18 октября 2007
Нанесение материалов дозированием. Часть II
Размещение дозатора
Свойства пасты существенно деградируют при встряхивании, резких ударах и воздействии вибрации на шприц. Особенно опасна вибрация, вследствие чего оборудование, вызывающее ее (например, вибробункерные питатели), должно быть удалено от дозирующих систем; в противном случае произойдет быстрое расслоение пасты. Если убрать такое оборудование или изолировать дозатор от его воздействия не представляется возможным, следует использовать шприцы меньшего объема, не дающие пасте существенно расслоиться за время своего опустошения. Большое влияние на расслоение пасты может оказать быстрое ускорение, вибрации и ударные нагрузки, вызываемые работой автоматизированного дозирующего оборудования. В этом случае также необходим подбор оптимального размера шприца.
Объем шприца
Объем шприца выбирается, исходя из соображений частоты замены, температурных воздействий и размера наносимой дозы.
Например, в приложениях, где паста расходуется со скоростью 10 г/ч, шприцы объемом 3 см³ не будут хорошим выбором, так как потребуется их замена через ~1 час работы. В этом случае, для минимизации времени простоя оборудования для замены шприца, следует использовать объем 30 см³. Если же 10 г пасты расходуются в течение двух дней, использование шприцев объемом 3 см³ минимизируют потери материала, связанных с деградацией его свойств с течением времени. Это соображение очень важно, если паста подвергается нагреву в процессе дозирования, что обычно происходит из-за сжатия воздуха в пневматической системе и трения в материале, а также при повышенной температуре воздуха на производстве, за счет тепла рук монтажника при ручном нанесении и по другим причинам.
Размер наносимой дозы определяет количество циклов дозирования, после которого шприц опустошается. При более мелких дозах, это количество растет, и паста более длительное время подвергается деградирующим механическим воздействиям. Тем не менее, большинство паст позволяет выполнить, по крайней мере, 10000 циклов дозирования без ухудшения свойств пасты вследствие механического воздействия на нее [17].
Достоинства
- Концептуальная простота метода.
- Гибкость, возможность применения для широкого круга материалов (включая эпоксидные компаунды, адгезивы и пр.)
- Шприцы имеют низкую стоимость и демонстрируют хорошую экономическую эффективность, так как могут быть утилизированы после использования (целиком либо только наконечник).
Недостатки
- Низкая объемная точность и повторяемость наносимых объемов. Материал удерживается от истечения из наконечника вследствие приложения обратного давления (с помощью вакуума), что негативно сказывается на точности наносимых доз.
- Зависимость размера дозы от уровня материала в шприце. По мере опустошения шприца, сдвиговое напряжение, удерживающее материал от истечения, уменьшается. Также увеличивается объем воздуха в шприце, что требует большего времени для его сжатия – время отклика системы на приложение давления увеличивается. Совместно эти факторы вызывают значительные изменения в динамике истечения материала из наконечника после приложения и последующего сброса давления, что ведет к неравномерности нанесения отпечатков с течением времени (рис. 4). Вследствие этого, наносимый объем малых доз материалов для последующего монтажа ЭК типоразмеров 0805, 0603 непостоянен, а получение стабильных результатов для типоразмера 0402 крайне сложно и в общем случае не рекомендуется к промышленному использованию [23].
- Применение пневматических дозаторов демонстрирует высокую степень зависимости от изменения температуры – как окружающей среды, так происходящего вследствие образования внутренней теплоты в результате трения как побочного эффекта процесса дозирования. Изменение температуры меняет вязкость наносимого материала в шприце (с ее ростом вязкость падает). График такой зависимости для адгезивов, применяемых в технологии поверхностного монтажа, продемонстрирован на рис. 5. Даже небольшое изменение вязкости значительно влияет на величину давления, необходимого для проталкивания требуемого объема материала через шприц. Это существенно влияет на точность наносимых объемов доз во времени, даже если время процесса дозирования и давление жестко контролируются.
К указанному выше следует добавить, что при температурах более 27°С паяльная паста может потерять способность содержать припой во взвешенном состоянии, что приведет к расслоению составляющих пасты. Также необходимо помнить о том, что скорость химических реакций с участием флюса при температурах, превышающих 27°С, заметно растет.
- В случае ручного применения – действие человеческого фактора: степень тренировки и накапливающаяся усталость оператора.
