Скоро!
Событий нет.
|
 |
14 июня 2007
Режимы пайки оплавлением
Введение
Создание оптимального температурного профиля оплавления является одним из важнейших факторов в обеспечении качества паяных соединений, получаемых на печатной плате методом поверхностного монтажа. Температурный профиль непосредственно влияет на ряд характеристик сборки:
- распределение температур по площади печатной платы (ПП);
- способность припойной пасты к смачиванию;
- очищающую способность флюса;
- микроструктуру паяных соединений;
- плоскостность ПП;
- уровень остаточных напряжений в сборке и т.д.
Профиль представляет собой зависимость температуры, воздействию которой подвергается сборка в печи, от времени. В типичном профиле оплавления выделяют четыре этапа (рис. 1):
- предварительного нагрева;
- выдержки/активации флюса;
- оплавления;
- охлаждения.
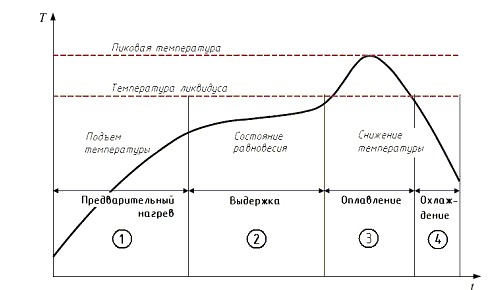
Рис. 1. Типичный профиль оплавления и его деление на этапы
Основными параметрами профиля оплавления на каждом этапе являются: максимальная и минимальная температура, скорость нагрева/охлаждения (наклон данного участка профиля), время выдержки. Неправильное построение профиля может приводить к образованию различных дефектов, в частности, растрескиванию керамических и пластиковых корпусов ЭК и короблению ПП, образованию шариков припоя, пустот в паяных соединениях и пр.
Ниже приведены рекомендованные значения параметров для каждого этапа температурного профиля для типовых эвтектических припоев Sn63/Pb37 и Sn62/Pb36/Ag2. Также рассмотрены особенности создания профиля при использовании бессвинцовых припоев (как правило, группы Sn/Ag/Cu).
Этап предварительного нагрева
В течение данного этапа паяльная паста высушивается, испаряются ее наиболее летучие компоненты (органические наполнители), удаляется влага из ЭК и ПП. Скорость подъема температуры обычно составляет 1 – 3°С/сек (по данным [2] 2 – 4°С/сек), максимальная температура составляет от 100 до 150°С. Более быстрый рост температуры приводит к разбрызгиванию паяльной пасты, образованию шариков и перемычек припоя, а также может вызвать повреждения термочувствительных ЭК (появление трещин в керамических чип – резисторах и т.д.). Бессвинцовые сплавы требую более высоких температур предварительного нагрева – до 150 – 200°С.
Выдержка
При выдержке происходит минимизация градиентов температур компонентов и всех областей ПП, активация флюса, очистка паяемых поверхностей. Скорость подъема температуры выбирается предельно низкой. Температура в конце этапа приближается к точке плавления (130 – 170°С для эвтектических припоев, 180 – 200°С для бессвинцовых). Следствием слишком быстрого подъема температуры является недостаточное флюсование и образование шариков припоя; с другой стороны, низкая скорость обуславливает избыточное окисление пасты и, в результате, ее разбрызгивание, а также увеличивает без необходимости время операционного цикла. Время выдержки составляет 60 – 90 сек, иногда до 120 – 150 сек. Рекомендуется, чтобы разница температур между фазами предварительного нагрева и оплавления была меньше 100°С.
Оплавление
В процессе оплавления температура повышается на 1 – 3°С/сек. Чтобы избежать перемычек припоя, недостаточной смачиваемости, эффектов «холодной» пайки и коробления, необходимо выдерживать паяемые ЭК при температуре выше точки плавления (183°C для Sn63, 179°C для Sn62, 217°C для бессвинцовых) по меньшей мере в течение 30 – 90 сек (предпочтительно 60 сек.). Меньшие значения (30 – 60 сек) рекомендуются в случае использования покрытий HASL и OSP, большие (60 – 90 сек) – для покрытий на основе никеля. Температура должна быть достаточной для обеспечения хорошего смачивания и флюсования (обычно – 215 – 220°C) и на 30 – 40°С превышать температуру эвтектики. ЭК должен находиться при температуре, отличающейся от пиковой не более чем на 5°С, в течение 10 – 30 сек. Более длительная, чем необходимо, выдержка ведет к избыточному росту интерметаллических соединений, что придает паяному соединению хрупкость и уменьшает его усталостную прочность. Также повышенная температура может активизировать окисление пасты, что ухудшает смачивание. Температура корпуса ЭК, которая может отличаться от температуры выводов на 15°С, не должна превосходить 220°С. Небольшие ЭК (объем корпуса V<350 мм3) подвергаются большему нагреву, чем крупные. Максимальное значение температуры корпуса для небольших ЭК составляет 240°С. В процессе оплавления не должно происходить изменения цвета или обугливания ПП. Бессвинцовые припои отличаются более высокими температурами оплавления: 240 – 260°С.
