15 января 2013
Стойкость бессвинцовых сплавов к ударным (динамическим) нагрузкам. Эффект микродобавок
Статья предоставлена компанией «Itecs»
www.alphametals.ru
Впервые опубликовано в журнале «Технологии в электронной промышленности», №7/2012
Авторы: Ранджит С Пандер (Ranjit S Pandher), Брайен Г Левис (Brian G Lewis), Рагхасудха Вангавети (Raghasudha Vangaveti), Бава Сингх (Bawa Singh)
Перевод: Виталий Щекин, Алексей Максимов
info@alphametals.ru
Краткое описание
Вопрос надёжности паяных соединений является одной из основных тем в электронной промышленности частично из-за постоянно растущей популярности мобильных электронных устройств и частично ввиду перехода на бессвинцовые паяльные материалы. Большинство рекомендуемых бессвинцовых сплавов (Pb-free) – это сплавы с большим содержанием олова (high Sn) и относительно высоким показателем модуля упругости и прочности. Это и играет ключевую роль в вопросе надёжности бессвинцовых паяных соединений. Более того, несмотря на то, что именно олово в припойных сплавах принимает основное участие в образовании паяного соединения, интерметаллические соединения, образованные использованием оловянно-свинцовых (SnPb) и бессвинцовых сплавов (Pb-free), могут различаться. На качество паяного шва также влияет и очевидно различающиеся режимы процесса для оловянно-свинцовых и бессвинцовых сплавов.
Хрупкий излом паяных соединений при термоударах образуется вблизи или непосредственно в промежуточном слое (слоях) интерметаллических соединений. Это происходит из-за хрупких свойств интерметаллических соединений, дефектов как внутри, так и на границе интерфейсов, а также в результате передачи напряжений промежуточным слоям по причине низкой вязкости припоя.
В процессе работ по улучшению характеристик сплавов компанией Cookson Electronics учитывались два основных направления – это повышение вязкости припоя, а также модифицированный контроль интерметаллических слоев. Широкий диапазон основных составов сплавов вместе с отобранными микросплавными добавками к сплавам на основе SnAgCu оценивались с целью контроля механических свойств и процессов диффузии, действующих при образовании и росте промежуточных интерметаллических слоев.
В данной статье приведены результаты глубокого изучения ряда микросплавных добавок. Сплавы-добавки обычно действуют как модификаторы диффузного отражения молекул, снижая взаимную диффузию между подложками и припоем, а также уменьшая как толщину интерметаллических соединений, так и вероятность образования пустот. В качестве альтернативного варианта можно использовать добавки, которые действуют как компенсаторы диффузии. Следует отметить, что уровень микродобавок не изменяет значительно объёмные механические свойства основных сплавов. Наши результаты, основанные на испытаниях на ударопрочность, демонстрируют возможность значительных улучшений надёжности паяных соединений.
Введение
По мере перехода электронной промышленности к бессвинцовой пайке SAC 305 и SAC 405 cтали наиболее распространенными сплавами благодаря самой низкой по сравнению с остальными сплавами температурой плавления, эвтектическому составу, а также хорошим циклическим усталостным характеристикам. Однако, всё же, несмотря на соответствие большинству требований для успешной бессвинцовой пайки нельзя не упомянуть и некоторые сомнения, возникшие по мере увеличения основных характеристик используемых сплавов. Прежде всего, такие сомнения были связаны с различиями в результатах и эффективности процесса. Одновременно с развитием технологий бессвинцовых сплавов во всём мире развился и значительный интерес к производству мобильной электроники. Эти устройства подчёркивали необходимость хорошей устойчивости к ударным нагрузкам, а ведь именно в этой области как у сплава SAC 305, так и у других сплавов SAC с относительно высоким содержанием серебра (Ag) имеются значительные недостатки.
Главная причина слабой скорости деформирования сплавов SAC 305 в сравнении с эвтектическими оловянно-свинцовыми сплавами кроется в объёмных свойствах сплавов. Большинство бессвинцовых припоев содержат большое количество олова, а содержание серебра и меди составляет 5% и 1% соответственно. У таких сплавов относительно высокая прочность и эластичность, но более низкое полное акустическое сопротивление, поэтому при ударных нагрузках больше вероятность передачи напряжений границам раздела между припоем и подложкой. Интерметаллические соединения (IMC), формирующиеся в процессе пайки, имеют малую вязкость, поэтому именно на данной границе раздела и возникает хрупкий излом при тестировании на ударопрочность.
В качестве замены SAC-сплавам с высоким содержанием серебра, использующихся в корпусах BGA и CSP, предлагалось большое число проверенных и широко обсуждаемых в специальной литературе сплавов. Первым учитываемым фактором являются объёмные свойства сплава. Эффект увеличения прочности сплавов с высоким содержанием олова можно минимизировать посредством выбора сплавов с малым содержанием серебра. При снижении содержания серебра в сплаве становится меньше интерметаллических соединений Ag3Sn и, следовательно, уменьшается механическая прочность. На рисунке 1 показана прочность на сдвиг семейства сплавов SAC. Сплавы с меньшим содержанием серебра имеют преимущество в потенциальном снижении эффекта высокой скорости деформации.
