Скоро!
Событий нет.
|
 |
24 июня 2007
Основы технологии монтажа в отверстия. Часть II
Ручная и полуавтоматическая установка компонентов
Данная операция выполняется на АРМах либо монтажных столах. В этих устройствах автоматизирована подача сборочной информации – места установки ЭК на ПП и его требуемой ориентации, а также может быть обеспечена автоматическая подача нужного лотка с компонентами устанавливаемого типономинала, механизирован процесс фиксации ПП на монтажном столе. АРМы могут быть дополнительно оснащены устройствами формовки выводов ЭК. Такое оборудование дешево, но малопроизводительно (1000–2000 ЭК/ч).
Существуют следующие варианты установки ЭК:
- С зазором (вариант II по ОСТ4 010.030-81). При таком способе установки легче осуществить отмывку собранных узлов от остатков флюса, меньше перегрев ИС при пайке. Печатные проводники могут располагаться в этом случае под навесным элементом. При определенных условиях (при определенных спектрах воздействия) улучшается стойкость к вибро- и ударным воздействиям, передающимся по плате, поскольку воздействие демпфируется выводами. Тем не менее, увеличивается высота узла, меньше его устойчивость к прямым механическим воздействиям. Возможен отрыв КП от односторонней ПП при приложении значительного давления к ЭК сверху.
- Без зазора (вариант I по ОСТ4 010.030-81). Элементы лучше сопротивляются механическим нагрузкам (в особенности – с дополнительным креплением за корпус скобой и т.д.), высота узла получается меньшей. Улучшается теплоотдача от компонента печатной плате, что часто применяется, когда использование радиатора нецелесообразно. Компоненты с радиальными выводами, уложенные на бок, рекомендуется устанавливать исключительно без зазора (в отдельных случаях – с технологическими прокладками под корпусом). Уменьшается длина выводов ЭК, что улучшает электрические характеристики устройства. Однако может быть затруднена отмывка собранного узла, а также необходимо обеспечить взаимную изоляцию ЭК и печатных проводников, металлизированных отверстий, проходящих под корпусом (например, с помощью изолирующих прокладок с приклейкой их к корпусу ЭК и/или ПП).
Вертикальная установка ЭК (вариант III по ОСТ4 010.030-81) с осевыми выводами увеличивает плотность компоновки, однако снижает технологичность, повышает вероятность взаимного замыкания выводов, увеличивает высоту узла и делает внешний вид неопрятным. При этом необходимо, чтобы угол наклона ЭК относительно вертикальной оси не превышал 15°.
Типы установки компонентов регламентируется отраслевыми стандартами, например ОСТ4 010.030-81, и стандартами предприятия. Хотя требования отраслевых стандартов не являются в настоящее время обязательными, их часто применяют в качестве рекомендации и исходных документов.
Устанавливать ЭК следует таким образом, чтобы были различимы элементы их маркировки, в особенности касающиеся полярности, для обеспечения последующего контроля правильности монтажа.
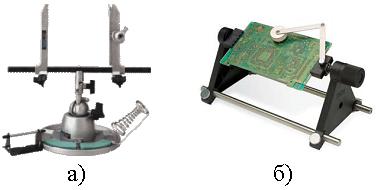
Рис. 6. Примеры держателей ПП. Источник: PanaVise Products, Inc. (а) и Cooper Industries, LLC. (б)
Монтаж компонентов можно проводить, устанавливая по одному ЭК и далее осуществляя пайку путем поворота ПП, однако более технологичным является способ, когда ПП в процессе монтажа имеет жесткую фиксацию. Для закрепления печатных плат и их поворота в процессе монтажа применяют специальные приспособления. Существуют держатели ПП (рис. 6), снабженные подпружиненным фиксатором платы, обеспечивающие возможность ее закрепления в горизонтальной, вертикальной, а также повернутой вокруг одной или двух осей плоскости, антистатическую защиту при монтаже и пайке. Процесс ручной пайки ЭК рассмотрен ниже.
Пайка
В рамках THT-технологии преимущественно применяются три метода пайки: пайка волной, селективная и ручная.
Пайка волной припоя
Пайка волной – наиболее распространенный метод пайки, впервые появившийся в 50-е годы XX века. Он применяется как для изделий на основе исключительно штырьковых компонентов, так в случае смешанного монтажа, когда на ПП одновременно наличествуют THT- и SMD-компоненты.