Пиковая температура в процессе оплавления имеет нижний и верхний пределы. Нижний предел – температура, минимально необходимая для получения надежных паяных соединений (определяется, прежде всего, характеристиками припойной пасты). Верхний предел – максимальная температура оплавления, которая должна быть ниже, чем:
- тестовая температура, используемая для оценки уровня чувствительности корпуса ЭК к влажности (MSL);
- температура, при которой происходит повреждение ПП.
Диапазон между нижним и верхним пределами пиковой температуры определяет т.н. «окно» процесса. Шириной этого окна для традиционной технологии составляет около 35°С. Для бессвинцовых сплавов окно процесса существенно уже (10 – 20°С), и существенно возрастают требования к контролю параметров процесса.
Обеспечение однородного нагрева ПП
Эффективность процесса пайки оплавлением в значительной степени определяется равномерностью распределения температуры по площади ПП, для обеспечения которой многие производители конвекционных печей применяют ряд специальных технологий. В особенности этот фактор важен при пайке больших ПП, а также для бессвинцовой технологии. Обычные печи оплавления могут иметь значительные температурные градиенты между различными областями ПП, вызванные их неравномерным нагревом, разницей в объемах, скоростях, давлениях и направлениях перемещения воздушных потоков.
В частности, компания ERSA [9] разработала и применяет в своих продуктах технологию Multijet. Согласно данной технологии, благодаря принудительному контролю конвекции (Forced Convection Control) создается постоянный, равномерный и однородный воздушный поток, увеличивается коэффициент теплопередачи и снижается градиент температур по всей площади ПП. Так как направление обратного воздушного потока от ПП строго вертикально, и он проходит рядом с каждым индивидуальным соплом, то происходит сокращение областей низкого давления и турбулентности, а также поперечных воздушных потоков (рис. 2).
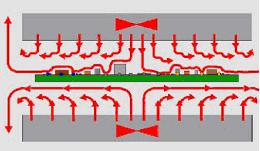
а)
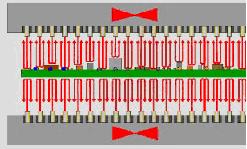
б)
Рис. 2. Распределение тепловых потоков в конвейерной печи: а) неконтролируемое и неравномерное; б) принудительный контроль конвекции, согласно технологии Multijet, обеспечивает равномерное распределение воздушных потоков. Источник: ERSA GmbH [9].
Компания Novastar [10] применяет технологию горизонтальной конвекции (Horizontal Convection), при которой воздух циркулирует над ПП в одном направлении, и под ПП – в противоположном, формируя воздушный «циклон», обтекающий плату вдоль горизонтальной оси конвейерной печи (рис. 3). Так как поток как на верхней, так и на нижней стороне ПП направлен от периферии платы к ее центру, это снижает обычный перегрев центральной части ПП относительно периферийных областей. Равномерность скорости, давления и объема воздушного потока достигается равенством поперечных сечений верхней и нижней части рабочей камеры, однородность потока обеспечивается направлением его перемещения параллельно ПП, что дополнительно улучшает условия пайки ЭК с выводами, располагающимися под корпусом (BGA).
