07 июня 2008
Реболлинг BGA компонентов: технология и оснастка для восстановления шариковых выводов
Введение
Восстановление шариковых выводов компонентов BGA, или реболлинг BGA (от англ. reballing) – процесс воссоздания матрицы шариковых выводов на нижней стороне корпуса компонента взамен поврежденных при операции его демонтажа. Для подавляющего большинства электронных компонентов (ЭК) в корпусах типа BGA операция демонтажа необратимо повреждает его выводы, и операция их восстановления становится совершенно необходимой, если данный ЭК предполагается использовать вновь.
Операция реболлинга может входить в состав техпроцесса ремонта или восстановления сборок в случае использования дорогих компонентов, отбраковка которых при демонтаже с печатной платы приведет к неоправданно больши́м затратам, нерентабельности заказа единичных новых ЭК либо штучной их партии, либо в случае отсутствия по различным причинам данного компонента на предприятии на момент проведения ремонта при необходимости быстро отремонтировать плату.
Также реболлинг применяется некоторыми производителями для замены бессвинцовых шариковых выводов на оловянно-свинцовые с целью избежать т.н. смешанной технологии, которая в настоящее время является предметом активных споров между технологами. Существуют вполне обоснованные мнения, что пайка бессвинцовых BGA компонентов одновременно со свинцовосодержащими изделиями приводит к ухудшению качества паяных соединений, и если закупка BGA с оловянно-свинцовыми шариками затруднена, следует производить замену шариков. Однако данный вопрос выходит за рамки настоящей статьи.
Некоторые производители компонентов не рекомендуют проводить процесс восстановления шариковых выводов вследствие наличия определенного числа циклов теплового воздействия, которым должен подвергнуться компонент. Тем не менее, для большинства компонентов вполне возможно проведение реболлинга, а для многих – неоднократное.
Реболлинг BGA проводится с помощью различных методик, объединяет которые использование специальной оснастки, набора готовых шариков, паяльной пасты либо заготовок с уже установленными шариками. Многие компании выпускают специальные наборы оснастки для реболлинга, инструмента и расходных материалов. Ниже мы остановимся на нескольких получивших наибольшее распространение методах.
Следует отметить, что процесс реболинга требует некоторых навыков, которые могут быть получены в процессе тренировки. Чтобы облегчить этот процесс и сделать его менее затратным, многие производители специально включают в свои наборы для восстановления выводов BGA тестовые макеты компонентов.
При проведении реболлинга, также как и при любой другой операции с BGA компонентами, важно выполнять ряд требований по защите от воздействия статического электричества и принять меры к удалению избыточного количества влаги из корпусов компонентов. Подробнее эти меры изложены в статьях нашего портала «Основы статического электричества» и «Чувствительность электронных компонентов к влажности».
Идентификация компонента
Перед проведением реболлинга с помощью специальных комплектов оснастки необходимо точно знать, какой тип BGA корпуса предполагается подвергнуть этому процессу. Это соображение касается как материала корпуса, так и шариковых выводов компонента. Ниже приводятся описания наиболее распространенных типов таких корпусов с этой точки зрения [2].
- Керамический компонент с шариковыми выводами, изготовленными из высокотемпературного припоя (90Pb/10Sn). Шарики выглядят как гладкие сферы, окруженные мениском из удерживающего их более мягкого эвтектического припоя (обычно с добавкой 2% серебра), слегка отличающегося по цвету. Для реболлинга таких корпусов пригодны только те методы, с помощью которых возможно нанесение паяльной пасты для крепления шариков. Большинство выпускаемых наборов для реболлинга непригодны для этой цели.
- Пластиковые или керамические компоненты с шариковыми выводами, изготовленными из эвтектического припоя. У всех пластиковых BGA-компонентов шарики сформированы из эвтектического припоя (также обычно с добавкой 2% серебра) непосредственно на контактных площадках. Ряд ремонтных наборов (в частности, [2]) возможно применять для реболлинга только таких компонентов.
- Пластиковые или керамические компоненты с шариковыми выводами, изготовленными из бессвинцового припоя. Применяемый сплав – как правило, Sn96.5Ag3Cu0.5 с температурой плавления 217-220°C.
- Компоненты Tape Ball Grid Array (TBGA). ЭК оснащены частично оплавленными шариками из высокотемпературного припоя (90Pb/10Sn). Если данные компоненты правильно демонтированы с печатной платы с соблюдением необходимого температурного профиля, они не теряют свои шариковые выводы, не требуют реболлинга и могут быть успешно установлены в новую позицию.
Состав наборов для реболлинга
Типичный набор для восстановления шариковых выводов может включать в себя следующие основные компоненты (на примере наборов [2, 13, 20, 21], рис. 1):
- Механическое приспособление для закрепления корпуса BGA-компонента и трафарета и последующего помещения их совместно в печь оплавления.
- Набор трафаретов с различным расположением апертур под шариковые выводы, шагом и диаметром выводов либо готовые одноразовые трафареты с уже уложенными в их апертуры шариками.
- Флюс-карандаш для флюсования контактных площадок.
- Деионизированная вода для отмывки.
- Набор шпателей и ракель для нанесения пасты.
- Плетенка для удаления остатков припоя.
- Каптоновая клейкая лента или другой термостойкий материал для крепления компонентов к трафарету и/или приспособлению.
- Набор эвтектических шариковых выводов различного диаметра.
- Пинцеты, иголки для размещения шариков в апертурах, антистатическая щеточка, отвертка для завинчивания винтов приспособления.
- Антистатический поддон для сбора излишков шариков, антистатическая кювета для отмывки.
- Салфетки для протирки с малым уровнем пылевыделения, пропитанные изопропиловым спиртом.
- Макеты BGA компонентов для тренировки и приобретения необходимых навыков реболлинга.
- Инструкция по выполнению технологического процесса.
Набор не обязательно должен содержать все вышеперечисленные компоненты.
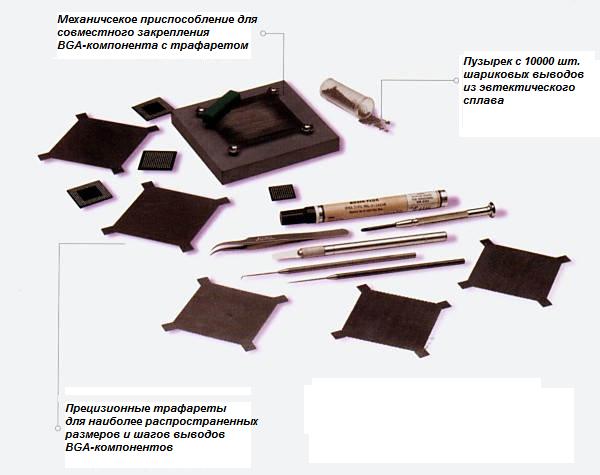
Рис. 1. Пример набора для реболлинга (Weller WPRB1000). Фото из [1]
Оборудование и оснастка для реболлинга
Следующие компоненты, как правило, не входят в наборы для реболлинга, и оснащение ими рабочего места возлагается на пользователя [13]:
- Печь или сушильный шкаф (необходимы для предварительной просушки чувствительных к влажности компонентов).
