Скоро!
Событий нет.
|
 |
24 июня 2007
Основы технологии монтажа в отверстия. Часть I
Введение
Технология монтажа в отверстия (Through Hole Technology, THT), также называемая иногда штырьковым монтажом , является родоначальником подавляющего большинства современных технологических процессов сборки электронных модулей. Также существует ряд распространенных, но не совсем корректных названий данной технологии, например, DIP-монтаж (название происходит от типа корпуса – Dual In-Line Package – корпус с двухрядным расположением выводов, широко применяемого, но не единственного в данной технологии) и выводной монтаж (название не совсем корректно, поскольку монтаж компонентов с выводами применяется и во многих других технологиях, в т. ч. в поверхностном монтаже).
Фактически данная технология появилась вместе с началом использования монтажных плат, как метода выполнения электрических соединений. До этого монтаж компонентов осуществлялся пространственно путем крепления выводов компонентов к металлическим контактам на конструктивных элементах устройства, либо соединением выводов компонентов между собой. Применение монтажных плат перенесло конструирование узлов из пространства на плоскость, что значительно упростило как процесс разработки конструкций, так и изготовление устройств. Появление печатного монтажа в дальнейшем привело к революции в технологичности и автоматизации проектирования электронных устройств.
Технология монтажа в отверстия, как следует из названия, представляет собой метод монтажа компонентов на печатную плату, при котором выводы компонентов устанавливаются в сквозные отверстия платы и припаиваются к контактным площадкам и/или металлизированной внутренней поверхности отверстия.
Широкое распространение технология монтажа в отверстия получила в 50-х – 60-х годах XX века. С тех пор значительно уменьшились размеры компонентов, увеличилась плотность монтажа и трассировки плат, было разработано не одно поколение оборудования для автоматизации сборки узлов, но основы конструирования и изготовления узлов с применением данной технологии остались неизменны.
В настоящее время технология монтажа в отверстия уступает свои позиции более прогрессивной технологии поверхностного монтажа, в особенности, в массовом и крупносерийном производстве, бытовой электронике, вычислительной технике, телекоммуникациях, портативных устройствах и других областях, где требуется высокая технологичность, миниатюризация изделий и хорошие слабосигнальные характеристики.
Тем не менее, есть области электроники, где технология монтажа в отверстия по сей день является доминирующей. Это, прежде всего, силовые устройства, блоки питания, высоковольтные схемы мониторов и других устройств, а также области, в которых из-за повышенных требований к надежности большую роль играют традиции, доверие проверенному, например, авионика, автоматика АЭС и т.п.
Также данная технология активно применяется в условиях единичного и мелкосерийного многономенклатурного производства, где из-за частой смены выпускаемых моделей автоматизация процессов неактуальна. Эта продукция, в основном, выпускается небольшими отечественными предприятиями как для бытового, так и для специального применения.
Некоторое время назад имела место ситуация, когда выбор технологии монтажа в отверстия мог быть продиктован применяемыми компонентами. Некоторые компоненты попросту не выпускались в корпусах для поверхностного монтажа. Особенно это было актуально для нашей страны, поскольку новинки доходили до нас с опозданием. Сейчас эта ситуация существенно изменилась, и большинство компонентов общего применения можно найти либо в обоих исполнениях, либо в исполнении для поверхностного монтажа, поскольку он считается более прогрессивным. Исключение составляют силовые компоненты, электромеханические реле, разъемы, большие переменные резисторы, панели ИМС и некоторые другие компоненты, однако многие из них уже имеют аналоги для монтажа на поверхность. Существует неоднозначное отношение к надежности электролитических конденсаторов для поверхностного монтажа, а их танталовые аналоги достаточно дороги, поэтому часто на платах среди поверхностного монтажа можно встретить штыревые алюминиевые электролитические конденсаторы. Все это обуславливает необходимость применения технологии смешанного монтажа (одновременного наличия на ПП SMT- и THT-компонентов).
Технология установки THT-компонентов относительно проста, хорошо отработана, допускает ручные и автоматизированные методы сборки, хорошо обеспечена сборочным оборудованием и технологическим оснащением. В данной статье кратко рассмотрены основные операции THT-технологии.
Компоненты
ЭК, используемые в технологии монтажа в отверстия, по типу корпуса можно разбить на следующие основные группы (примеры корпусов приведены на рис. 1):
а) ЭК с осевыми (часто встречается обозначение axial, аксиальными) выводами;
б) ЭК с радиальными выводами (radial);
в) SIL, SIP (Single In-Line Package) – многовыводной корпус с однорядным расположением выводов;
г) DIP (Dual In-Line Package) – корпус с двухрядным расположением выводов;
д) разъемы, слоты;&
е) панели для ИС, в том числе DIP; ZIF (Zero Insertion Force, панели с нулевым усилием вставки для штырьковых ИС); PGA (Pin Grid Array, панели для штырьковых ИС с матрицей выводов);
ж) различные компоненты сложной формы.
