10 июля 2007
Свойства, применение и хранение паяльных паст
Введение
Паяльная паста используется в технологии поверхностного монтажа в качестве материала, обеспечивающего образование паяных соединений между контактными площадками (КП) печатной платы (ПП) и выводами поверхностно монтируемых электронных компонентов (ЭК). Одним из важнейших достоинств пасты является ее многофункциональность и технологичность применения: помимо основного назначения в качестве припоя, она одновременно является флюсом, а также фиксирует компоненты при их установке на ПП. Применение паст позволяет значительно автоматизировать процесс нанесения. Правильный выбор пасты, соблюдение определенной технологии при подготовке ее к применению и предписанных производителем условий хранения – немаловажные факторы в обеспечении качества сборки электронного модуля. Эти вопросы рассмотрены в данной статье.
Паяльные пасты и их характеристики
Паяльная паста представляет собой густую, вязкую массу, состоящую из смеси порошкообразного припоя и флюса-связки. Флюсовая составляющая пасты содержит канифоль или синтетические смолы, активаторы, добавки для контроля вязкости, стабилизаторы и растворители.
В электронной промышленности преимущественное распространение получили следующие припои: Sn63/Pb37 и Sn62/Pb36/Ag2 (добавление серебра снижает его миграцию с покрытия контактных поверхностей ЭК в материал припоя) для эвтектической пайки и Sn95,5/Ag3,8/Cu0,7 и Sn96,5/Ag3,5 – для бессвинцовой.
Характеристики пасты
Форма и размер частиц припоя
Данные параметры пасты являются чрезвычайно важными, так как определяют пригодность пасты для нанесения конкретным методом: трафаретной печатью либо дозированием, а также существенно связаны с геометрическими размерами апертур трафарета и шагом выводов устанавливаемых ЭК. Пульверизация расплавленного припоя, которая обычно применяется для получения порошкообразной припойной составляющей паст, приводит к образованию частиц преимущественно сферической формы. Такие пасты можно наносить как трафаретной печатью, так и дозированием.
Чем меньше площадь поверхности частицы припоя, тем меньше степень ее окисления. Так как отношение площади поверхности S к объему частицы V равно 1,5·D, где D – диаметр частицы, следовательно, паста с меньшим размером частиц более склонна к окислению. Это же соображение справедливо для частиц неправильной формы по сравнению со сферической. Пасты с мелкими частицами склонны к образованию шариков припоя при пайке, с крупными частицами либо частицами нерегулярной формы – к закупорке трафарета при нанесении.
По размеру частиц припоя, пасты подразделяются на 6 типов (согласно стандарту IPC/EIA J-STD-005 [8], см. таблицу 1).
Таблица 1. Классификация паст по размерам частиц припоя согласно стандартам IPC/EIA J-STD-005 и ASTM B- 214
Тип
|
Размер частиц припоя, мкм
|
Обозначение сетки по ASTM B-214
|
Параметры по стандарту IPC/EIA J-STD-005
|
Не более по ÆD, чем:
|
Менее 1% имеют больший ÆD, чем:
|
Минимум 80% имеют ÆD в диапазоне:
|
Максимум 10% имеют меньший ÆD, чем:
|
Средний ÆD частиц
|
Отношение S/V
|
1
|
160
|
150
|
150–75
|
20
|
н.д.
|
н.д.
|
–100/+200
|
2
|
80
|
75
|
75–45
|
20
|
60
|
1,00
|
–200/+325
|
3
|
50
|
45
|
45–25
|
20
|
35
|
1,71
|
–325/+500
|
4
|
40
|
38
|
38–20
|
20
|
31
|
1,93
|
–400/+500(635)
|
5
|
30
|
25
|
25–15
|
15
|
18
|
3,33
|
–500/+635
|
6
|
20
|
15
|
15–5
|
5
|
н.д.
|
н.д.
|
–635
|
|
Также используется классификация паст по стандарту ASTM B-214, где размер частиц оценивается густотой ячеек сетки, через которую может пройти определенное количество частиц. Например, параметр –200/+325 означает, что по крайне мере 99% частиц по массе пройдут через сетку в 200 ячеек/кв. дюйм и менее 20% - через сетку в 325 ячеек/кв. дюйм. Соответствие между двумя стандартами также приведено в таблице 1.