- Система пайки горячим воздухом либо конвекционная печь оплавления.
- Емкость (например, лабораторный стакан) для отмачивания загрязненных флюсом деталей приспособлений и оснастки.
- Рабочее место, подготовленное в соответствии с требованиями по защите от воздействия статического электричества и удалению вредных летучих соединений.
- Микроскоп (рекомендуется для проведения контроля).
- Деионизированная вода.
- Напалечники или перчатки.
Возможно также применение специальных установок для реболлинга, описанных ниже в данной статье. В комплект их поставки входят практически все необходимые компоненты из наборов для реболлинга.
Последовательность операций реболлинга
Все техпроцессы реболлинга можно разделить на две большие группы: с использованием готовых шариков и с использованием паяльной пасты. Существует ряд наборов для проведения реболлинга, позволяющих применять обе эти методики.
Находят применение и другие технологии восстановления шариков: например, применение одноразовых картриджей с шариками, размещенными на матрице из водосмываемой бумаги [12 – 14] либо готовых пленочных трафаретов из полиимида с уложенными шариками [8 – 11].
Использование готовых шариков, хотя и предусматривает дополнительные затраты на их приобретение, позволяет избежать проблем с неплотным прилеганием трафарета, неравномерностью усилия на ракеле при нанесении пасты, что может привести к образованию шариков неодинаковых размеров и, соответственно, проблемам при последующей пайке такого компонента. Однако процесс с применением шариков требует большей аккуратности и трудоемкости с точки зрения недопущения пропусков.
Вне зависимости от применяемого метода, все подготовительные и заключительные операции одинаковы. Ниже приведен список основных операций техпроцесса:
- Предварительная сушка компонента
- Подготовка компонента
- Выбор материала для реболлинга
- Флюсование компонента
- Совмещение и закрепление специального трафарета на компоненте
- Закрепление собранных вместе трафарета и компонента в специальном механическом приспособлении
- Укладка шариков/нанесение пасты (если необходимо)
- Оплавление
- Изъятие готового компонента из приспособления
- Очистка
- Сушка
- Контроль
Материалы для реболлинга
Флюс
Разработчики технологий реболлинга и компании, занимающиеся выпуском комплектов для его осуществления, рекомендуют использовать клейкие флюсы: канифольные средней активности (RMA) [2] либо водосмываемые на основе органических кислот с уровнем активности от слабого до среднего [4, 13], хотя отмечается, что может быть использовано большинство типов флюсов. Не следует использовать водосмываемые флюсы с высокой степенью активности (в частности, используемые в военной отрасли HF-1189-SP1 тип WSF-0, стандарт MIL-F-14256-F), так как они могут очистить трафареты до такой степени, что будет происходить смачивание их припоем при оплавлении, и вследствие этого такие трафареты станут непригодными для осуществления реболлинга и потребуют замены.
Также утверждается [13], что флюсы, не требующие отмывки, плохо подходят для применения при реболлинге, так как, во-первых, имеют слишком низкую активность, чтобы обеспечивать хорошее смачивание; во-вторых, в случае применения готовых трафаретов из водосмываемой бумаги ее удаление будет существенно затруднено; в-третьих, требуемое количество флюса будет настолько велико, что, скорее всего, потребуется дополнительная отмывка.
Паяльная паста
Паяльная паста обычно не включается в состав наборов для реболлинга, так как срок ее хранения ограничен. Для обычных пластиковых корпусов BGA рекомендуется использовать пасту 62Pb/32Sn/2Ag, которая переходит в текучее состояние при сравнительно низкой температуре 189°С. Использование паст 90Pb/10Sn может привести к отказу компонента при термоциклировании по причине разницы в ТКР пасты и вывода. Согласно [2], содержание металла в пасте должно находиться в пределах 85 – 93%, шаг сетки – от 325 до 500 ячеек/кв. дюйм по ASTM B-214, что соответствует типу 3 IPC/EIA J-STD-005 (размер частиц не более 50 мкм), вязкость – от 350 до 500 кспз по Брукфилду.
Трафареты
Трафареты могут входить в состав наборов для реболлинга либо изготавливаться на заказ под конкретный компонент. Распространены универсальные трафареты, представляющие собой матрицу отверстий соответствующего диаметра и шага выводов, расположенную ровными рядами либо в шахматном порядке. Если в центре корпуса есть контактные площадки для теплоотвода, окруженные пустой областью, все равно, возможно применять универсальный трафарет – достаточно не укладывать шарики в избыточные апертуры или наносить пасту во все апертуры трафарета (там, где контактных площадок нет, шарики сформируются, но не создадут паяного соединения с корпусом).
Трафареты для реболлинга изготавливаются из высококачественной нержавеющей стали, в противном случае (например, при недостаточной толщине) данный трафарет при нагреве может «повести», что приведет к смещению отпечатков пасты и браку при реболлинге. Диаметр отверстия обычно выполняется на 5 – 10 мкм больше диаметра ремонтного шарика, апертура имеет коническую форму для облегчения снятия трафарета при использовании паяльной пасты. Толщина трафарета обычно соответствует диаметру шарика.
Подготовка микросхемы
Процедура подготовки микросхемы к последующему реболлингу заключается в удалении частично оплавленных выводов и остатков припоя с контактных площадок корпуса BGA-компонента. Иногда данная операция, по аналогии с реболлингом, называется деболлингом (debolling).
Для ее выполнения применяются различные инструменты, среди которых:
- ручной паяльник и плетенка для удаления припоя;
- инструменты, осуществляющие отсос припоя посредством вакуума;
- низкотемпературные системы пайки волной.
Вакуумный процесс наиболее безопасен для микросхемы, однако требует значительного времени. Применение паяльника и плетенки, являясь более быстрым процессом, может в случае неправильного исполнения либо неверного выбора размеров плетенки привести к отслоению контактных площадок ИС или повреждению паяльной маски. Применение систем пайки волной требует, помимо наличия такого оборудования, точного поддержания требуемой температуры при снятии припоя, а также знания состава удаляемого сплава с целью предотвращения загрязнения им паяльной ванны.