В процессе пайки ПП устанавливаются на конвейер и последовательно проходят несколько рабочих зон паяльной установки: зону флюсования, предварительного нагрева, пайки.
Особое влияние на процесс пайки оказывают следующие параметры:
- угол наклона конвейера;
- скорость движения конвейера;
- тип применяемого флюса и его плотность;
- толщина слоя флюса и равномерность его нанесения;
- температура и скорость предварительного нагрева;
- тип применяемого припоя и степень его чистоты (отсутствие примесей);
- температура припоя;
- форма, высота и стабильность волны припоя;
- атмосфера при пайке и степень ее чистоты.
Флюс удаляет оксидные пленки с паяемых поверхностей, улучшает смачивающую способность припоя и предотвращает окисление до начала пайки. Применяются флюсы на водной и канифольной основе, в том числе не требующие отмывки, а также водосмываемые флюсы. Флюсование осуществляется одним из двух основных способов: распылением и с помощью пенообразователя. Многие установки пайки волной имеют возможность оснащения флюсователями обоих типов.
Распыление флюса осуществляется, например, при помощи вращающегося сетчатого барабана, где поток сжатого воздуха, пропущенный через его сетку, создает мелкодисперсную струю жидкого флюса. Существуют конструкции флюсователей, где флюс предварительно переходит в мелкодисперсное состояние на рабочей поверхности ультразвуковой форсунки, а затем распыляется потоком сжатого воздуха. Слой наносимого флюса должен быть равномерным и иметь толщину 1–10 мкм в сухом состоянии. Производится подбор оптимального давления при распылении, а также контроль плотности флюса. Метод распыления обладает рядом преимуществ по сравнению с пенообразованием, в частности, он более экономичен, а также позволят точнее контролировать толщину флюса.
Пенное флюсование осуществляется с помощью фильтрующих элементов (трубчатых фильтров либо пористых камней (например, пемзы) с размером пор ≈ 3 – 35 мкм), которые образуют однородную пену, состоящую из пузырьков малого диаметра. Пена направляется на плату с помощью сопла. Пузырьки, лопаясь, разбрызгивают флюс по нижней поверхности ПП. Чем меньше размер пузырьков пены, тем лучшее смачивание обеспечивает флюсование, поэтому применение трубчатых фильтров по сравнению с пористыми камнями предпочтительно. Высота подъема пены регулируется (обычно не более 2 см).
Зона флюсования оканчивается устройством «воздушного ножа», служащим для удаления избытка флюса с поверхности ПП.
Предварительный нагрев служит для предотвращения теплового удара ПП и ЭК в результате контакта с волной горячего припоя, сушки (удаления растворителя) и активации флюса. Нагрев осуществляется ИК-модулями с различной длиной волны, кварцевыми нагревателями и конвекционными системами (последние особенно эффективны в случае наличия на ПП ЭК, обладающих большой теплоемкостью).
Далее конвейер с ПП проходит непосредственно зону пайки, где в ванне с помощью помпы формируется волна расплавленного припоя. Платы устанавливаются либо на пальчики (лепестки) конвейера, как правило, выполненные из титана, либо крепятся в паллетах. Конвейер обладает возможностью регулировки скорости движения (0–2 м/мин) и угла наклона ПП по отношению к волне (5–9°), что важно для обеспечения стекания избыточного количества припоя. Форма волны припоя может быть различной, в зависимости от применяемой модели оборудования. Изначально использовалась симметричная волна, но впоследствии произошел переход к несимметричным (T-образная, Z-образная, W-волна и пр.), обеспечивающим лучшие результаты с точки зрения качества паяных соединений (рис. 7а). Производители ЭК в своих рекомендациях указывают параметры профиля пайки волной, которые включают в себя температуру и скорость предварительного нагрева, скорость подъема температуры при воздействии волны, максимальную температуру, которой подвергается ЭК во время пайки и время выдержки при ней, а также максимально допустимую скорость охлаждения ПП.