При выборе размера частиц пасты следует руководствоваться шагом выводов компонентов и шириной апертур (окон) трафарета. Преимущественно применяются пасты типов 2 и 3, для ЭК с малым шагом выводов – типа 3, при сверхмалом шаге может потребоваться применение паст типов 4 и 5. Для любых апертур необходимо, чтобы по крайней мере 4-5 частиц припоя умещалось вдоль сторон самой маленькой апертуры.
Содержание металла в пасте определяет толщину оплавленного припоя, осадку и растекание пасты и указывается в % по массе. Более высокое содержание металла ведет к увеличению толщины соединения после оплавления. Следует иметь в виду, что высота оплавленного припоя отличается от толщины нанесенного слоя пасты и может колебаться от 50% начальной толщины при 90% содержании металла до 25% при 75% [6], что необходимо учитывать при обеспечении требуемого объема паяного соединения. Типичное значение содержания металла для паяльных паст – от 80 до 90%. Значения у верхнего предела указанного диапазона характерны для паст, предназначенных для трафаретной печати, у нижнего – для нанесения дозированием.
Классификация флюсов в составе паст
Тип флюса в составе пасты определяет ее активность, необходимость отмывки и применяемые при этом способы. Флюсам, требованиям к ним и методам их испытаний посвящен стандарт IPC/EIA J-STD-004 [9]. В целом, выделяют три категории флюсов по методу удаления их остатков:
1. Группа канифольных флюсов. Изготавливаются на основе очищенной натуральной смолы, добываемой из древесины сосны (55-65%). Внутри группы по степени активности делятся на:
а) неактивированные (Rosin, R);
б) среднеактивированные (Rosin mildly activated, RMA);
в) активированные слабокоррозионные (Rosin activated, RA).
Флюсы группы R имеют наименьшую активность среди вышеперечисленных. Наибольшее распространение получили RMA-флюсы, имеющие достаточную очищающую способность, обеспечивающие хорошее смачивание и растекаемость припоя. Такие флюсы явились предшественниками материалов, не требующих отмывки. Тем не менее, они могут быть коррозионными, поэтому рекомендуется проводить отмывку изделий после пайки (растворителями либо водными мыльными растворами).
RA-флюсы используются достаточно редко вследствие своей высокой активности, преимущественно для пайки подвергшихся сильному окислению поверхностей. Такие флюсы требуют обязательной отмывки органическими растворителями на основе спирта.
2. Водосмываемые флюсы (Water soluble), изготовленные на основе органических кислот (иначе называемые organic acid, OA). Обеспечивают хорошие результаты пайки благодаря своей высокой активности, однако требуют обязательной отмывки горячей деионизированной водой (55–65°С).
3. Безотмывные флюсы, флюсы, не требующие отмывки (No-clean, NC), изготавливаемые на основе натуральных и синтетических смол. Имеют в составе меньше смол, чем RMA-флюсы (35-45%), являются среднеактивированными, их остатки после пайки являются некоррозионными и непроводящими. Процент твердых остатков No-clean флюсов сведен к минимуму и составляет менее 2 %. Отмывка при использовании таких флюсов не является обязательной. Если отмывка все же необходима, то проводится с применением тех же материалов, что и для RMA-флюсов.
Данные свойства пасты определяют ее поведение на трафарете, геометрические характеристики отпечатка и характер изменения их во времени. Для процесса нанесения пасты имеют значение такие характеристики, как вязкость, осадка, время сохранения свойств, клейкость. Эти параметры контролируются путем введения в состав пасты при ее производстве модификаторов – загустителей либо вторичных растворителей. Они имеют высокую температуру кипения, так как должны работать вплоть до температуры оплавления припоя. Их остатки, не полностью удаленные при оплавлении, могут стать причиной образования пустот в паяном соединении.
Вязкость (viscosity) определяет густоту паяльной пасты. Пасты – тиксотропные материалы, меняющие вязкость при действии механической нагрузки. Такое свойство очень важно для процесса нанесения – паста располагается поверх окон трафарета в вязком состоянии, и приобретает текучесть при продавливании ее ракелем, заполняя окна. При снятии нагрузки, паста снова переходит в вязкое состояние, что заставляет ее находиться в пределах площади КП и предотвращает растекание по неметаллизированной поверхности ПП. Помимо нагрузки, на вязкость пасты оказывает влияние температура окружающей среды и размер частиц пасты (вязкость будет ниже в случае крупных частиц и повышения температуры).