Удаление припоя с помощью вакуумного отсоса производится следующим образом (на примере паяльных станций Martin, [16], рис. 2):
- на контактные площадки наносится флюс;
- паяльная станция оснащается насадкой для подачи горячего воздуха и вакуумным отсосом припоя (меньшая насадка соответствует меньшему размеру контактных площадок); температура устанавливается равной 350°C, скорость подачи воздуха – 10 л/мин, мощность нижнего ИК-нагрева – 300 Вт;
- в процессе удаления припоя инструмент подачи горячего воздуха должен находиться под углом около 45° относительно горизонтали таким образом, чтобы при удалении припоя с одной контактной площадки следующая подогревалась бы потоком горячего воздуха для облегчения проведения операции; инструмент удаления припоя – слегка наклонен и расположен над оплавленным припоем.
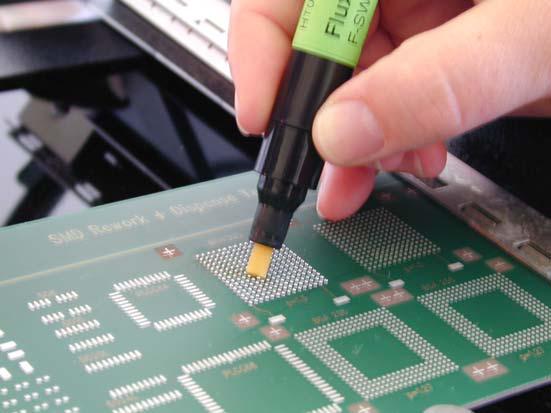
а)
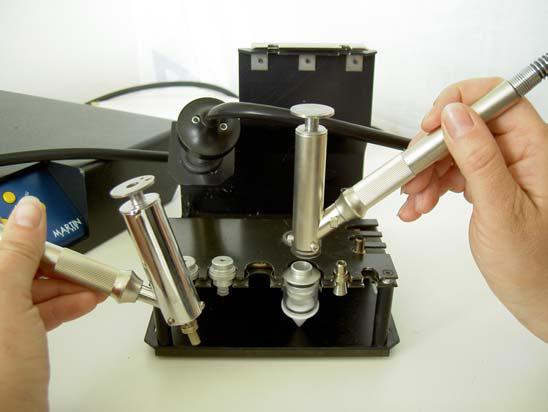
б)
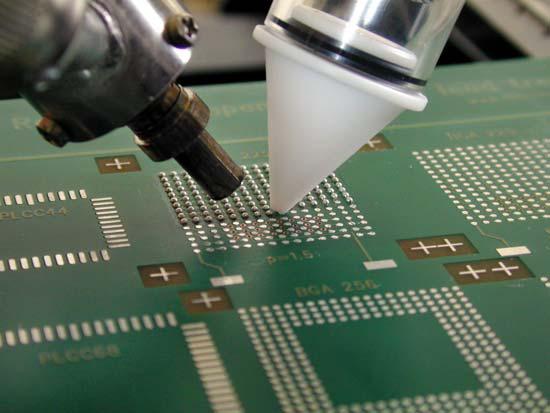
в)
Рис. 2. Удаление припоя с помощью вакуумного отсоса:
а) нанесение флюса на контактные площадки;
б) оснащение паяльной станции насадкой и отсосом припоя;
в) процесс удаления припоя.
Фото из [16]
В случае применения паяльника и плетенки последовательность действий следующая (на примере методик [4] и [13], рис. 3):
- положить компонент на антистатический коврик контактными площадками вверх;
- нанести флюс на обращенную вверх сторону компонента (а);
- накладывая плетенку на флюсованную поверхность компонента, прогревать ее приложенным сверху паяльником с плоским наконечником, добиваясь полного расплавления и удаления остатков припоя и избегая сильного нажима на контактные площадки во избежание их царапания или повреждения корпуса компонента (б);
- перемещая плетенку по поверхности компонента, добиться полного удаления припоя;
- окончательно очистить компонент с помощью чистой плетенки.
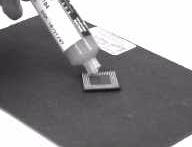
а)
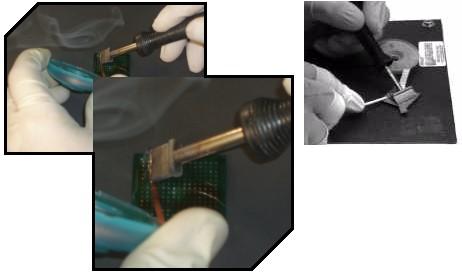
б)
Рис. 3. Удаление припоя с помощью паяльника и плетенки
а) нанесение флюса на контактные площадки (файл SQReballing01.jpg);
б) приложение плетенки и паяльника (файл SQReballing02.jpg).
Фото из [4]
Хорошей практикой считается оставить часть припоя на контактных площадках с целью облегчения последующего процесса реболлинга. Покрытие контактной площадки должно быть плоским и равномерным.
Далее производится очистка поверхности компонента от остатков флюса не оставляющей волокон салфеткой, смоченной в изопропиловом спирте (рис. 4). Чем быстрее после завершения процесса будет произведена такая очистка, тем легче будет избавиться от остатков флюса. В процессе очистки необходимо всегда поддерживать обратную сторону компонента и не допускать изгибания его углов.
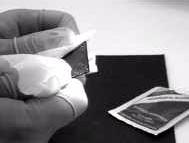
Рис. 4. Очистка поверхности компонента от остатков флюса при помощи салфетки. Фото из [13]
Завершает процесс деболлинга контроль целостности контактных площадок, степени их чистоты и отсутствия отслоения, проводимый с помощью стереомикроскопа или другого соответствующего оптического инструмента. Необходимо добиться полного удаления шариков припоя. На рис. 5 показаны чистые контактные площадки (а) и площадки с оставшимися загрязнениями (б).
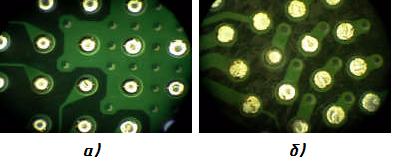
Рис. 5. Внешний вид чистых (а) и загрязненных (б) контактных площадок под микроскопом. Фото из [13]
В качестве дополнительной процедуры [2, 13] (рис. 6) рекомендуют проводить очистку компонента с помощью деионизированной воды, нанесенной на поверхность компонента, и антистатической щетки из конского волоса, совершающей прямые в двух перпендикулярных направлениях, а затем круговые движения (а), после чего компонент ополаскивается деионизированной водой (б), просушивается сухим воздухом и снова контролируется на предмет повреждения контактных площадок. Погружение компонента в воду не допускается.
Рекомендуется использовать наиболее сильный очищающий реагент из допустимых для данного типа флюса и материалов корпуса компонента.