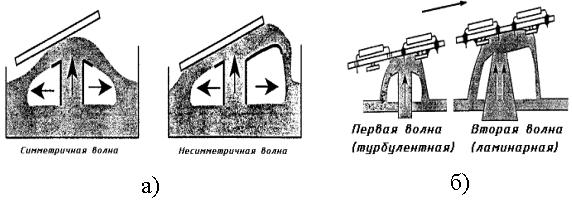
Рис. 7. Волна припоя: а) симметричной и несимметричной формы; б) первая (турбулентная) и вторая (ламинарная) для пайки двойной волной. Источник: Emerald Group Publishing Limited
Для изделий на базе смешанного монтажа применятся т.н. «двойная» волна припоя (рис. 7б). Первая волна является узкой, подается из сопла под большим давлением и имеет турбулентный характер. Ее задача – обеспечить смачивание выводов ЭК и исключить формирование полостей с газообразными включениями, оставшимися от разложения флюса. Вторая волна – ламинарная, ее скорость истечения ниже; она разрушает перемычки, образованные первой волной, и завершает формирование паяных соединений. Пример температурного профиля пайки ПП двойной волной представлен на рис. 8.
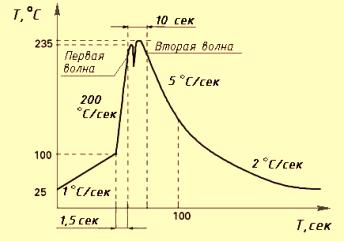
Рис. 8. Пример температурного профиля для бессинцовой пайки ПП двойной волной. Источник: Zetex Semiconductors
Подобно зоне предварительного нагрева, зона пайки также оканчивается «воздушным ножом», удаляющим излишки припоя и разрушающим перемычки.
Ряд моделей оборудования обеспечивает возможность пайки волной в среде инертного газа (азота). Применяется подача азота непосредственно к месту пайки либо создание азотного «туннеля» над всеми зонами. Цель применения азота – уменьшить окисление припоя и флюса, получить более блестящие и яркие паяные соединения, снизить уровень образования шлама и, как следствие, исключить засорение форсунок.
Ручная пайка
Ручная пайка предварительно установленных THT-компонентов проводится с применением аналоговых и цифровых паяльных станций.
Подготовленные поверхности покрывают флюсом непосредственно перед пайкой. Механизм действия флюса заключается в том, что окисные пленки металла и припоя под действием флюса растворяются, разрыхляются и всплывают на его поверхности. Вокруг очищенного металла образуется защитный слой флюса, препятствующий возникновению окисных пленок. Жидкий припой замещает флюс и взаимодействует с основным металлом. Слой припоя постепенно увеличивается и при прекращении нагрева затвердевает.
При проведении процесса пайки крайне важно выдерживать необходимую температуру. Пониженная температура приводит к недостаточной жидкотекучести припоя и плохому смачиванию соединяемых поверхностей. Значительное увеличение температуры вызывает обугливание флюса до активации им поверхностей спая. Следует отметить, что температура жала паяльника, выставленная на паяльной станции, всегда выше реальной температуры пайки, что обусловлено теплоемкостью элементов, участвующих в образовании паяного соединения (сам компонент и его выводы, ПП и элементы проводящего рисунка). Подбор температуры осуществляется в зависимости от применяемого припоя, типа и размера корпуса компонента, материала и топологии ПП.
Важными характеристиками паяльной станции являются:
- быстрый нагрев жала до рабочей температуры;
- точный контроль температуры жала с максимальной частотой (вследствие конструктивных особенностей сочленения нагревателя и жала, расположения термопар и других причин заданная температура жала может отличаться от реальной);
- автоматическая калибровка станции при смене жала либо паяльника;
- быстрая смена жал.
Такими возможностями обладают преимущественно цифровые паяльные станции, которые обеспечивают более точное задание, поддержание и управление температурой паяльника по сравнению с аналоговыми, а также позволяют подключать к станции несколько инструментов.
Для пайки обычно используются жидкий флюс и проволочный припой. Флюс наносится кистью в места пайки. Для пайки в труднодоступных местах, а также для ремонта, применяют трубчатые припои с несколькими каналами флюса внутри. Преимущественно применяются припои со слабоактивированными низкоканифольными флюсами (NC, No-clean – не требующими отмывки) либо среднеактивированные канифольные, для которых отмывка возможна, но не является обязательной при нормальных условиях эксплуатации изделия. Для пайки сильно окисленных поверхностей, а также поверхностей с плохой паяемостью, применяются активированные канифольные флюсы, требующие последующей отмывки в деионизованной воде или органическими растворителями на спиртовой основе. Припои используются как эвтектические (Sn-Pb, Sn-Pb-Ag), так и бессвинцовые (Sn-Cu, Sn-Ag-Cu); поставка осуществляется в катушках.