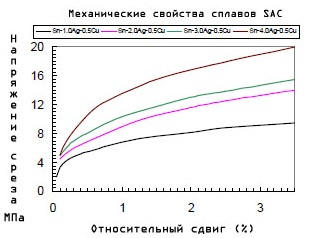
Рис. 1. Механические свойства серебросодержащих сплавов SAC
Вторым изученным фактором является происхождение и количество образующихся в процессе пайки интерметаллических соединений (IMC). Данная область более сложная. Высокая скорость образования хрупких изломов может проявиться при пайке бессвинцовым припоем на всех подложках, включая OSP Cu, ENIG, матовые Ni и подложки с плёнками (Au/Ni), нанесённые распылением. Образуемые пограничные интерметаллические соединения определяются синхронными фазами (свободной энергией) припоя с высоким содержанием олова и подложки таким образом, что, например, при пайке SAC-сплавом Cu6Sn5 будет синхронной фазой на границе раздела между припоем и подложкой, а Cu3Sn соответственно в равновесии с подложкой. Качество образованных интерметаллических соединений зависит от времени пайки, температуры и последующих условий старения компонентов. Вероятность хрупкого излома определенной границы раздела зависит от состава интерметаллического соединения, например, из двух бинарных интерметаллических соединений CuSn Cu3Sn более хрупок и отличается также толщиной интерметаллического соединения и наличием таких дефектов, как поры Киркендалла, медленно развивающиеся трещины и остаточное напряжение между слоями интерметаллических соединений, например, (Ni,Cu)6Sn5 и (Ni,Cu)3Sn4 [2,3]. Увеличения стойкости к ударным нагрузкам можно добиться контролем, как за начальным образованием интерметаллических соединений, так и за их последующим развитием в течение срока службы устройства, включая дефекты интерметаллических соединений.
В ходе работ по улучшению характеристик припоев компания Cookson Electronics исследовала вязкость SAC-сплавов с низким содержанием серебра, улучшенными свойствами смачивания и растекаемости, включая модификацию и контроль за интерметаллическими соединениями посредством преобразования и комбинирования микросплавных добавок.
В данном исследовании сравнивается производительность семейства сплавов SAC как с содержащими микродобавки запатентованными сплавами SACX, так и со сплавами SACX без микродобавок. Роль серебра и меди в сплавах SAC напрямую зависит от Cu6Sn5 и Ag3Sn, упрочняющие матрицу Sn. Снижение содержания серебра и поддержание уровня содержания меди для контроля за растворением подложки, а также добавление висмута (Bi) для улучшения характеристик смачивания и усталостной прочности [4] составили основу сплава для развития микродобавок.
В процессе обсуждения влияния микросплавных добавок на изменение процесса развития интерметаллических соединений установлена прямая зависимость соединений от самих добавок. Так, И.Андерсон вместе с другими специалистами [5] указывает на улучшения в структуре хрупкого излома SAC-сплавов при добавлении кобальта (Co) и железа (Fe) с учётом снижения скорости растворения меди из подложки. При этом снижается вероятность образования как хрупкой фазы Cu3Sn, так и пустот. Ф. Гао [6] в процессе обсуждения данного вопроса говорит о похожей реактивной диффузии при добавлении кобальта и никеля (Ni) на базе термодинамических моделей и делает вывод о том, что кобальт и никель обладают большим сродством с оловом, чем с медью и их разветвление может образовать Cu6Sn5 посредством зарождения и роста Cu3Sn. В отсутствии добавок к переходным металлам диффузия по границам зёрен может привести к значительному росту интерметаллических соединений. Степень блокирования роста Cu3Sn при добавлении небольшого количества никеля показана на рисунке 2.
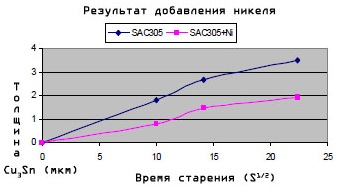
Рис. 2. Образование интерметаллических соединений у сплавов SAC305 и SAC3DS + 0,1% Ni
Параллельно компания Cookson создала ряд бессвинцовых сплавов на оловянно-цинковой основе (SnZn) с низкой температурой пайки [7]. Наличие в составе этих сплавов микродобавок в виде индия (In), никеля, железа и кобальта оказалось эффективным при модификации эвтектического состава, целью которой было уменьшение содержания цинка для улучшения коррозионной устойчивости и образования высокомобильных диффундирующих веществ, например, индия, которые действуют как «компенсаторы» диффузии, минимизируя поры Киркендалла у паяных соединений, образованных с использованием сплавов олово - цинк — медь.
В данной работе показан процесс относительной деформации у SAC-сплавов с низким содержанием серебра при комбинированном добавлении висмута, никеля, хрома (Cr), германия (Ge) и индия. Микродобавки выбирались с целью оптимизации объёмных характеристик сплава, изменения особенностей образования интерметаллических соединений и улучшения характеристик окисления припойного сплава.