Для измерения вязкости пасты служат два распространенных прибора: вискозиметры Брукфилда и Малкома.
Метод Брукфилда (стандарт IPC-TM-650 [7], методы 2.4.34 и 2.4.34.1 в зависимости от ожидаемой вязкости пасти) использует стандартный принцип ротационной вискозиметрии: измерение вязкости осуществляется посредством пересчета крутящего момента, необходимого для вращения шпинделя прибора (стандартный вискозиметр Brookfield RVTD или аналогичный, шпиндели TC и TF) с постоянной скоростью (5 об/мин) при погружении его в исследуемую пасту на глубину в 2,8 см от поверхности при температуре окружающей среды 25±0,25°С.
Метод Малкома (стандарт IPC-TM-650 [7], метод 2.4.34.2 и 2.4.34.3 в зависимости от ожидаемой вязкости пасти) также основан на ротационном принципе и использует прибор со спиральным адаптером, состоящий из внутреннего нарезного и внешнего вращающегося (со скоростью 10 об/мин) цилиндров, благодаря совместному действию которых паста продавливается вверх, и измеряется крутящий момент на штоке внутреннего цилиндра. Методики измерений вязкости подробно описаны в стандарте IPC-TM-650 [7].
Производителями паяльной пасты указываются значения по одной либо обоим методикам, выраженные обычно в системе единиц СГС в пуазах, пз [poise, ps] (преимущественно – для метода Малколма) или сотых долях пуаза·1000, кспз [kilo centi poise, kcps] (для метода Брукфилда), а также в паскаль-секундах [Па·сек] в системе СИ. 1[пз] = 0,1 [Н·сек/м² = Па·сек]. Взаимосвязи между значениями, полученными этими двумя методами, не существует.
Рабочая вязкость паст указывается производителем. Рекомендуется, чтобы она находилась в следующих пределах (кспз, метод Брукфилда) [6]:
- 200 – 450 для дозирования;
- 450 – 800 для трафаретной печати (сетчатый трафарет);
- 750 – 950 для трафаретной печати (фольговый трафарет для ЭК с шагом выводов 1,27 мм);
- 900 – 1200 для трафаретной печати (фольговый трафарет для ЭК с малым шагом выводов).
Следует помнить, что повышение температуры уменьшает вязкость пасты. По мере обработки большого количества ПП происходит увеличение ее вязкости. Таким образом, для минимизации изменений вязкости необходимо добавлять свежую пасту в процессе печати, а также обеспечивать контроль температуры в зоне нанесения, что обеспечивается рядом моделей автоматов трафаретной печати.
Осадка – свойство пасты увеличивать размеры отпечатка после нанесения на КП. Для обеспечения хороших результатов пайки, осадка должна быть минимальной, так как чрезмерное увеличение отпечатков пасты ведет к образованию перемычек, в особенности для ЭК с малым шагом выводов.
Существует тест на осадку (стандарты IPC/EIA J-STD-005 [8], IPC-TM-650 [7], метод 2.4.35), заключающийся в нанесении пасты через трафарет заданной толщины (определяющей высоту нанесении пасты, в данном тесте 0,1 и 0,2 мм) на тестовую ПП с различным шагом выводов. Паста считается прошедшей тест на осадку для данной высоты нанесения и шага выводов, если после определенной выдержки (10-20 мин при 25±5°С и относительной влажности 50±10%; 10-15 мин при 150±10°С) эффекта осадки не наблюдается и между соседними КП не образуется перемычек.
Время сохранения свойств («время жизни»). Обычно данный термин означает максимальное время пребывания пасты на трафарете до нанесения, либо на ПП после нанесения, без деградации реологических свойств. Первое из них носит обозначение «stencil life» либо «print life» и составляет для различных паст обычно от 8 до 48 часов. Второе значение представляется более важным, так как оно определяет, через какой промежуток времени ПП должна быть передана на участок установки ЭК и далее на участок пайки (в настоящее время существуют пасты со значением данного показателя, равным 72 часам). Под данным параметром часто подразумевается время удержания ЭК на пасте («tack time», см. ниже в разделе «Клейкость»). Производителями паст обычно указывается один из этих параметров либо оба.
В целом, наиболее информативным является определение, обозначаемое обычно как «working life» («время жизни») [6]: максимальное время, прошедшее после открытия банки с пастой до ее оплавления без деградации реологических свойств. Он включает в себя время, требуемое на нанесение пасты, установку ЭК, предварительный нагрев при пайке и все промежуточные технологические операции.