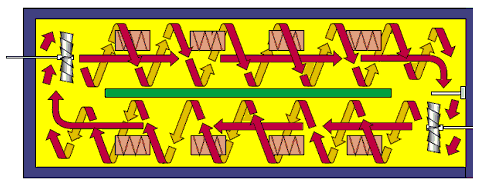
Рис. 3. Горизонтальная конвекция (воздушный «циклон», обтекающий ПП с двух сторон. Источник: APS NOVASTAR LLC [10]
Для обеспечения минимального градиента пиковых температур при оплавлении, фирма Speedline Technologies (торговая марка Electrovert) [11] предлагает технологию «heat-on-intake» (нагрев через диффузор, рис. 4), заключающуюся в наличии трех независимых камер для смешивания рабочего газа, оснащенных своими впускными отверстиями. Предварительно нагретый рабочий газ перемешивается вентилятором и создает в каждой камере мягкое обратное давление на ее нижнюю панель (диффузор). Такое давление создает воздушный поток в виде концентрических расходящихся окружностей, которые частично перекрываются на уровне ПП и обеспечивают эффективную и равномерную теплопередачу. Пиковые температуры, таким образом, поддерживаются в диапазоне ±3° C (±1,5° C с опционными нагревателями) для ПП шириной до ≈600 мм (24”).
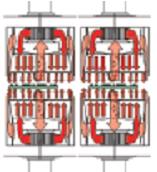
Рис. 4. Технология «heat-on-intake» для обеспечения минимального градиента пиковых температур. Источник: Speedline Technologies [11]
Охлаждение
Процесс пайки считается завершенным, когда сборка охлаждается с образованием прочных паяных соединений. Скорость охлаждения непосредственно влияет на получаемую микроструктуру соединения, а она, в свою очередь, на его механические свойства. Высокая скорость охлаждения уменьшает размер зерна интерметаллических соединений и упрочняет паяные соединения, увеличивает усталостную прочность, соединение получается более блестящим. С другой стороны, быстрое охлаждение вызывает остаточные напряжения в материалах с различными ТКР и коробление ПП. Вследствие этого, следует контролировать процесс охлаждения – как правило, снижением скорости в зависимости от возможностей печи (скорости воздушного потока, расположения нагревательных элементов, ширины конвейера и т.д.). Рекомендуемые значения скорости составляют 3 – 4°С/сек до 130 °С (не более 4°С/сек).
Время нахождения платы под воздействием температуры выше температуры стеклования Tg (125° – 175°C) должно быть менее 4 минут. Продолжительность процесса оплавления при подъеме температуры от 45°C до пиковой (215 ± 5°C) составляет, как правило, от 3,5 до 4 минут; общее время пребывания платы в печи – от 4 до 6 минут.
Параметры профилей оплавления, рекомендованных ассоциацией JEDEC, приведены в таблице 1 и таблице 2. Следует отметить, однако, что эти профили использовались для оценки уровня чувствительности корпусов ЭК к влажности (MSL), но не для регулярного оплавления. Поэтому приведенные ниже в таблицах 1 – 4 цифры являются верхней границей допустимых значений – выше них целостность корпусов не гарантируется.
Таблица 1. Профиль оплавления для эвтектического сплава (JEDEC J-STD-020С)
Средняя скорость подъема температуры (Ramp up) от TL до TP |
max 3°C/сек |
Температурный диапазон предварительного нагрева |
100 – 150°C |
Время выдержки при предварительном нагреве |
60 – 120 сек |
TL |
183°C |
Время выдержки при T>TL |
60 – 150 сек |
Время выдержки в коридоре 5°C от TP |
10 – 30 сек |
Средняя скорость охлаждения (Ramp down) |
max 6°C/сек |
Время нахождения платы при температуре от 25°C до TP |
6 мин max |
Таблица 2. Профиль оплавления для бессвинцового сплава (JEDEC J-STD-020С)
Средняя скорость подъема температуры (Ramp up) от TL до TP |
max 3°C/сек |
Температурный диапазон предварительного нагрева |
150 – 200°C |
Время выдержки при предварительном нагреве |
60 – 120 сек |
TL |
217°C |
Средняя скорость подъема температуры (Ramp up) от 200°C до 217°C |
max 3°C/сек |
Время выдержки при T>TL |
60 – 150 сек |
Время выдержки в коридоре 5°C от TP |
20 – 40 сек |
Средняя скорость охлаждения (Ramp down) |
max 6°C/сек |
Время нахождения платы при температуре от 25°C до TP |
8 мин max |
В приведенных выше таблицах: TL – температура эвтектики; TP – пиковая температура.
Пиковые температуры, как уже упоминалось выше, зависят от толщины и объема корпуса ЭК (таблица 3 и таблица 4).