Ход испытаний
Испытания проводились на установках для тестирования соединений Dage 4000 и Dage 4000 HS. Установка Dage 4000 способна выполнять проверку шариковых выводов на целостность и надёжность со скоростью до 15 мм/сек, а Dage 4000 HS выполняет аналогичную процедуру со скоростью до 1000 мм/сек. Все испытания проводились с использованием сфер размером 18 мил (450 мкм), собранных на подложках типа CABGA100 и сфер размером 12 мил (300 мкм), смонтированных на подложках CBGA84, где для покрытия контактной площадки применялся сплав никель-золото (NiAu). Сферы монтировались с использованием пастообразного водорастворимого флюса (Alpha WS9180-M3), наносившегося на подложки через трафарет. Установка сфер проходила методом простого ручного монтажа и оплавления в среде воздуха в конвекционной печи оплавления, состоящей из семи зон. Два сплава с низким содержанием серебра на основе олово-серебро-медь (SAC105: Sn1,0Ag0,5Cu) и SACX: Sn0,3Ag0,7Cu0,1Bi), а также обычные SAC-сплавы SAC405 и SAC305 для сравнения использовались с рядом микродобавок. Образцы, не прошедшие испытания, сгруппированы в соответствии с выявленным дефектом, как показано на рисунке 3.
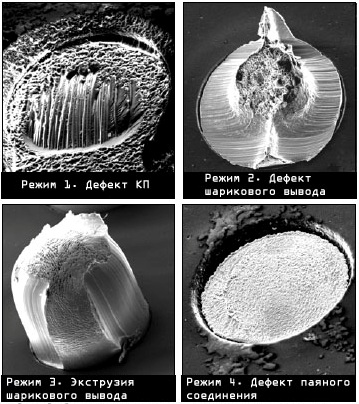
Рис. 3. Режимы отказа шариковых выводов при растяжении. Изображения со сканирующего электронного микроскопа
Режим 1 – Дефект контактной площадки. Контактная площадка отслаивается от подложки, что указывает на плохое качество платы или подложки.
Режим 2 – Дефект шарикового вывода. Наиболее распространённая неисправность, которая указывает на вязкое разрушение паяльного материала.
Режим 3 – Экструзия шарикового вывода. Возникает из-за неправильного расположения используемого для монтажа инструмента или по причине чрезмерной твёрдости припоя.
Режим 4 – Неисправность стыковых или интерметаллических соединений. Дефект образуется на границе между припоем и контактной площадкой. Данная неисправность может иметь большее максимальное значение силы и преимущественно проявляется как хрупкий излом.
Высокоскоростное испытание на деформацию
Испытания на ударную прочность проводились в соответствии со стандартом JEDEC JESD22-B111, применяемым для определения воздействия ударной нагрузки на электронные мобильные устройства [8]. Однако данный метод испытаний требует много времени и затрат. На корпусах BGA и CSP для оценки качества паяной сферы можно использовать метод проверки на растяжение и на срез. В процессе испытаний удалось показать, что высокая скорость среза и высокая скорость деформации шарикового вывода, определённые тестером DAGE 4000 HS , имитируют воздействие ударной нагрузки [9, 10]. Помимо воздействия высокой температурой (150ºC) и увеличения количества фаз интерметаллических соединений стандартные испытания на растяжение и срез с помощью тестера DAGE 4000 могут воспроизводить результаты испытаний на удар.
В данном исследовании упоминается комбинация высокоскоростных испытаний на растяжение и на удар на узлах типа CABGA100 с использованием оборудования для испытаний на удар от компании Lansmont (рис. 4).
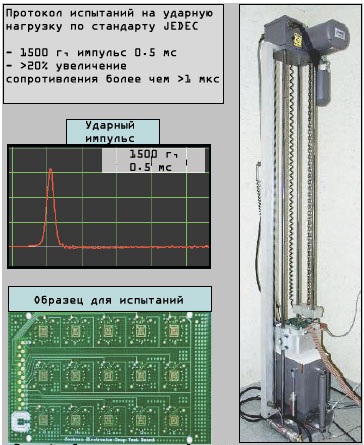
Рис. 4. Система испытаний на ударную прочность и протокол испытаний по стандарту JEDEC
В дополнение к высокоскоростным испытаниям на растяжение и ударную нагрузку также исследовались характеристики смачивания и растекания сплавов. Сферы размером 12 мил помещались на флюс, нанесенный методом трафаретной печати на образец для испытаний, предварительно покрытый органическим защитным покрытием. Затем в воздушной среде конвекционной печи, состоящей из семи рабочих зон, проведено оплавление. Тестовые образцы с органическим защитным покрытием использовались для улучшения смачиваемости. После оплавления образцы погружались в горячую воду для удаления твёрдых остатков флюса. В процессе оплавления припой смачивает поверхность и растекается. Затем измеряется область смачиваемой поверхности и определяется коэффициент растекаемости как относительное увеличение в области, относящейся к выступающему поперечному сечению сферы.
|