Клейкость определяет способность пасты удерживать SMD-компоненты на своих местах после установки их на ПП и до пайки. Это свойство является индикатором того, подошло ли к концу время жизни пасты.
Тест клейкости (стандарты IPC/EIA J-STD-005 [8], IPC-TM-650 [7], метод 2.4.44) предусматривает применение стандартного тестера, измеряющего силу, необходимую для сдвига компонента определенного веса с площадки пасты определенного размера ( 6,3 мм и высоты 0,25 мм). Тестовый пробник двигается со скоростью 2,5±0,5 мм/мин и приводится в соприкосновение с компонентом, при этом в течение 5 секунд к компоненту прикладывается сила в 300±30 г. Далее производится сдвиг компонента с площадки с указанной скоростью и измеряется потребная для этого сила. Производится несколько измерений через определенные промежутки времени после нанесения пасты. Данные представляются в виде графика зависимости усилия сдвига от времени. По графику определяется время, обозначаемое как время удержания («tack life» либо «tack time»), по истечении которого сила сдвига уменьшается на 20%. Пиковая сила определяет собой удерживающую способность в граммах и обозначается в характеристиках пасты как «tackiness» либо «tack force» (типичное значение: 35 – 50 г). Обычно это значение относится к начальной клейкости, измеренной непосредственно после нанесения пасты («initial tackiness»).
Для различных паст время удержания может различаться и составлять до 24 и более часов (для паст с увеличенным временем удержания). Минимально приемлемый диапазон – от 4 до 8 часов. В целом (но не обязательно), канифольные и безотмывочные пасты обеспечивают большее время удержания, чем пасты, не требующие отмывки.
Упаковка пасты
Способ нанесения пасты определяет вариант упаковки: шприцы (для ручного и автоматического дозирования), банки (для трафаретной печати при ручном нанесении), картриджи (при полуавтоматическом и автоматическом нанесении).
Типичные емкости упаковок: шприцы (обычно 10 и 30 см³), пластмассовые банки (500 г), картриджи (0,5 – 1,5 кг).
Условия хранения и работы с паяльной пастой
Соблюдение условий хранения и обращения с паяльной пастой поможет дольше поддерживать ее характеристики на требуемом уровне, что отразится в меньшем расходе пасты, большем выходе годных изделий, меньшем количестве дефектов. Производители паст указывают следующие параметры, имеющие отношение к хранению и работе с паяльной пастой:
- рекомендуемая температура хранения пасты, °С;
- диапазон допустимых температур хранения пасты, °С;
- минимальное время достижения пастой комнатной температуры, ч.;
- время перемешивания пасты, мин.;
- срок годности пасты при хранении в рекомендуемых условиях, мес.;
- рекомендуемая температура и относительная влажность при нанесении пасты, °С; %.
Чрезмерный нагрев и охлаждение
Паяльные пасты обладают чувствительностью к чрезмерно низким и, в особенности, высоким температурам. Так как основой паст являются два материала с очень разной плотностью (припой и флюс), допускается небольшое естественное расслоение флюса и прочих составляющих пасты, а также образование небольшого приповерхностного слоя флюса. Чрезмерный нагрев в течение длительного времени приводит к значительному расслоению флюса и остальной пасты, образованию толстого приповерхностного слоя флюса. Результатом этого является изменение реологических характеристик пасты и, скорее всего, приведет к появлению дефектов при ее нанесении. Температура выше 30°С может вызвать химическое разложение пасты.
Как правило, производители не рекомендуют подвергать пасты воздействию низких температур. Активаторы флюса могут при этом частично перейти в осадок, что может снизить смачивающую способность пасты. В любом случае, следует провести тесты качества пасты после заморозки, перед использованием в производстве реальных изделий. Некоторые производители, тем не менее, предусматривают хранение своих паст при отрицательных температурах (от –20 до +5°С, [4]).
Воздействие влаги
Проникновение влаги, возможно, является наиболее пагубным воздействием на паяльную пасту. Избыточная влага в пасте вызывает и/или увеличивает окисление припойных шариков, что, в свою очередь, вызывает расход активаторов флюса в большей степени на очистку шариков, чем паяемых поверхностей КП и ЭК. Это может привести к плохому смачиванию либо его полному отсутствию. Также попадание влаги вызывает растекание пасты, что ведет к появлению таких характерных дефектов, как образование перемычек и шариков припоя, разбрызгивание припоя/флюса, смещение ЭК при пайке, уменьшение времени удержания ЭК.