- Метод обладает меньшей производительностью по сравнению с другими технологиями нанесения материалов дозированием.
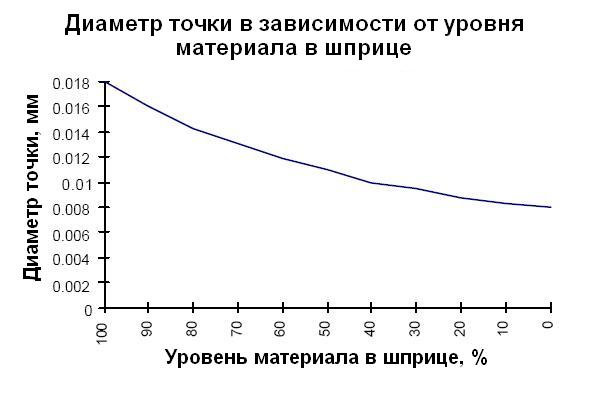
Рис. 4. Зависимость размера наносимой точки от уровня материала в шприце (для SMT-адгезивов). Рисунок из [19].
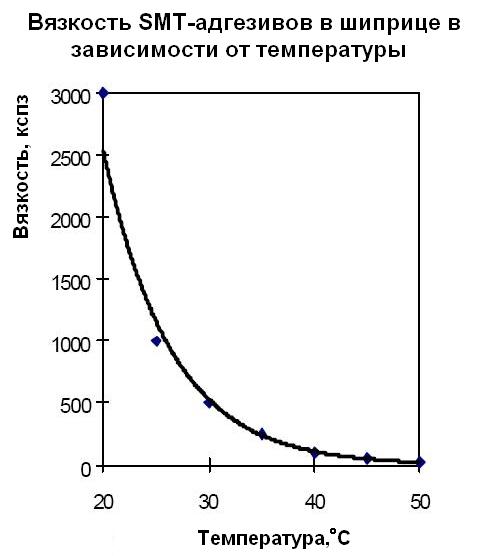
Рис. 5. Зависимость вязкости материала в шприце от температуры (для SMT-адгезивов). Рисунок из [19].
В наибольшей степени на характер и качество дозирования влияют такие параметры, как время, давление, реология материала и уровень материала в шприце. Первые два параметра достаточно хорошо управляемы, основные проблемы возникают с контролем реологических свойств (прежде всего, вязкости) и уровня материала в шприце. Для автоматов дозирования эти параметры оцениваются системой технического зрения (СТЗ) в реальном времени по диаметру наносимой точки. При изменении диаметра система корректирует параметры времени/давления либо дает сигнал оператору. Тем не менее, такая коррекция не затрагивает истинных причин возникновения неравномерности наносимых отпечатков, вследствие чего простота использования систем пневматического дозирования оборачивается снижением точности/повторяемости отпечатков с ростом скорости нанесения.
Вследствие вышесказанного, сферой применения данного метода являются некритичные к точности и повторяемости нанесения материала процессы в лабораторных условиях, единичном и мелкосерийном многономенклатурном производстве. Метод может быть рекомендован в случае нанесения материалов с малым временем жизни (долговечностью), так как более совершенный и дорогостоящий дозатор не будет при этом испорчен в случае несвоевременной очистки его от остатков материала [9].
Шнековые дозаторы
С повышением плотности компоновки электронных модулей, внедрением компонентов с малым шагом выводов и, как следствие, возрастанием требований к точности, повторяемости и скорости нанесения доз, электронная промышленность потребовала разработки более совершенных устройств дозирования. Этим требованиям отвечают шнековые дозаторы (Auger pump), занимающие в течение десятилетия одно из лидирующих положений в технологии нанесения материалов дозированием. Данная технология берет свое начало из Древнего Египта, где таким образом откачивалась вода из Нила.