Таблица 3. Эвтектический сплав – пиковые температуры оплавления TP (JEDEC J-STD-020С)
Толщина корпуса, мм |
При объеме корпуса <350 мм3 |
При объеме корпуса ≥350 мм3 |
<2,5 |
240+0-5°C |
225+0-5°C |
≥2,5 |
225+0-5°C |
225+0-5°C |
Таблица 4. Бессвинцовая технология – пиковые температуры оплавления TP (JEDEC J-STD-020С)
Толщина корпуса, мм |
При объеме корпуса <350 мм3 |
При объеме корпуса 350-2000 мм3 |
При объеме корпуса <2000 мм3 |
<1,6 |
260°C |
260°C |
260°C |
1,6-2,5 |
260°C |
250°C |
245°C |
>2,5 |
250°C |
245°C |
245°C |
Начать составление профиля рекомендуется с рекомендаций производителя паяльной пасты. Окончательный выбор режимов производится технологом исходя из конструкции печатной платы, типоразмеров компонентов, плотности монтажа, особенностей используемого оборудования, результатов экспериментальных паек.
В перечне технических характеристик ЭК производителем, как правило, указана максимально допустимая скорость изменения температуры (нагрева и, в особенности, охлаждения). При соблюдении данных рекомендаций производитель гарантирует определенный уровень отказов компонентов. Эти данные могут быть основаны как на приведенных выше рекомендациях JEDEC (например, максимальная скорость охлаждения составляет 6°C/сек для BGA-компонентов TI [23] и усилителей мощности RMPA2266 Fairchild [24]), так и отличаться от них в меньшую сторону (например, для модулей DC/DC Ericsson серии PKF [25] эти значения составляют 1–5°C/сек, для генераторов, управляемых напряжением фирмы M/A-COM [26] – 2°C (не допускается форсированное охлаждение), для инфракрасных приемопередатчиков Sharp GP2W0004YP/XP [27] – 1–4°C/сек).
Бессвинцовая технология предусматривает более высокие температуры оплавления, поэтому необходимо более длительное охлаждение и, соответственно, печи с бо́льшим количеством зон охлаждения. Чем больше таких зон предусмотрено в конструкции конвейерной печи, тем более точную отработку требуемого градиента температур она может обеспечить. Существуют модели печей с 8 такими зонами (суммарная длина зон охлаждения – 1,6 м).
Сравнение профилей RSS и RTS
Современные многозонные конвейерные печи оплавления с применением принудительной конвекции обеспечивают быстрый и контролируемый прогрев собираемого модуля, независимо от различий в высоте ЭК, цвете и текстурах их поверхностей. Также практически отсутствуют эффекты затенения и заметный градиент температур между различными областями ПП, что в значительной степени снижает необходимость длинного этапа выдержки. Вследствие этого для современных конвекционных печей и паст с не требующими отмывки флюсами все более широко применятся отличный от показанного на рис. 1 традиционного RSS (Ramp – Soak – Spike, «наклон – выдержка – пик») оптимизированный тип профиля, названный RTS (Ramp – To – Spike, «наклон – пик»). Сравнение профилей приведено на рис. 5.
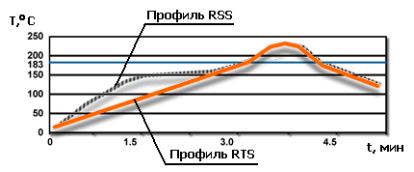
Рис. 5. Сравнение профилей оплавления RSS и RTS. Источник: Surface Mount Technology (SMT) [21]
Согласно рис. 5, профиль RTS в части нагрева представляет собой линейный участок подъема от температуры окружающей среды до пиковой. Этот участок профиля служит одновременно зоной предварительного нагрева, удаления летучих составляющих, активации флюса и выравнивания градиентов температур. Обычно скорость здесь составляет 0,6 – 1,8°С/сек. Первые 90 секунд подъема должны быть строго линейны.
Простое эмпирическое правило для скорости заключается в том, что 2/3 профиля должны лежать ниже линии T=150°С. При более высокой температуре активирующая способность большинства паяльных паст начинает быстро деградировать. Если следовать данному правилу, результатом будет лучшее смачивание и получение более блестящих паяных соединений.
Пиковая температура в зоне оплавления должна поддерживаться на уровне 215°C ± 5°C, при этом время нахождения при температуре выше температуры ликвидуса – 60 ± 15 сек. Как и для профиля RSS, продолжительность процесса оплавления при подъеме температуры от окружающей среды до пиковой должна составлять 3,5 – 4 минуты.