Все пасты в той или иной степени гигроскопичны (впитывают влагу), поэтому следует избегать помещения паст во влажную среду (это замечание в особенности касается паст с водосмываемыми флюсами, но также применимо к пастам с флюсами, не требующими отмывки, и слабоактивированными канифольными флюсами).
Хранение
Согласно общим рекомендациям, паста должна храниться в холодильнике при температуре 4-5°С [2], что предотвращает испарение растворителя и снижает химическую активность пасты в процессе хранения. Некоторые производители рекомендуют более высокую температуру хранения: 8-10°С [3]. Хранение в холодильнике, как правило, в два раза увеличивает срок годности паст по сравнению с хранением при комнатной температуре. В случае хранения при комнатной температуре, необходимо поддерживать ее не выше 25°С при относительной влажности не более 60-80%. Не следует помещать в холодильник начатые банки с пастой – это может вызвать конденсацию абсорбированной влаги, что приведет к описанным выше проблемам. Банки с пастой нужно герметично закрыть и оставить при комнатной температуре для дальнейшего использования. Ряд производителей, тем не менее, рекомендует хранить начатые банки с пастой в холодильнике [3].
Сроки годности паст различны. В большинстве случаев, пасты с водосмываемыми флюсами хранятся в холодильнике от 3 до 6 месяцев, пасты с флюсами, не требующими отмывки – от 6 месяцев до 1 года. Срок хранения паст при комнатной температуре составляет, как правило, 1 – 4 недели [5]. Крайне важно использовать пасты в течение их срока годности, в противном случае возможно появление дефектов, связанных прежде всего с изменившейся вязкостью пасты. При использовании паст рекомендуется использовать принцип FIFO (First In, First Out – в данном случае «первым поступил - первым используется»), с целью недопущения залеживания паст на складе.
Если это необходимо, неиспользованный остаток пасты может некоторое время (обычно не более 12 часов) храниться с целью дальнейшего использования, хотя это и не является рекомендуемой производителями паст практикой. Необходимо снять пасту с трафарета, положить в чистую банку (нельзя перемешивать остатки со свежей пастой) и хранить при комнатной температуре. При дальнейшем использовании следует смешать равные объемы оставшейся и свежей паст, что восстановит ее характеристики и поможет осуществить приемлемую печать. Согласно рекомендациям некоторых производителей паст [1], следует добавлять небольшие объемы старой пасты к новой в течение рабочей смены или всего рабочего дня, с целью минимизировать последствия деградации пасты, а также уверенности в том, что вся старая паста использована перед финальной очисткой трафарета в конце дня. Многие производители не допускают повторного использования остатков пасты. Необходимо помнить, что отказ от их применения обойдется гораздо дешевле последующего ремонта собранных изделий.
Хранить банки, картриджи и шприцы с пастой следует в вертикальном положении, наконечниками шприцов вниз для предотвращения расслоения.
Подготовка к применению
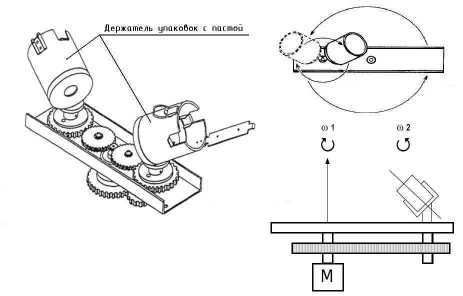
Рис. 1. Рабочий механизм устройства автоматического перемешивания пасты. Фото: MalcomTech.
Перед использованием, паяльную пасту необходимо достать из холодильника и дать ей естественным образом достигнуть температуры окружающей среды. Не следует открывать и перемешивать пасту, пока она не нагрета до комнатной температуры. Типичное время нагрева/стабилизации паяльной пасты – от 4 до 6 часов. Не следует форсировать нагрев пасты и, тем более, нагревать ее в печи – это может привести к расслоению ее компонентов. Если паста используется в холодном состоянии, при нагреве образуется конденсат и произойдет поглощение пастой влаги. К тому же, непрогретая паста имеет тусклый внешний вид, ее сложно перемешивать, будет затруднено качение валика пасты по трафарету, паста может прилипать к ракелю.