Подача материала осуществляется при приложении постоянного давления к резервуару с дозируемым материалом, благодаря которому он перемещается по подающему патрубку. Материал входит в контакт с прецизионным винтом (шнеком), который вращается в течение заданного времени с определенной постоянной скоростью. В процессе поворота винта, материалу сообщается сдвигающее усилие, он захватывается канавками винта и перемещается вниз, к дозирующему наконечнику. Как только материал достигнет пространства между винтом и наконечником, он начинает испытывать сопротивление вследствие ограниченного объема. Винт продолжает вращаться, создавая усилие, достаточное для проталкивания пасты через наконечник (рис. 6). Количество нанесенного материала определяется углом поворота винта, вязкостью материала и температурой окружающей среды. Постоянное сопротивление истечению материала, которое обеспечивает сам винт и наконечник, препятствует постоянному выходу материала из дозатора. Сопротивление рождает противоток материала обратно в шприц, величина которого пропорциональна перепаду давления между шприцем и областью перед наконечником. Таким образом, поток материала из наконечника будет равен сдвиговому потоку минус обратный поток. Если наконечник требует большего давления, чем может обеспечить винт, обратное давление превысит сдвиговое и поток не потечет из наконечника.
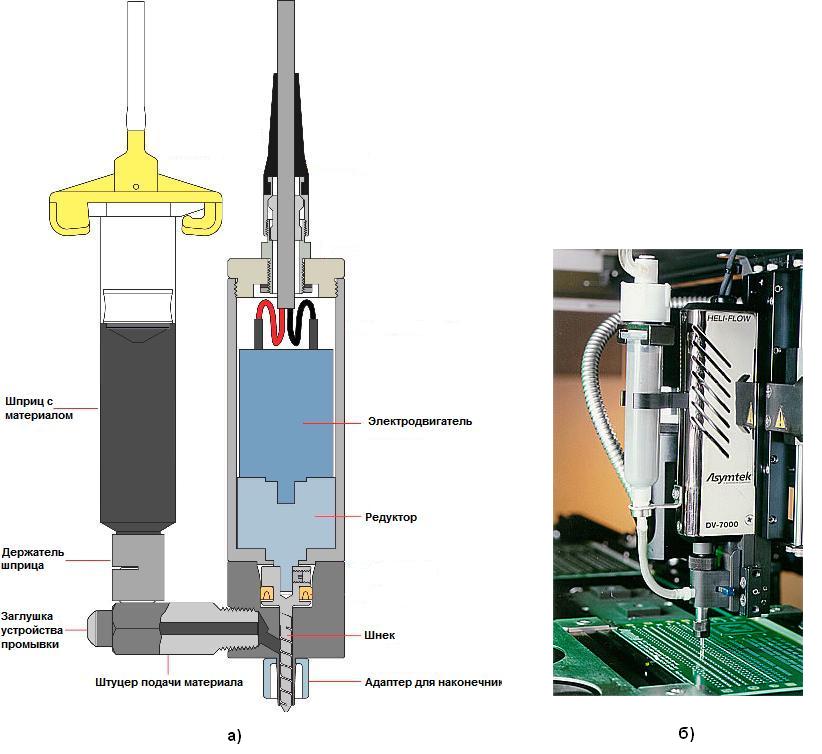
Рис. 6. Шнековые дозаторы: а) конструкция; б) автоматическая дозирующая головка. Рисунок и фото из [18, 37].
Некоторые шнековые дозаторы на конце оснащаются шаровым клапаном, который располагается вплотную к седлу и обеспечивает точную отсечку дозируемого материала. Это особенно актуально для таких текучих материалов, которые продолжают течь либо капать из наконечника даже после остановки вращения винта.
Долгое время шнековые дозаторы составляли основу инструментария для дозирования. Они существенно эволюционировали, появились модели с различным видом резьбы, различным шагом, глубиной и количеством заходов резьбы и диаметров винта для применения в различных процессах.
Следующие параметры процесса оказывают влияние на качество нанесения материала с помощью шнекового дозатора [18]:
- Размер дозы
- Тип наконечника
- Давление воздуха
- Скорость вращения шнека
- Выбор конструкции шнека
- Температура
- Размещение дозатора
- Зазор между наконечником и ПП
- Объем шприца
- Уровень материала в шприце
- Выбор двигателя для вращения шнека
- Техническое обслуживание
Часть из перечисленных параметров описаны выше в разделе «Пневматические дозаторы».
Давление воздуха
Давление должно быть достаточным для заполнения канавок шнека и постоянным для создания равномерного потока материала от резервуара к винту. Различные производители приводят разные типовые значения – например, от 4 до 10 psi (0,27 – 0,67 атм.) [18], либо 10-20 psi (0,67 – 1,33 атм.) [20], однако указывается, что выбор конкретного давления существенно зависит от приложения.