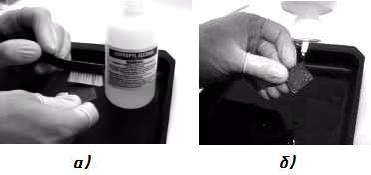
Рис. 6. Дополнительная процедура очистки компонента:
а) с помощью щетки;
б) ополаскивание.
Фото из [13]
Флюсование компонента
Клейкий флюс наносится на нижнюю сторону компонента с помощью шприца и далее распределяется антистатической щеточкой по поверхности. Флюс обязательно должен обладать клейкими свойствами, так как это исключительно важно для последующего прикрепления шариковых выводов. Он также обеспечит подготовку поверхности контактных площадок и необходимое смачивание в процессе оплавления шариков.
Совмещение и закрепление специального трафарета на компоненте
Совмещение и выравнивание трафарета относительно корпуса BGA-компонента производится по контактным площадкам, расположенным в противоположных углах корпуса. Для предотвращения их взаимного смещения применяется термостойкая лента из каптона с клейким слоем. Она наклеивается по периметру компонента со стороны, противоположной стороне с контактными площадками, таким образом, чтобы около 10 мм ее ширины выступали за пределы корпуса. Теперь, после совмещения трафарета и корпуса, достаточно просто прижать выступающую часть ленты к трафарету и тем самым скрепить их вместе. В таком виде собранные вместе трафарет и корпус помещаются в механическое приспособление [2].
Следует отметить, что на трафареты для реболлинга, как правило, нанесена маркировка, облегчающая определение правильной стороны трафарета при закреплении. Так, в наборах Weller обозначение «THIS FACE DOWN» относится к стороне трафарета, которая должна прилегать к компоненту. Это важно, так как апертуры трафарета имеют коническую форму для облегчения снятия его с готового компонента. Обозначение «THIS FACE UP» наносится на ту сторону трафарета, которая должна быть обращена вверх при установке собранных вместе компонента и трафарета в механическое приспособление.
Закрепление собранных вместе трафарета и компонента в специальном механическом приспособлении
Существуют различные конструкции таких приспособлений.
Например, основой конструкции приспособления из набора Weller является керамическая плита с четырьмя винтовыми креплениями по краям [1]. Компонент с трафаретом размещается на пластине, причем под нижнюю сторону корпуса подкладываются по необходимости одна или несколько стеклянных пластин различной толщины, благодаря чему обеспечивается «грубая» высота пакета для последующего точного закрепления его винтами. Трафарет слегка поворачивается до того момента, пока винты не попадут в соответствующие отверстия «под ключ» в углах трафарета. Возможно, для этого потребуется слегка нажать на углы трафарета. Пластины должны быть подобраны так, чтобы в собранном состоянии поверхность трафарета была ровной и горизонтальной; она не должна прогибаться при нажатии на любую ее точку. При наклоне приспособления стеклянные пластины не должны смещаться.
Также в более простом варианте реализации процесса возможно аккуратно прикрепить компонент с трафаретом на керамическую пластину термостойким скотчем.
Укладка шариков/нанесение паяльной пасты
Укладка шариков
Перед укладкой шариков необходимо установить механическое приспособление в специальный антистатический поддон. Он позволит легко собрать просыпавшиеся шарики после окончания процедуры и снова пересыпать их в контейнер для хранения. Шарики укладываются в апертуры трафарета с помощью специальной антистатической мягкой щеточки, «помогающей» шарикам проваливаться в апертуры. Необходимо убедиться, что каждая контактная площадка компонента получила свой шариковый вывод. Если трафарет универсальный и, соответственно, больше по размерам, чем компонент, то нет необходимости заполнять все его апертуры.
Нанесение паяльной пасты
Паяльная паста наносится на поверхность трафарета наиболее подходящим по размеру шпателем из набора. Паста должна быть нанесена в каждую апертуру трафарета. После этого необходимо провести по поверхности трафарета каучуковым ракелем и удалить с нее излишки пасты. Трафарет должен быть полностью очищен от пасты. Наклеенная предварительно каптоновая лента поможет избежать наличия большого количества избыточной пасты вдоль краев компонента под трафаретом. Хотя эта паста и не оказывает отрицательного влияния на результат реболлинга, она расходуется и оплавляется впустую, а после окончания операции трудно поддается удалению.
Необходимо наносить пасту на весь компонент целиком, независимо от того, есть ли в центре его корпуса контактные площадки. Если их нет, то шариковые выводы будут сформированы, но не прикрепятся к корпусу компонента.
При нанесении пасты особенно важно, чтобы трафарет плотно прилегал к поверхности корпуса.
Оплавление
С уложенными шариками
Далее приспособление помещается в обычную печь оплавления для формирования шариковых выводов. Как и во всех прочих операциях оплавления, одной из ключевых составляющих успеха реболлинга является соблюдение правильного температурного профиля. Настоятельно рекомендуется использовать рекомендованный производителем BGA-компонента профиль оплавления, не допуская превышения максимально допустимой температуры нагрева, составляющей для BGA-компонентов ~220–230°С, и обеспечивая равномерный нагрев без значительных температурных градиентов. После окончания оплавления цвет шариковых выводов должен быть светло-коричневым, более темный цвет свидетельствует о превышении допустимой скорости обдува горячим воздухом [13].
Ряд производителей также допускает использование ремонтных систем с нагревом горячим воздухом [2]. Необходимо использовать насадку достаточно большого размера для размещения под ней корпуса компонента целиком и также как можно более точно воспроизводить профиль оплавления в печи. В процессе предварительного нагрева сопло должно размещаться на высоте ~1" (~25,4 мм) над трафаретом, а во время этапов подъема температуры и достижения пиковой температуры оплавления – находиться на уровне ~1/8" (~3 мм).
Охлаждение должно производиться при температуре окружающей среды, принудительное охлаждение не допускается. Затем сопло убирается от приспособления.
С нанесенной паяльной пастой
При использовании пасты некоторые производители [2] не рекомендуют применять традиционную печь оплавления – следует использовать ремонтную станцию с подачей горячего воздуха и маленьким соплом (7х7 или 12х12 мм). Необходимо также как можно более точно воспроизводить профиль оплавления в печи. Последовательность действий при этом следующая:
Предварительный нагрев. Поместить приспособление на расстоянии ~1" (~25,4 мм) под воздушным соплом, установить температуру 177°C, а скорость воздушного потока – в положение «Low» («Низкая»). В зависимости от размера компонента, предварительный нагрев должен длиться от 1 до 3 мин. Если компонент очень крупный, то его необходимо медленно перемещать под воздушным потоком, добиваясь прогрева компонента целиком.