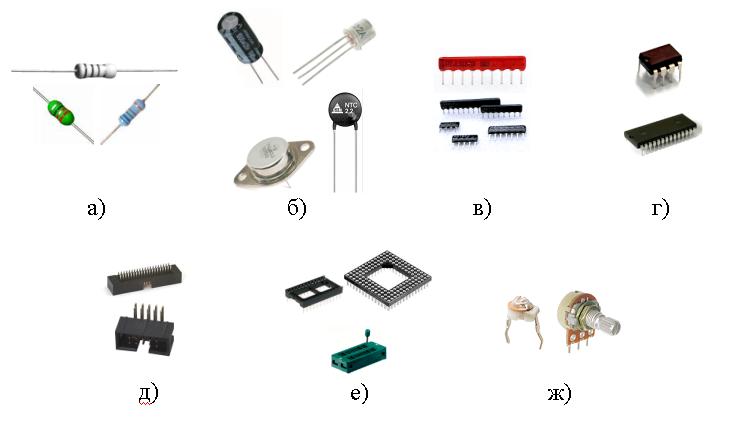
Рис. 1. Примеры THT-компонентов: а) с осевыми выводами; б) с радиальными выводами; в) в корпусах SIL; г) в корпусах DIP; д) разъемы; е) панели для ИС; ж) ЭК сложной формы
Такое разделение компонентов прежде всего связано с особенностями технологии их монтажа. Так например, осевые и радиальные выводы компонентов требуют формовки и обрезки, тогда как большинство других компонентов в этом не нуждаются. При формовке выводов, и как следствие, последующей установке компонентов с осевыми выводами они имеют дополнительную степень свободы (вращение вокруг оси), поэтому их маркируют цветными кольцами (см. рис. 1а), исключающими установку «маркировкой вниз».
Также есть различия в механизмах захвата, базирования и фиксации разных групп компонентов, поэтому часто компоненты в разных корпусах устанавливаются каждый на своем оборудовании.
Типичная последовательность операций
Технологический процесс сборки ПП на основе THT-технологии состоит из следующих типовых этапов:
- подготовка выводов ЭК (формовка, обрезка), часто совмещается с автоматизированным монтажом;
- установка компонентов (ручная, автоматическая);
- пайка (волной припоя, ручная, селективная);
- отмывка (ультразвуковая, струйная).
На некоторых предприятиях сохранилась технология, при которой из-за проблем с покрытиями выводов и хранением компонентов подготовка выводов включала в себя предварительное лужение, однако современная технология этого не предусматривает благодаря качественной упаковке и покрытию выводов современных компонентов.
Ниже рассмотрены данные операции в порядке выполнения.
Подготовка выводов ЭК
Выводы ЭК перед монтажом должны быть специальным образом подготовлены. Цель подготовки:
- выравнивание (рихтовка) выводов (если требуется);
- обеспечение необходимого монтажного расстояния между выводами;
- зазора между ПП и компонентом (если требуется);
- фиксации ЭК на ПП при ручном монтаже либо до поступления платы в установку пайки.
Зазор обычно обеспечивается приданием выводам ЭК соответствующего изгиба – т.н. «опорного зи́га» (рис. 2а); самофиксация ЭК на ПП перед групповой пайкой – особым изгибом части вывода, входящей в отверстие ПП – замка́ (рис. 2б). Одновременное выполнение зига и замка носит название «зиг-замо́к».
Также возможно крепление ЭК следующими методами:
- обеспечением пружинения выводов;
- посадкой на клей (клей полимеризуется при комнатной температуре, при этом для стеклянных корпусов может понадобиться надевание трубки на часть корпуса, контактирующую с адгезивом; также необходимо обеспечить достаточное количество клеевых точек для крепления тяжелых ЭК);
- подпайкой выводов (применяется при ручном монтаже – например, подпайка двух диагонально расположенных выводов разъема);
- подгибкой (полной либо частичной – на угол от 0 до 45° от плоскости ПП и только для выводов диаметром менее 0,7 мм (более – в технически обоснованных случаях); необходимо обеспечить минимально допустимое расстояние от загнутого вывода до соседних КП/выводов/проводников; следует осуществлять подгибку вдоль печатного проводника, если в конструкторской документации нет других указаний);
- с использованием различных держателей (хомутов, металлических скоб, клипс, зажимов).