Если давление будет слишком мало, возможно возникновение дефектов процесса дозирования: кавитации, неполного нанесения и пропуска доз. Диагностика этих дефектов бывает затруднена: их проявления можно ошибочно принять за последствия наличия пузырьков воздуха в шприце либо неправильного подбора зазора между наконечником и ПП.
Капание. При отсутствии давления и поворота винта материалы с низкой вязкостью могут продолжать капать с наконечника под действием гравитации. В некоторых случаях, когда нанесение доз происходит через неравные промежутки времени, капание вызывает заметные изменения объема наносимого материала. Также оно может быть вызвано избыточно высоким давлением.
Образование полостей (кавитация). Возникает в случае, когда подача материала недостаточна по сравнению со скоростью вращения винта. Возникают пропуски в подаче материала по винту, вызывающие прерывистый поток материала из наконечника. Для решения этой проблемы можно повысить давление, но это может привести к капанию. Наиболее безопасно от кавитации можно избавиться, уменьшив скорость вращения винта [20].
Если давление будет слишком велико, материал будет проталкиваться вниз по шнеку, когда он не вращается, и капать из наконечника. Это приведет к неполному нанесению материала, так как он будет скапливаться вокруг наконечника и заполнять зазор между ним и механическим штырем, обеспечивающим зазор между ПП и наконечником.
Даже при правильной настройке давления может происходить истечение при больших паузах между нанесением пасты. В этом случае рекомендуется программное снятие давления с резервуара с пастой. Может быть использован импульсный режим давления – преимущественно в случае, когда недостаточна скорость нанесения, хотя шнековые дозаторы изначально не предназначены для работы в импульсном режиме. Следует помнить, что увеличение давления ведет к расслоению пасты и капанию. Если такое решение требуется, то, как правило, это является показателем того, что шнековый дозатор – неоптимальный выбор для данных условий процесса.
Скорость вращения винта
Давление определяется скоростью вращения шнека (в об/мин). Чем больше оборотов в единицу времени делает шнек, тем больше материала наносится за этот временной промежуток. Для каждой комбинации шнека, пасты и наконечника существуют максимально и минимально достижимые скорости истечения материала при максимальном рекомендуемом давлении. Т.е. после определенного значения, бо́льшая скорость шнека не даст прироста скорости нанесения пасты. Когда давление, требуемое для преодоления внутреннего сопротивления наконечника, достигает предельного уровня, происходят следующие процессы: частицы паяльной пасты подвергаются холодной сварке друг с другом, шнек блокируется, и температура пасты растет вследствие комбинированного действия давления и трения. В этом случае либо двигатель будет не в состоянии провернуть шнек, либо давление, создаваемое вращающимся шнеком, упадет ниже порогового значения, необходимого для преодоления внутреннего сопротивления наконечника, и паста течь не будет.
Наиболее точный контроль процесса достигается при комбинации малой скорости вращения шнека и длительного времени цикла. Для максимизации скорости нанесения, необходимо вращать шнек на максимально возможной скорости, не допуская деградации свойств пасты.
Скорость должна соответствовать приложенному давлению, в противном случае также возможно возникновение кавитации и капания. Типовое значение скорости составляет 200 – 800 об/мин в зависимости от размеров доз [20]. Меньшее значение соответствует более точному дозированию на КП для установки миниатюрных компонентов.
Выбор конструкции шнека
Существуют два основных типа шнеков: 8 и 16 витков резьбы на дюйм при различной глубине витков (рис. 7). Стандартный размер составляет 8 витков, сопротивление истечению при этом среднее и паста движется быстро. Подходит для большинства применений. Шнек с 16 витками применяют, когда требуется либо дополнительное внутреннее сопротивление, либо нанесение более мелких доз. Расстояние между витками у таких шнеков в два раза меньше, при этом расстояние, которое должна пройти паста вокруг винта, удваивается, а количество наносимого материала на один оборот винта уменьшается в два раза. Лучше определиться с конструкцией шнека на ранних стадиях подготовки производства – это поможет сохранить время и усилия. Шнеки с более мелким шагом лучше удерживают материал, когда шнек не вращается, и могут создавать бо́льшие давления в наконечнике, чем шнеки с более мелким шагом канавок.
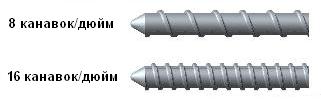
Рис. 7. Шнеки с различным шагом витков. Рисунок из [18].
