GmbH [7]. Данная модель предназначена специально для проведения измерений при выполнении различных операций технологии поверхностного монтажа, в том числе непосредственно для выполнения тестов согласно стандарту IPC-9850.
Установка имеет следующий набор параметров:
- Погрешность измерений: для чип-компонентов – 4 мкм; для стеклянных макетов QFP-компонентов – 2 мкм.
- Производительность: 1500 измеренных точек в час.
- Рабочая область: 300 x 200 мм.
- ОС: Windows 2000.
- Оснащение: ЖК-монитор, мышь или трекбол, сетевой адаптер, DVD-RW и пр.
- Программное обеспечение: для обработки изображений (CmCVis) и статистической обработки полученных данных (CmCStat 5.0).
- Габариты: ~ 600 х 600 x 1230 мм.
- Вес: 120 кг.
Подобные КИМ могут использоваться для оценки точности не только автоматов установки компонентов, но и установок для нанесения пасты трафаретной печатью или дозированием, а также систем АОИ.
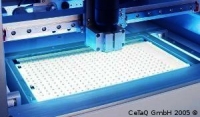
Рис. 11. Рабочая зона КИМ CmController 5 в процессе проведения измерений. Фото с сайта www.cetaq.net
Тестовые платы
Метод оценки точности и повторяемости, предлагаемый стандартом IPC-9850, использует в качестве специальной тестовой платы стеклянную панель.
Стеклянные платы используются вследствие хорошей стабильности их размеров по сравнению с традиционными печатными платами из стеклотекстолита, а также возможности их очень точного изготовления. Кроме того, прозрачность стекла позволяет КИМ использовать подсветку снизу для увеличения повторяемости измерений. Изготовленные из хрома реперные знаки обеспечивают высококонтрастное изображение при распознавании их как посредством СТЗ КИМ, так и СТЗ автомата установки компонентов.
Выпускаются различные тестовые платы – этим занимаются, в частности, сами производители КИМ для поверхностного монтажа – отличающиеся размерами, толщиной, цветом выполненных из хрома изображений (например, коричневый, голубой либо традиционный серебристый цвет), шагом сетки и допуском на ее расположение (типичные значения составляют ~0,5 – 4 мкм). Существуют как стандартные типоразмеры плат, так и возможность их изготовления на заказ под конкретные требования заказчика. Часто платы крепятся на металлическую раму с целью защиты от повреждений или выполнения особых требований к проведению измерений. Тем не менее, возможно применение тестовых плат без рам, как это, в частности, предусмотрено стандартом IPC-9850.
Пример тестовой платы, предназначенной специально для определения точности автомата установки компонентов методами стандарта IPC-9850, приведен на рис 12.
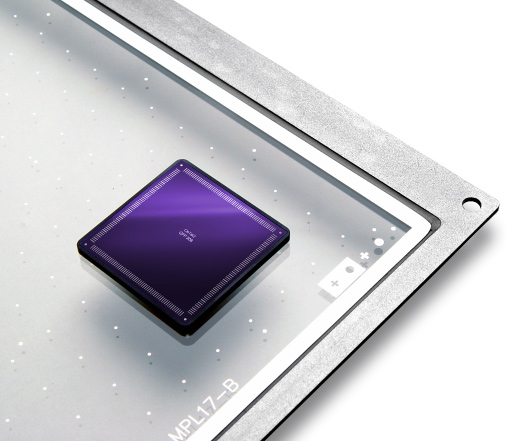
Рис. 12. Панель MPL17, изготовленная в соответствии с требованиями стандарта IPC-9850. Фото с сайта www.cetaq.net
Выпускаются платы, специально предназначенные для осуществления калибровки автоматов. Их предоставляют как сами производители оборудования, так и сторонние фирмы-производители тестовых плат и макетов компонентов [15]. На рис. 13 приведен пример такой многофункциональной платы, предназначенной, в частности, для проведения тестирования/калибровки автоматов.