Оплавление. Далее необходимо опустить сопло до высоты ~1/2" (~12,5 мм) над компонентом и установить температуру от 204°C до 260°C. Скорость воздушного потока должна быть установлена в положение «High» («Высокая»). Необходимо перемещать приспособление под воздушным потоком для прогрева всей поверхности компонента. Рекомендуется начать с центра компонента и постепенно продвигаться к периферии корпуса – круговыми движениями или по спирали. Это будет способствовать быстрому формированию шариковых выводов и минимизации температурных градиентов по поверхности корпуса. После того, как паяльная паста начнет оплавляться и все шариковые выводы будут сформированы, можно переходить к заключительному этапу.
Заключительный этап. Установки температуры и воздушного потока прежние. Сопло следует опустить до ~1/4" (~6 мм) над трафаретом. Необходимо прогреть всю поверхность компонента, но быстрее, чем это было сделано при предварительном нагреве. Эта стадия в большинстве случае должна продолжаться 15 с. Полное оплавление припоя происходит, когда цвет шарика становится из тускло-серого блестящим, а его поверхность начинает отражать свет.
Охлаждение также должно производиться при температуре окружающей среды в течение по крайней мере 1 мин., принудительное охлаждение не допускается.
Температурный профиль оплавления
Каждый корпус BGA-компонента, подвергаемый процессу реболлинга, может потребовать своего профиля оплавления. Следует, в общем случае, руководствоваться информацией производителя компонента, если же прямые указания отсутствуют, то начать с базового профиля, подстраивая его параметры в соответствии с материалом, массой и размером корпуса, а также применяемыми материалами припоя шариковых выводов.
Не рекомендуется подвергать корпуса нагреву, превышающему 220°C. Для выполнения реболлинга рекомендуется применение любой установки, реализующей пайку горячим воздухом, при наличии управляемого по времени цикла нагрева, с температурным диапазоном 20- 240°C и принудительной конвекцией.
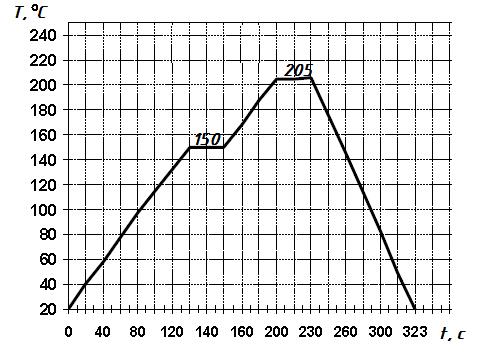
Рис. 7. Базовый температурный профиль оплавления для реболлинга. Рисунок из [13]
Базовый вид температурного профиля для эвтектического сплава шариковых выводов (по данным [13]) приведен на рис. 7. Он реализует скорость подъема температуры ~1°C/с, пиковую температуру от 200 до 210°C, время нахождения при температуре, превышающей температуру ликвидуса (183°C) от 45 до 75 с. Более крупные компоненты или компоненты с теплоотводящими элементами конструкции могут потребовать более длительных циклов оплавления. Для разработки правильного температурного профиля под каждую конкретную установку оплавления необходимо воспользоваться термопарами, размещаемыми в различных областях корпуса компонента.
Вынимание готового компонента из приспособления
Необходимо дождаться полного охлаждения приспособления после оплавления, затем попытаться снять трафарет с компонента путем его легкого изгибания. Для облегчения отделения трафарета от компонента может понадобиться применение небольшого количества отмывочной жидкости.
Если трафарет не отделяться легко, важно не пытаться снять его силой с помощью рычага. Лучший способ – снять каптоновую ленту и дополнительно прогреть трафарет горячим воздухом.
Реболлинг с использованием готовых трафаретов с уложенными шариками
Существуют и альтернативные методы восстановления шариковых выводов, в частности, те из них, в которых применяются готовые трафареты с уже уложенными шариками [8, 12, 13]. В качестве материала основы для таких трафаретов используется либо водосмываемая бумага, либо полиимидная пленка.
Технология с применением готовых трафаретов из водосмываемой бумаги
Первая технология компании Emulation Technologies Inc. носит название SolderQuik™ [12 – 14] и предусматривает применение готовых трафаретов из водосмываемой бумаги, а также механического приспособления – специального фиксатора (под конкретный размер либо регулируемого) для компонента и трафарета. Процедура реболлинга при этом состоит из следующих основных этапов ([13], рис. 8):
- положить готовый трафарет на ступеньку фиксатора логотипом SolderQuik™ вниз, убедиться в том, что трафарет свободно располагается в фиксаторе – если трафарет во вставленном состоянии будет изогнут, реболлинг не получится;
- нанести небольшое количество флюса на нижнюю поверхность корпуса; кисточкой распределить его по поверхности таким образом, чтобы каждая контактная площадка оказалась покрыта тонким слоем флюса;
- вставить корпус в приспособление стороной с нанесенным флюсом к трафарету; прижать корпус к трафарету путем легкого нажатия на него; убедиться в плотном совмещении деталей и плоском расположении компонента в фиксаторе;
- поместить фиксатор в печь либо на станцию пайки горячим воздухом и произвести оплавление с использованием соответствующего температурного профиля;
- используя пинцет с тупыми захватами, вынуть фиксатор из печи или снять с паяльной станции и поместить в антистатический поддон; дать охладиться в течение около 2 мин., прежде чем вынимать компонент из фиксатора;
- после охлаждения корпуса, вынуть его из фиксатора и поместить его шариковыми выводами вверх в поддон для отмывки;
- нанести деионизированную воду на трафарет и выждать ~30 секунд для отмокания бумажной подложки;
- используя пинцет с заостренными захватами, снять бумажную подложку с корпуса, захватив ее при этом с одного угла; подложка должна сняться в виде одного листа; если она рвется в процессе снятия, остановиться и добавить еще деионизированной воды и выждать 15 – 30 с, после чего продолжить процесс;
- удалить случайно оставшиеся клочки бумаги с помощью пинцета; необходимо соблюдать осторожность, чтобы острыми захватами пинцета не повредить паяльную маску компонента;
- сразу же произвести отмывку компонента с помощью щетки и большого количества деионизированной воды (подробнее см. выше при подготовке компонента к реболлингу);
- произвести ополаскивание деионизированной водой, чтобы удалить небольшие частицы флюса и бумаги, оставшиеся после предшествующей операции отмывки; не следует вытирать компонент насухо.