Чем глубже канавки шнека, тем больше скорость истечения пасты (меньше сопротивление истечению), но больше капание. Кроме того, такие шнеки могут создать большое давление в наконечнике благодаря тенденции к обратному течению материала к центру винта.
Зазор между наконечником и ПП
В процессе дозирования наконечник должен быть точно установлен над областью ПП для нанесения пасты. Цель такого размещения – обеспечить легкое истечение пасты и чистое отделение наконечника при его переносе в следующую позицию дозирования.
В данной статье рассматривается расположение наконечника перпендикулярно поверхности ПП. Наклонное расположение наконечника часто помогает решить ряд проблем, связанных с дозированием, но рассмотрение данного аспекта выходит за рамки базовых рекомендаций.
Если наконечник установлен слишком близко к поверхности платы, возможно образование тяжей (нитей материала, тянущихся за наконечником и падающих затем на поверхность ПП), а также перенос дозы на следующую позицию. Слишком высокое расположение наконечника вызовет растекание дозы и также возможно образование тяжей (рис. 8). Образования тяжей можно избежать, осуществив нагрев наконечника либо области, близкой к области дозирования – материал в этом случае лучше отделяется от наконечника.
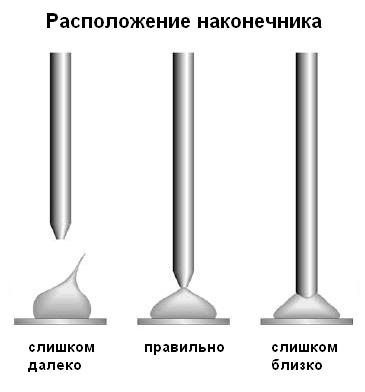
Рис. 8. Расположение наконечника над поверхностью ПП. Рисунок из [15].
Возможны следующие дополнительные проблемы, связанные с неправильным выбором значения зазора. Если наконечник находится близко к поверхности, паста, выйдя из наконечника, ударится о поверхность платы, и возникшее обратное давление не даст пасте вытекать дальше (рис. 9а). Продолжительная работа шнека без истечения пасты вызывает расслоение пасты и холодную сварку частиц в дозаторе. Если он располагается далеко от ПП – паста будет иметь лучшую адгезию к себе самой и наконечнику, чем к поверхности платы, прилипнет к наконечнику и не останется на плате при переходе к следующей дозе (рис. 9в). Получается картина «большая точка – маленькая точка»: паста будет налипать на наконечник, при нанесении следующей дозы она перейдет на ПП, будет снова захвачена на следующем шаге дозирования и т.д.
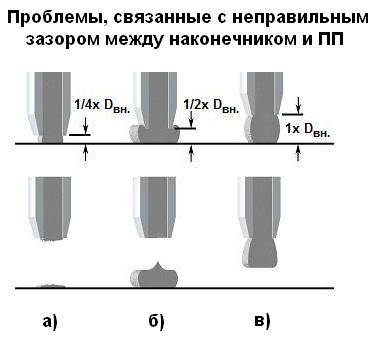
Рис. 9. Проблемы, связанные с неправильным зазором между наконечником и поверхностью ПП: а) слишком малый зазор; б) правильное расположение; в) слишком большой зазор. Рисунок из [18].
Стандартное значение зазора, рекомендуемое большинством производителей, составляет ½ от внутреннего диаметра наконечника [15, 18, 20], либо 60% от него [12], и составляет обычно 0,15 – 0,3 мм.
Существуют различные способы выдерживания зазора. Самый простой из них – использование опорного штыря (рис. 10). Он контактирует с поверхностью платы и выдерживает необходимый зазор независимо от ее возможного прогиба и других геометрических погрешностей. Тем не менее, такой подход не обеспечивает необходимой гибкости в настройке зазора, а также часто возникает проблема контактирования штыря с компонентами на ПП либо уже нанесенными дозами. Более совершенные системы используют другие методы контроля высоты – контактные (механические датчики силы с контактным усилием всего лишь ~1 г) и бесконтактные (лазерные датчики). Такое оснащение дозатора позволяет иметь одну дозирующую головку на весь диапазон размеров доз и зазоров [12].

Рис. 10. Опорный штырь для выдерживания зазора между наконечником и ПП. Рисунки из [15,12].
|