Тяжелые элементы (например, трансформаторы) или элементы, подверженные механическим воздействиям (тумблеры, потенциометры, подстроечные конденсаторы), устанавливаются с помощью особых держателей. Такие держатели обеспечивают надежное механическое крепление соответствующих элементов к ПП и предотвращают обрыв и поломку выводов под воздействием механических нагрузок.
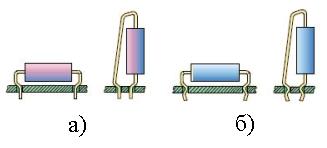
Рис. 2. Обеспечение с помощью формовки выводов ЭК: а) зазора между ПП и компонентом (опорный зиг); (б) самофиксации ЭК на ПП (замо́к). Источник: ASPgold
Формовку круглых или ленточных выводов элементов производят с помощью ручного монтажного инструмента либо специальных полуавтоматических устройств таким образом, чтобы исключались механические нагрузки на места крепления выводов к корпусу. При формовке выводов не допускается их механическое повреждение, нарушение защитного покрытия, изгиб в местах соединения вывода и корпуса, скручивание относительно оси корпусов, растрескивание стеклянных изоляторов и пластмассовых корпусов.
Основные ограничения (рис. 3) накладываются на размер от корпуса ЭК до оси изогнутого вывода (L) и внутренний радиус изгиба выводов (R). Минимальный размер L в зависимости от типа ЭК находится в пределах 0,75 – 4 мм (но не менее 2·D выводов); размер R зависит от диаметра вывода и составляет минимум 0,5 – 1,5 мм (но не менее (1–2)·D выводов). Также на выводах не должно быть деформаций и утонений, превышающих 10% от диаметра, ширины либо толщины вывода.
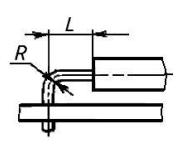
Рис. 3. Основные параметры формовки
Несоблюдение данных рекомендаций может привести к образованию избыточных напряжений в месте крепления вывода к корпусу ЭК и в области изгиба вывода и, как следствие, появлению в этих местах трещин и, возможно, обрывов, в особенности при механических воздействиях на собранный узел. Не допускается изгибать жесткие выводы (лепестки) транзисторов и диодов средней и большой мощности, так как это может привести к растрескиванию их стеклянных изоляторов и нарушению герметичности корпусов.
Расстояние от корпуса до места пайки должно быть не менее 2,5 мм, если не приняты меры к дополнительному теплоотводу в процессе пайки.
Не осуществляют формовку, подгибку и обрезку при установке многовыводных ЭК (ИС в DIP-корпусе и пр.). Для них может проводиться исключительно рихтовка (выравнивание) выводов, если в этом есть необходимость.
Устройства формовки выпускаются с механическим и электрическим приводом подачи ЭК, а также механическим либо пневматическим – самого устройства формовки. Загрузка компонентов производится из лент, трубчатых кассет, россыпи. Геометрические параметры формовки регулируются; установки оснащаются сменными формовочными матрицами. Специальная конструкция матриц формовочных устройств обеспечивают отсутствие избыточных напряжений и зазубрин на материале в месте изгиба вывода. Примеры отформованных выводов различных THT-компонентов приведены на рис. 4.
.jpg)
Рис. 4. Примеры формовки выводов ЭК с осевыми (а) и радиальными (б) выводами. Источник: ASPgold
Производительность формовочного оборудования в автоматическом режиме при загрузке из лент, как правило, составляет до 40000 ЭК/час для ЭК с осевыми выводами и 20000 ЭК/час – с радиальными; при загрузке ЭК из россыпи – 7000 и 3000 ЭК/час соответственно. При ручной подаче ЭК типовая производительность – около 1500–3000 ЭК/час.
Существуют автоматические счетчики выводных компонентов, вклеенных в ленту (до 100 ЭК/с).
Установка компонентов
Установка ТНТ-компонентов осуществляется с применением специальных монтажных автоматов, автоматизированных рабочих мест (АРМ) либо полностью вручную.
Автоматизированный монтаж
Сборочное оборудование
Существует два основных вида автоматизированного оборудования по критерию выполняемых функций:
- собственно монтажные автоматы (inserter, от insert – вставлять), осуществляющие вставку штырьковых выводов ЭК в отверстия на ПП, их подрезку и подгибку (опционально) с обратной стороны ПП с помощью монтажных, гибочных и отрезных головок соответственно; делятся на группы по типу компонентов (Axial (Radial) inserter – автомат для монтажа ЭК с осевыми (радиальными) выводами, DIP inserter – автомат для монтажа ЭК в корпусах DIP, Odd-Form inserter – автомат для монтажа ЭК в корпусах сложной формы);
- секвенсеры (sequencer) – автоматы формирования последовательности устанавливаемых ЭК (т.е. подготовки программной ленты, содержащей последовательно вклеенные ЭК разных типоразмеров в порядке их последующего монтажа; осуществляется путем переклейки ЭРЭ из первичных лент по программе).