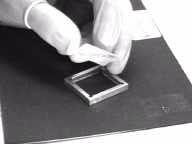
а)
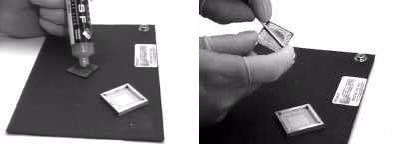
б)
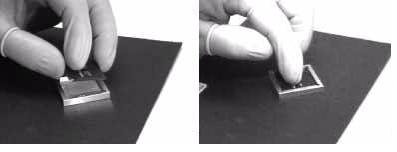
в)
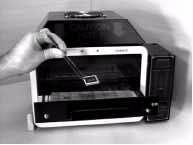
г)
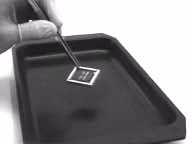
д)
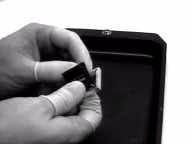
е)
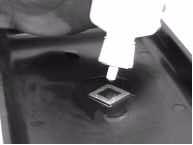
ж)
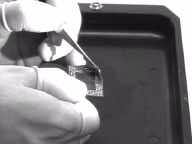
з)
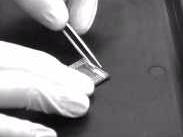
и)
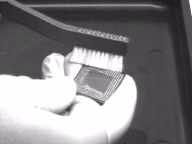
к)
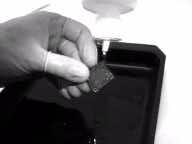
л)
Рис. 8. Процедура реболлинга для фиксатора и готовых трафаретов из водосмываемой бумаги:
а) закрепление трафарета в фиксаторе;
б) флюсование компонента;
в) закрепление компонента в фиксаторе;
г) оплавление;
д) вынимание фиксатора из печи;
е) вынимание корпуса из фиксатора;
ж) отмокание бумажной подложки;
з) снятие бумажной подложки;
и) удаление пинцетом клочков бумаги;
к) отмывка компонента;
л) ополаскивание компонента.
Фото из [13]
Дальнейшая процедура инспекции аналогична применявшейся при подготовке микросхемы к реболлингу. Для проверки качества отмывки следует использовать тестеры ионных загрязнений. На рис. 9 показаны чистые шариковые выводы (а) и выводы, окруженные слоем остатков флюса (б).
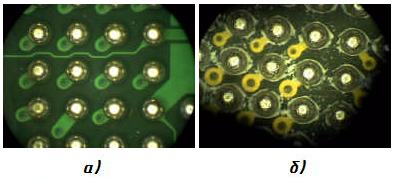
Рис. 9. Внешний вид чистых шариковых выводов (а) и коррозионных остатков флюса под микроскопом. Фото из [13]
Большое значение имеет своевременная очистка фиксаторов, которые при долговременном использовании становятся грязными и липкими из-за наростов флюса. Грязный фиксатор может стать причиной неправильной установки компонента и нарушения всего процесса реболлинга.
Очистку фиксаторов следует проводить также в деионизированной воде, предварительно дав фиксатору отмокнуть в ней в течение ~15 мин., затем применив щетку для очистки, ополоснув и просушив в воздушном потоке. Для фиксаторов различных конструкций для достижения наилучших результатов рекомендуется применять ультразвуковую очистку.
Невозможно изготовить полный набор фиксаторов для осуществления реболлинга всех выпускаемых компонентов BGA. Опционально могут поставляться регулируемые фиксаторы (рис. 10), которые возможно настроить на любой размер корпуса от 5 до 57 мм [13], и которые также возможно применять для реболлинга прямоугольных корпусов.
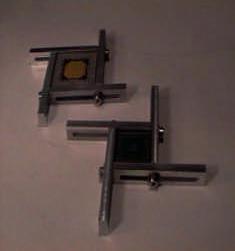
Рис. 10. Регулируемый фиксатор. Фото с сайта [13]
Такой фиксатор с четырьмя подвижными плечами настраивается с помощью четырех регулировочных винтов под конкретный корпус, который помещается в гнездо на ступеньку фиксатора, а плечи подгоняются под необходимые размеры с каждой стороны (рис 11). Трафарет должен помещаться в фиксаторе без прогибания, в противном случае необходимо перенастроить фиксатор.
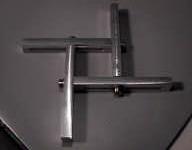
Рис. 11. Настройка регулируемого фиксатора. Фото из [13]
Технология с применением готовых трафаретов из полиимидной пленки
Вторым примером подобной технологии служит EZReball™ от компании BEST [8 – 11], основой которой являются одноразовые готовые трафареты из полиимида, в выполненные лазером апертуры которых заранее уложены шарики. Трафарет имеет подложку с нанесенным на нее термореактивным адгезивом на акриловой основе, устойчивым к действию растворителей и надлому, благодаря чему шарики удерживаются в своих апертурах. Данные трафареты могут иметь любую матрицу апертур под различные диаметры шариков и шаги их расположения.
Преимущества таких трафаретов – в незначительных требованиях к навыкам оператора: совмещение осуществляется по краям корпуса, так как габариты трафарета соответствуют габаритам компонента. После формирования выводов трафарет легко снимается с компонента, при этом не требуется дополнительных операций по отмывке, как это происходит в случае использования трафаретов из водосмываемой бумаги.
Данная технология может использоваться для размеров шариков до 0,15 мм и шага до 0,4 мм. Стандартно поставляются шарики из традиционного сплава Sn63Pb37 с температурой оплавления 183°C, а также бессвинцовые – из Sn96.5Ag3Cu0.5 (217-220°C), прочие сплавы доступны на заказ. Также существует возможность добавления к уже существующей матрице выводов компонента одного или нескольких шариков, не получившихся в результате предыдущей операции реболлинга, с помощью специального ремонтного трафарета.
В качестве оборудования для оплавления метод позволяет использовать как печи оплавления, так и ремонтные центры.
Последовательность основных операций при этом следующая (рис. 12):
- Нанести флюс на поверхность компонента.
- Совместить трафарет с уложенными шариками с корпусом, выровняв их по углам; после совмещения слегка нажать на компонент.
- Закрепить трафарет с компонентом на пластине термостойким скотчем; произвести оплавление.
- После оплавления удалить трафарет с компонента (шариковые выводы будут слегка уплощенными, но это допустимо).