Типовая последовательность пайки установленных в отверстия компонентов следующая:
- очистка жала паяльника (если необходимо), его облуживание;
- установка температуры жала паяльника на станции;
- выдержка, в процессе которой происходит нагрев жала паяльника до требуемой температуры;
- приведение жала в контакт (одновременный) с КП и выводом ЭК для обеспечения их прогрева, небольшая выдержка (0,5 – 1 сек);
- подача прутка припоя к паяному соединению с образованием связи между выводом и КП (не следует подавать припой непосредственно на жало паяльника во избежание преждевременного выгорания флюса);
- охват припоем вывода по кругу на 360°;
- одновременный отвод прутка припоя и жала паяльника (по направлению вверх вдоль вывода ЭК для образования галтели правильной формы).
Процесс пайки одного соединения должен быть по возможности кратковременным во избежание перегрева ЭК и отслаивания КП, его общее составляет от 0,5 до 2 секунд. При пайке необходимо следить за тем, чтобы паяльник даже на короткое время не прикасался к корпусу ЭК, и чтобы на него не попадали капли припоя и флюса. После работы жало паяльника необходимо облудить для увеличения срока его службы.
Существуют паяльники с одновременной подачей прутка припоя (пайка одной рукой, вторая может использоваться для удержания ЭК и/или ПП), а также станции автоматической непрерывной либо дискретной подачи припоя в точку пайки.
Для готового паяного соединения должны обеспечиваться требования по:
- минимальному углу охвата вывода смачивающим его припоем со стороны пайки (270–330°);
- минимальному проценту заполнения площади КП оплавленным припоем со стороны пайки (75%);
- минимальному заполнению отверстия припоем по высоте (50–100% в зависимости от класса изделия).
Конец вывода должен быть различим в образованном паяном соединении (не должно присутствовать избыточного количества припоя). Поверхность галтелей припоя – вогнутая, непрерывная, гладкая, глянцевая, без темных пятен и посторонних включений. Припой не должен касаться корпуса ЭК. Между мениском, образованным покрытием корпуса на радиальных выводах компонента, и паяным соединением должен быть зазор (минимум 1,2 мм). Не допускается растекание припоя за пределы КП по проводнику.
Селективная пайка
Селективная пайка представляет собой процесс избирательной пайки отдельных ЭК на ПП с отсутствием воздействия на остальные установленные компоненты, и выполняется, как правило, миниволной припоя. Развиваются также системы селективной пайки лазером и горячим газом.
Процесс пайки миниволной припоя во многом схож с обычной пайкой волной, с тем существенным отличием, что происходит пайка не всей ПП, а только отдельных ЭК на ней. Конвейерная система и модуль предварительного нагрева аналогичен по конструкции применяемому в пайке волной припоя. Флюсователи применяются как распылительного, так и точечного типа с одной или несколькими форсунками. Флюс избирательно и точно наносится в точку пайки флюсующей головкой, перемещаемой сервоприводом. Применяются также модули флюсования окунанием со специальными адаптерами, когда необходимо осуществить флюсование отдельных областей ПП. Волна в ванне с припоем, которая также имеет сервопривод перемещения (в некоторых моделях оборудования перемещается ПП), создается сменными соплами-волнообразователями. Существуют также системы селективной пайки с несколькими волнообразователями, выполненными в виде сменной оснастки для конкретного изделия. Такие системы обладают большей производительностью, но значительно меньшей гибкостью. Пайка может производиться в инертной (азотной) среде, чем достигается отсутствие окисления миниволны припоя. Уровень миниволны измеряется бесконтактными способами.
Селективная пайка имеет ряд существенных достоинств по сравнению с ручной и волновой пайкой:
- снижение расхода технологических материалов (флюс, припой, инертный газ) и электроэнергии;
- сокращение времени производственного цикла и числа сотрудников на участке ручной пайки;
- исключение необходимости отмывки;
- возможность пайки разных ЭК на ПП различными припоями на одной установке за один цикл;
- уход от человеческого фактора, повторяемость параметров процесса на всей партии.
Эти достоинства обуславливают все более частый отход производителей от пайки волной и ручной пайки, и применение ими пайки оплавлением для SMD-компонентов и селективной пайки для штырьковых ЭК.
|
 |
|