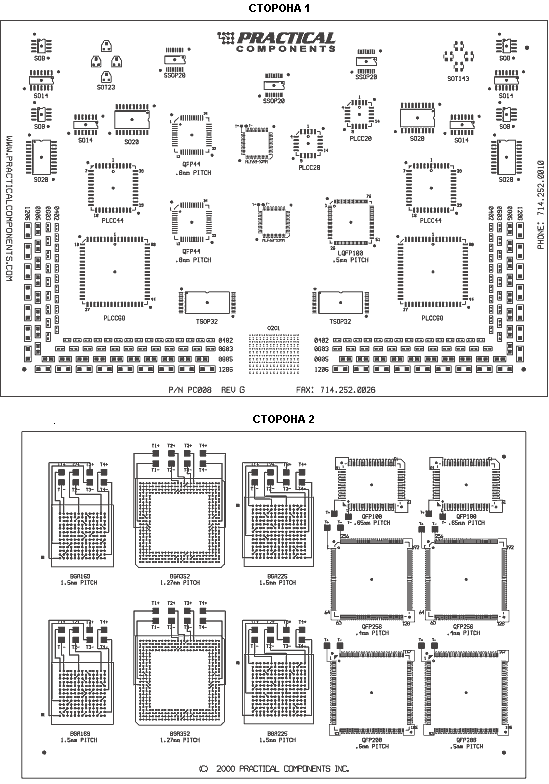
Рис. 13. Тестовая/калибровочная плата. Изображение с сайта www.practicalcomponents.com
Тестовые компоненты
ЭК также представляют собой макетные образцы, с высокой точностью изготовленные из стекла с нанесенными на них изображениями проекции корпуса и выводов, которые выполнены из хрома. Эти макеты компонентов обладают всеми свойствами реальных ЭК, их отличие – исключительно в высокой точности изготовления. Погрешность изготовления таких ЭК составляет менее 2 мкм.
Важно использовать те макеты ЭК, у которых изображение выводов нанесено на сторону, располагаемую ближе к видеокамере СТЗ КИМ. В противном случае, если камера располагается под некоторым углом к плоскости ЭК, возможно формирование побочного изображения, смещенного относительно действительного, вследствие преломления света стеклянным корпусом макета ЭК (рис. 14).
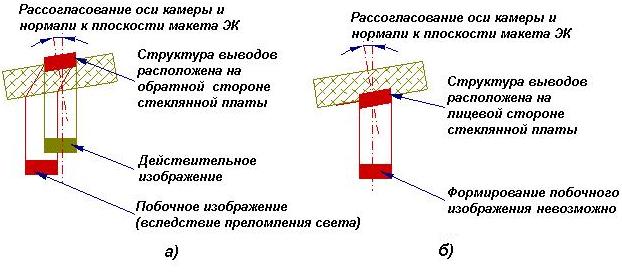
Рис. 14. Влияние расположения стороны платы, на которой расположены изображения выводов из хрома на корпусе макета ЭК, по отношению к позиции камеры СТЗ КИМ на точность формирования изображения: а) изображения расположены на обратной стороне платы; б) изображения расположены на лицевой стороне платы. Рисунок с сайта www.cetaq.com
Стандарт IPC-9850 предусматривает использование четырех типов таких компонентов: QFP (двух типоразмеров), BGA, SOIC-16 и конденсаторов типоразмера 0603 (1608 в метрической системе). Конденсаторы были выбраны вследствие более точного изготовления их сторон в противоположность чип-резисторам, у которых верхние границы выводов, обозреваемые камерой КИМ, могут не совпадать с границами выводов на нижней стороне, обозреваемыми камерой СТЗ нижнего обзора автомата при установке.
Пример стеклянного макета компонента QFP 208 приведен на рис. 15.
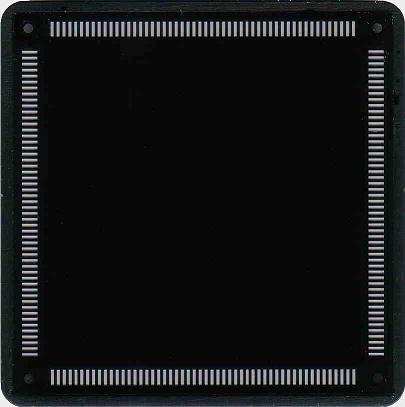
Рис. 15. Макет корпуса ЭК QFP 208. Рисунок с сайта www.cetaq.net
Способ удержания ЭК на тестовой панели
На тестовую панель в позицию установки компонентов наносится клейкое вещество, удерживающее ЭК в процессе установки на автомате и последующих измерений координат их центров с помощью КИМ. Стандартом IPC-9850 не рекомендуется нанесение клея распылением из-за нестабильности полученных результатов, и приведенные в нем рекомендации направлены на применение двусторонних клейких лент и листов. Подробно процедура нанесения клейкого слоя на тестовую плату описана в Приложении C IPC-9850. Отметим, что основным требованием является максимальное смещение ЭК, установленных на тестовую пластину с нанесенным адгезивом, не более чем на 2 мкм в течение времени, прошедшего между двумя последовательными измерениями их положения (минимально – спустя 2 часа после установки). Межоперационную транспортировку тестовой платы с установленными на клейкий слой компонентами следует осуществлять строго в горизонтальном положении [4].
Методы определения центра установленного на панель ЭК
Для чип-компонентов и SOIC-микросхем определение их центра проводится, исходя из результатов измерений расположения соответственно корпусов ЭК и их выводов. Для QFP и BGA-компонентов координаты центра вычисляются, исходя из измеренного положения локальных реперных знаков, расположенных как на тестовой стеклянной пластине, так и на самом стеклянном корпусе макета ЭК. Это сделано с целью сокращения предельной погрешности позиционирования измерительной камеры с высоким разрешением, так как ее поле зрения меньше размеров корпусов крупных BGA- и QFP-компонентов (рис. 16).