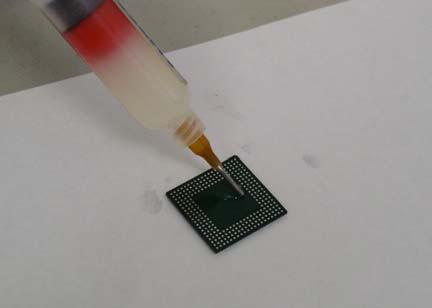
а)
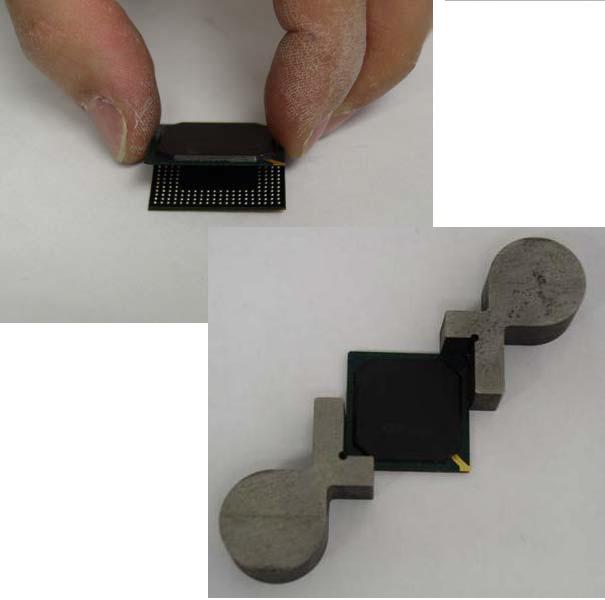
б)

в)

г)
Рис. 12. Процедура реболлинга для готовых трафаретов из полиимида:
а) флюсование компонента;
б) совмещение компонента и трафарета;
в) закрепление компонента с трафаретом на пластине; оплавление
г) удаление трафарета с компонента.
Фото из [10]
Подготовительные и заключительные операции по подготовке компонента и отмывке аналогичны вышеописанным. Адгезив после снятия трафарета не оставляет следов на выводах.
Можно также использовать данную технологию для проведения реболлинга керамических BGA-компонентов с выводами из высокотемпературного припоя, которые требуют нанесения паяльной пасты на контактные площадки корпуса. В этом случае следует совместить компонент с полиимидным трафаретом StencilQuik, нанести пасту ракелем в апертуры, затем прикрепить трафарет EZReball™ и провести стандартную процедуру оплавления. Затем необходимо аккуратно снять трафарет StencilQuik.
Автоматизированные методы реболлинга
Существует также ряд установок, позволяющих автоматизировать процесс реболлинга. В частности, на рынке существуют устройства оплавления с соответствующей оснасткой, предназначенные специально для проведения реболлинга [17]. В их комплект поставки включаются минипечи оплавления различных размеров, наборы шариковых выводов, трафаретов и рамок для установки компонентов, а также игла для облегчения размещения шариков в апертурах. Дополнительно системы могут быть укомплектованы двухканальными модулями измерения температуры с двумя термопарами и каптоновой лентой для крепления, инструментами для удаления остатков припоя, монитором для редактирования температурных профилей и индикации температуры.
Последовательность операций при этом следующая (рис. 13):
- В приспособление устанавливается соответствующим образом очищенный от остатков припоя и профлюсованный компонент контактными площадками вверх, затем на него сверху устанавливается соответствующий трафарет;
- Выбираются шарики соответствующего типа и размера из набора, часть из них рассыпаются по трафарету и помещаются во все апертуры при помощи иголки.
- Все лишние шарики должны быть осторожно перенесены обратно в контейнер, для чего в окантовке корпуса минипечи предусмотрена канавка;
- Инструмент подачи горячего воздуха устанавливается в перевернутом виде в магнитный держатель;
- На инструмент сверху устанавливается минипечь и закрывается крышкой; выбирается соответствующий температурный профиль и запускается процесс оплавления;
- После окончания программы необходимо выждать, пока минипечь остынет, после чего достать компонент и снять трафарет.
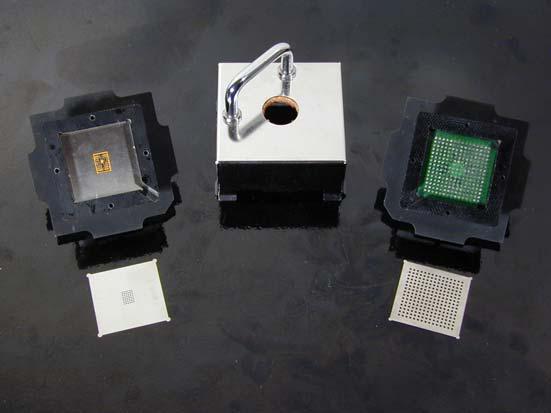
а)
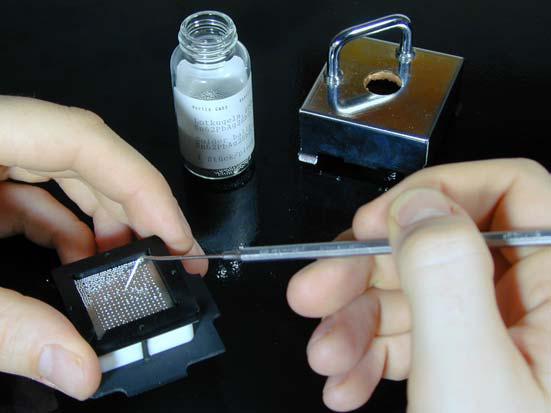
б)
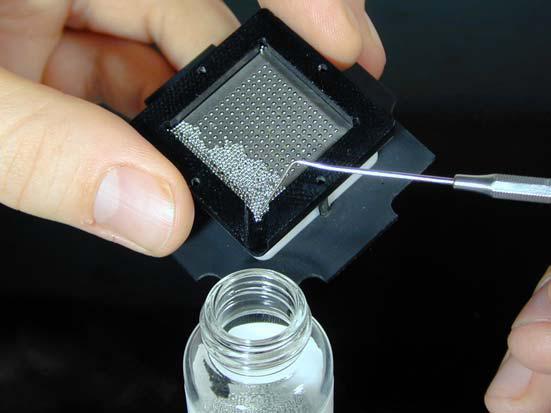
в)
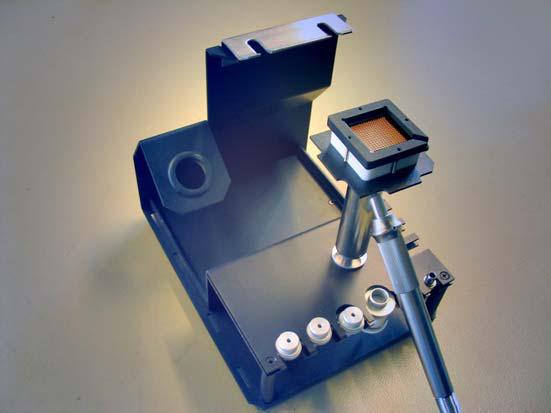
г)
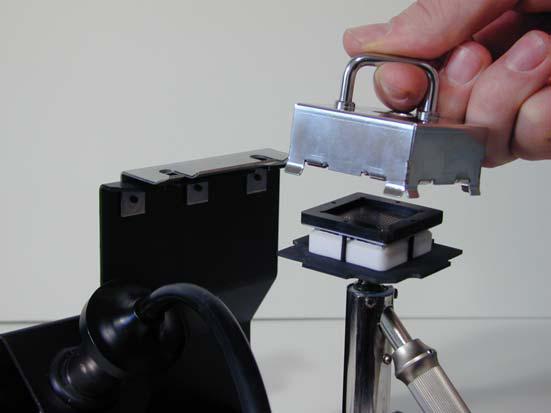
д)
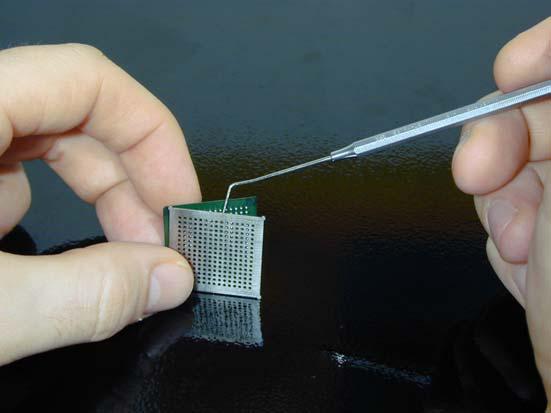
е)
Рис. 13. Последовательность операций при реболлинге с применением минипечи
а) установка компонента и трафарета в приспособление;
б) расстановка шариков в апертуры трафарета;
в) ссыпание лишних шариков в контейнер;
г) установка инструмента подачи горячего воздуха;
д) установка минипечи;
е) вынимание компонента, снятие трафарета.