Многие монтажные автоматы одновременно обладают функцией секвенсеров, т.е. могут работать непосредственно из первичных лент без необходимости подготовки программной ленты.
Следует отметить, что на современном рынке, наряду с выпускавшимся в 90-е г.г. и продающимся сейчас б/у (в т.ч. восстановленным) оборудованием для выводного монтажа (различные модели автоматов Dynapert, Panasert, Amistar, Universal Instruments и пр.), присутствуют современные модели различных производителей, уделяющих существенное внимание развитию технологии автоматизированного монтажа в отверстия. Многие опции автоматов, ранее доступные лишь для SMT-монтажа, стали неотъемлемой частью современного сборочного оборудования для THT-технологии. Следящие приводы перемещений по координатным осям, управление с помощью ПК, загрузка питателей без остановки работы, контроль правильности подачи ЭК, одновременная сборка более чем одной ПП, автоматическая загрузка/выгрузка ПП, коррекция погрешностей проводящего рисунка ПП, автоматическая смена захватных устройств – все это доступно в настоящее время и для штырькового монтажа. Применяются системы технического зрения для оптической коррекции положения ЭК и считывания реперных знаков. Сборочные головки автоматов оснащены преимущественно механическими захватами с сервоприводом. Стандартные углы поворота ЭК кратны 90°, однако, как правило, существует возможность оснащения автомата сборочной головкой со свободным углом поворота.
Ряд автоматов обладает способностью устанавливать на ПП проволочные перемычки (jumpers), нарезая их непосредственно перед монтажом из непрерывного прутка.
Паспортная производительность современного монтажного оборудования достигает 20000–40000 ЭК/час при уровне ошибок монтажа 100–200 ppm (для простых ЭК). Производительность при монтаже ЭК сложной формы может быть меньше на порядок. Основными параметрами оборудования, помимо перечисленных выше, являются геометрические характеристики ЭК и ПП, которые подлежат установке:
- диапазон либо дискретный набор расстояний между выводами (рядами выводов);
- максимальный диаметр и высота ЭК (в зависимости от его типа – с осевыми либо радиальными выводами);
- диапазон диаметров выводов;
- диапазон габаритных размеров ПП.
Загрузочные устройства
Для оснащения автоматов монтажа THT-компонентов используются загрузочные устройства (питатели) следующих основных типов (рис. 5):
- ленточные для ЭК с радиальными и осевыми выводами – предназначены для пошаговой подачи ЭРЭ, вклеенных в ленту; лента может быть намотана на бобину (Tape and Reel) или упакована в «магазин»-коробку (Ammo Pack);
- из трубчатых кассет для ИС в DIP-корпусе, компонентов сложной формы – с наклонным транспортным лотком и горизонтальные (для ЭК, которые не скользят свободно по наклонному лотку вследствие своих конструктивных особенностей – массы, формы корпуса либо выступающих острых выводов);
- вибробункерные для подачи различных ЭК из россыпи с возможностью их одновременной ориентации перед захватом;
- матричные (сотовые) для ЭК сложной формы – из матричных поддонов, магазинов.
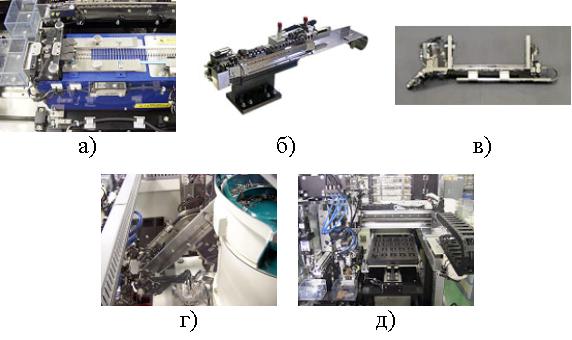
Рис. 5. Примеры питателей для THT-компонентов: а) с осевыми выводами; б) с радиальными выводами; в) из трубчатых кассет; г) вибробункерный; д) из матричных поддонов. Источник: A-I-TEC.Co.,Ltd
Ряд моделей оборудования оснащается питателями с микропроцессорным управлением, а также устройствами их автоматической смены.
|
 |
|