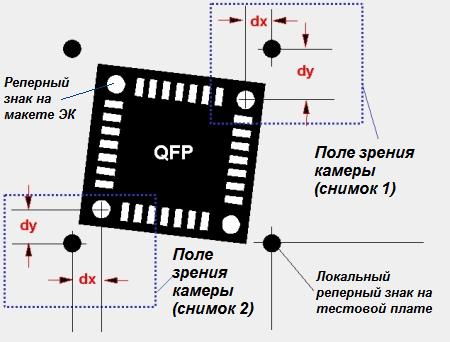
Рис. 16. К определению координат центра QFP и BGA-компонентов с помощью оптической системы КИМ. Рисунок с сайта www.cetaq.com
В Приложении D стандарта IPC-9850 рассмотрено несколько математических методов определения координат центра ЭК, приведены расчетные формулы и даны рекомендации по выбору метода, подходящего для конкретного типа ЭК.
Точность и повторяемость координатно-измерительных машин
Неточность измерений вызывается следующими факторами:
- погрешностью изготовления стеклянной тестовой платы;
- погрешностью изготовления тестовых образцов ЭК;
- точностью и повторяемостью координатно-измерительной машины (КИМ).
Параметры КИМ в части точности и повторяемости измерений должны обеспечивать возможность достоверного определения точности и повторяемости установки компонентов на печатную плату.
Оценка повторяемости и воспроизводимости КИМ
Для оценки параметров КИМ применяются различные методы оценки повторяемости и воспроизводимости Gauge Repeatability and Reproducibility (GR&R), заключающиеся в определении ошибки измерений δ(GR&R). Одна из методик определения δ(GR&R) приведена в Приложении H стандарта IPC-9850. Пригодность данной КИМ для проведения конкретных измерений определяется отношением этой ошибки к допуску автомата, выраженному в %:
, где

В процессе измерений точности и повторяемости КИМ заполненная 24 компонентами специальная тестовая плата Placement Verification Panel (PVP), чертеж которой приведен в стандарте IPC-9850, подвергается трем циклам по три измерения в каждом; при этом необходимо задействовать по крайней мере двух различных операторов КИМ.
В стандарте IPC-9850 результат представляется в виде допустимого верхнего и нижнего отклонения допуска автомата, при которых обеспечивается значение GR&R не хуже 25% (при симметричном допуске):
.
При этом, соответственно, минимально допустимая погрешность установки компонентов для измеряемого автомата, которая приведена в его технических характеристиках, составляет
.
Традиционно значение GR&R должно не превосходить 20-25%; однако, в том же стандарте IPC-9850 приведено более жесткое ограничение на ошибку измерений: GR&R < 10% [4 – Приложение H].
Производитель КИМ [7] отмечает, что средство измерений должно быть, по крайней мере, в 6-10 раз точнее, чем измеряемый объект. Параметры упоминавшейся выше установки CmController позволяют, таким образом, производить измерения точности и повторяемости автоматов установки компонентов с малым шагом выводов, в спецификациях которых указаны значения вплоть до 12 мкм, а высокопроизводительных автоматов для установки чип-компонентов – до 24 мкм (при ).
Точность оптической системы КИМ
Кроме описанной выше процедуры оценки повторяемости и воспроизводимости, для КИМ в рамках стандарта IPC-9850 проводится процедура определения точности, с которой оптическая система КИМ способна измерять положение установленных на тестовую стеклянную панель макетов ЭК. Данная процедура проводится с применением стандартизованной Национальным институтом стандартов и технологий США (National Institute of Standards and Technology, NIST) панели проверки точности Accuracy Verification Panel (AVP), также представляющей собой стеклянную панель с вытравленными из хрома прецизионными изображениями проекций корпусов ЭК с выводами (для 1608C и SOIC) и групп из четырех локальных реперных знаков на корпусе компонента (для QFP и BGA). Некоторые из них специально выполнены смещенными и повернутыми относительно своих номинальных положений, задаваемых в программе КИМ, чтобы оценить точность распознавания при рассогласовании между заданным и номинальным расположением компонента на плате.
С помощью КИМ проводятся измерения положения центра каждого ЭК на AVP, после чего из этих значений вычитается номинальное значение, сертифицированное NIST. В результате процедуры определяются верхнее и нижнее отклонения поля допуска КИМ, при которых обеспечивается значение показателя работоспособности процесса Cpk, равного 2.0 (при симметричном допуске):
.
Такие вычисления проводятся для осей X, Y и угла θ. Стандарт не предусматривает оценки соответствия вычисленных отклонений требуемым значениям, однако утверждается, что чем ближе измеренные КИМ значения к номинальным, тем выше измерительные возможности оптической системы данной КИМ.
|