В случае применения RTS-профиля, по сравнению с RSS, ожидается меньшее количество проблем с паяемостью ЭК, что обусловлено поддержанием активности флюса на протяжении всего длинного этапа предварительного нагрева. Благодаря жесткому контролю скорости подъема температуры, существует гораздо меньшая вероятность термического удара и образования прочих дефектов. Процесс более экономичен, так как для первой половины конвейерной печи необходима меньшая тепловая энергия. Данный процесс рекомендован многими производителями ЭК для бессвинцовой пайки.
Данные рекомендации формируют общее представление о температурных профилях, этапах и режимах оплавления. В последующих статьях будут даны рекомендации по осуществлению контроля параметров профилей, а также обзор типичных дефектов пайки, связанных с неправильным термопрофилированием, и методы их устранения.
Список использованных источников
- IPC/JEDEC J-STD-020C. Moisture/Reflow Sensitivity Classification for Non-hermetic Solid State Surface Mount Devices. Generic Standard on Printed Board Design – 2004. www.jedec.org
- Application Note: Soldering Guidelines for Module PCB Mounting Rev. 5/ANADIGICS, Inc., – 2004 . www.anadigics.com
- Reflow Soldering Guidelines for Surface-Mount Devices. Application Note 81/Altera Corporation – 2002. www.altera.com
- Surface mount reflow soldering description. AN10365/Philips Semiconductors – 2006. www.standardics.nxp.com
- CHAPTER 4. SOLDERING GUIDELINES AND SMD FOOTPRINT DESIGN/Philips Semiconductors – 2004. www.nxp.com
- Guidelines for Soldering Surface Mount Components to PC Boards. Application Note 7528/Fairchild Semiconductors – 2002. www.fairchildsemi.com
- Device Package User Guide/Xilinx, Inc. – 2006. www.xilinx.com
- Implementation and Solder Reflow Guidelines for Pb-Free Packages/Xilinx, Inc. – 2006. direct.xilinx.com
- HOTFLOW 2 Series – The Lead Free Generation of Reflow Soldering Equipment /ERSA GmbH. www.ersa.de
- Emerging Horizontal Convection reflow technologies/P. John Shiloh – SMT, Feb. 2003. www.novastarinc.com
- Speedline Technologies. Electrovert OmniExcel® Series Reflow Soldering System/Speedline Technologies. www.speedlinetech.com
- Ray P. Prasad. REFLOW SOLDER PROFILE DEVELOPMENT. www.ecd.com
- Bob Rooks. ROBUST REFLOW PROFILE DESIGN. www.ecd.com
- Ray P. Prasad. General Considerations for Developing Solder Profile/Surface Mount Technology (SMT) – 2002. smt.pennnet.com
- P. John Shiloh. How to Profile a PCB/Surface Mount Technology (SMT) – 2000. smt.pennnet.com
- Ronald C. Lasky, Bjorn Dahle. Optimizing Reflow/Surface Mount Technology (SMT) – 2004. smt.pennnet.com
- Denis Barbini, Gerjan Diepstraten, Ursula Marquez. Process Considerations for Optimiz-ing a Reflow Profile/Surface Mount Technology (SMT) – 2005. smt.pennnet.com
- David Scheiner. Reflow Profile Optimization/Surface Mount Technology (SMT) – 2003. smt.pennnet.com
- Phil Zarrow. Soldering/Surface Mount Technology (SMT) – 2000. smt.pennnet.com
- Karen Walters. Step 7: Soldering/Surface Mount Technology (SMT) – 2002. smt.pennnet.com
- David Suraski. The Benefits of a Ramp-to-Spike Reflow Profile/Surface Mount Technology (SMT) – 2000. smt.pennnet.com
- Ray P. Prasad. Surface Mount Technology – Principles and Practice. 2nd ed. — Kluwer Academic Publishers, Boston, USA, 2002. – 772 p.
- Design Summary for 56GQL (48- and 56-pin functions) MicroStar Junior BGA/Texas Instruments, Inc. – 2000. focus.ti.com
- RMPA2266 i-Lo™ WCDMA WCDMA Power Amplifier Module, 1920–1980 MHz/Fairchild Semiconductor – 2006. www.fairchildsemi.com
- DC/DC power modules. PKF series. General information/Ericsson Microelectronics AB. www.ericsson.com
- Reflow Soldering Conditions for VCO and Synthesizer Products/M/A-COM Division of AMP Incorporated. www.macom.com
- IrDA Technical Information. GP2W0004YP/XP Infrared Transceiver/Sharp Corp. – 2002. document.sharpsma.com
|
 |
|