Необходимо провести предварительную визуальную инспекцию пасты. Она должна иметь светло- либо умеренно серый цвет, быть достаточно однородной, без комков и посторонних включений, на поверхности не должна присутствовать сухая корка.
После достижения пастой рабочей температуры, необходимо добиться полной однородности ее состава путем перемешивания в банке (неметаллическим шпателем со скругленными углами) легкими движениями в одном направлении от 15-30 секунд до 3 минут (ближе к 1 минуте). Следует избегать сильного и длительного перемешивания пасты, что может привести к избыточному утончению ее слоев и, как следствие, к повышенной растекаемости и/или образованию перемычек.
Пасты в картриджах не требуют перемешивания, их реологические свойства восстанавливаются непосредственно в процессе нанесения.
Существуют устройства, осуществляющие автоматическое перемешивание и подогрев пасты без необходимости предварительного открытия заводской упаковки (что предотвращает окисление, избыточное увлажнение пасты и гарантирует отсутствие воздушных пузырьков при перемешивании). Данные установки обеспечивают стабильный результат вне зависимости от уровня подготовки оператора. Время от начала перемешивания до нанесения пасты на трафарет сокращается до 15 минут.
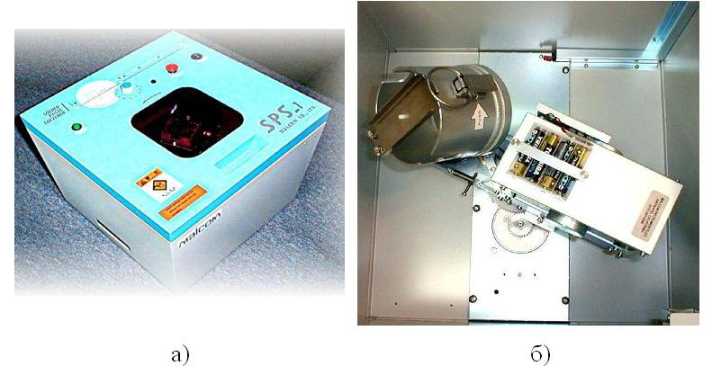
Рис. 2. Устройство автоматического перемешивания пасты: а) внешний вид; б) вид изнутри на рабочий механизм. Фото: MalcomTech.
Такие устройства, как правило, представляют собой центрифугу, на которой закреплено вращающееся коромысло с держателями емкостей с пастой (одной или двух банок, двух картриджей). Осуществляется сложное псевдо-планетарное движение (рис. 1), в процессе которого контейнер с пастой медленно поворачивается на конце коромысла, которое, в свою очередь, вращается с большой угловой скоростью. В результате паста перемешивается внутри контейнеров и одновременно нагревается за счет взаимного трения слоев. Внешний вид и вид на рабочий механизм такого устройств показан на рис. 2.
Список использованных источников
1. Tech-Sheet: Solder Paste Handling Guidelines/AIM. www.aimsolder.com
2. The Quick Pocket Reference For Solder Assembly/AIM. www.aimsolder.com
3. User‘s guidelines for Cobar No-Clean Solder Paste SnPb X-Series/Cobar Europe BV – 2003. www.cobar.com
4. Application Note: Procedures for Handling Solder Paste/Indium Corp. www.indium.com
5. Multicore Solders. Solder Paste Handling Guidelines/Henkel Loctite Adhesives Ltd. – 2004. www.loctite.com
6. Ray P. Prasad. Surface Mount Technology – Principles and Practice. 2nd ed. Kluwer Academic Publishers, Boston, USA, 2002. – 772 p.
7. IPC-TM-650. Test Methods Manual. Online-версия. www.ipc.org
8. IPC/EIA J-STD-005. Requirements for Soldering Pastes, Includes Amendment 1 – 1995. webvision.ipc.org
9. IPC/EIA J-STD-004. Requirements for Soldering Fluxes – 2004. webvision.ipc.org
10. Материалы фирмы AIM. www.aimsolder.com
11. Материалы фирмы Kester. www.kester.com
12. Материалы фирмы Cobar. www.cobar.com
13. Материалы фирмы Loctite. www.loctite.com
14. Материалы фирмы Indium. www.indium.com
15. Материалы фирмы MalcomTech. www.malcomtech.com
|