Фото из [16]
Внешний вид такой установки показан на рис. 14.
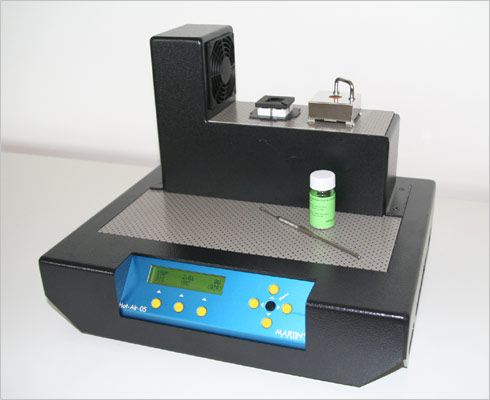
Рис. 14. Установка Martin 04.5 с минипечью оплавления для реболлинга. Фото из [17]
Существуют и более экономичные варианты реализации систем для реболлинга, имеющие в своем составе держатель BGA-компонентов, несколько адаптеров и трафаретов для совместного их закрепления с помощью каптоновой ленты на держателе [18, 19]. Система использует ИК-нагрев, что позволяет отказаться от минипечей и устройства подачи горячего воздуха со своей системой управления. Пользователю достаточно выбрать необходимую температуру и номер профиля оплавления, вставить подготовленный компонент, закрыть крышку устройства и нажать кнопку Start. С помощью функции обучения установка автоматически вычисляет продолжительность процесса реболлинга. Вставляя крючок в окно в крышке, пользователь может установить время достижения точки оплавления и сообщить об этом системе, нажав кнопку Stop. Блок управления автоматически вычислит дополнительное время, необходимое для образования надежного паяного соединения шариков с корпусом BGA-компонента и сохранит эти данные в одной из одиннадцати доступных ячеек памяти. После этого крышка устройства автоматически открывается и начинается процесс охлаждения посредством встроенного вентилятора.
Весь процесс реболлинга, по данным разработчика, занимает около трех минут. Внешний вид данной установки, а также входящая в ее комплект поставки оснастка показана на рис 15.
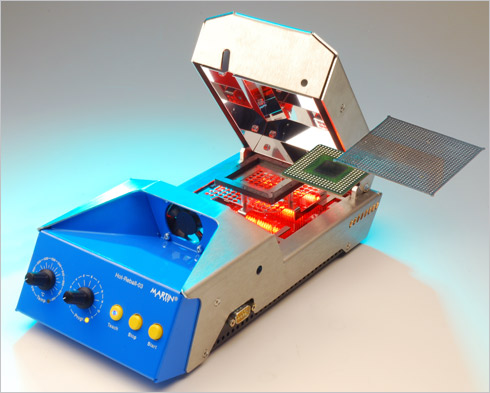
а)
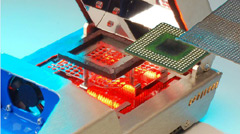
б)
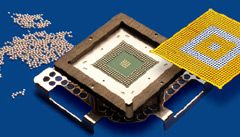
в)
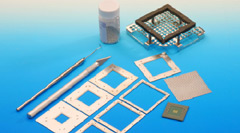
г)
Рис. 15. Установка Martin 03.1 для реболлинга с ИК-нагревом:
а) внешний вид установки; Файл Martin 03.1.jpg
б) – г) входящая в ее комплект поставки оснастка: держатель трафаретов, адептеры, трафареты, скальпель, набор шариков, крючок и пр.
Фото из [18]
Список использованных источников
Материалы компании Cooper Industries, Inc. (Торговая марка Weller)
- Набор для реболлинга Weller WPRB1000.
http://www.practicalcomponents.com/tools_supplies_training/wellerbga.htm,
http://www.practicalcomponents.com/images/wprb1000.jpg
- Weller. Operating Instructions for WPRB1000 Re-balling Kit.
http://www.howardelectronics.com/download/Manuals/WPRB%20Manual.pdf
Материалы компании Business Electronics Soldering Technologies (BEST), Inc.
- General BGA/CSP Reballing Process.
http://www.solder.net/technical/reballing.asp
- StencilQuik™ Fixturing Technique.
http://www.solder.net/technical/technique.asp
- StencilQuik™.
http://www.solder.net/stencilquik/default.asp
- Benefits of StencilQuik™.
http://www.solder.net/stencilquik/benefits.asp
- StencilQuik™ – User Instructions.
http://www.solder.net/stencilquik/User_Instructions.pdf
- EZReball.
http://www.solder.net/ezreball.asp
- Benefits of EZReball™.
http://www.solder.net/ezreball/benefits.asp
- EZReball Prelimanry Instruction Manual 10_2007.
http://www.solder.net/ezreball/EZReball%20Prelimanry%20Instruction%20Manual%2010_2007.pdf
- EZReball™ Technical Data Sheet.
http://www.solder.net/ezreball/EZReball%20Technical%20Data%20Sheet.pdf
Материалы компании Emulation Technology, Inc.
- SolderQuik™ Ball Grid Array Preforms.
http://www.emulation.com/catalog/off-the-shelf_solutions/lab&rework/bgareballing.html
- BGA REBALLING INSTRUCTIONS.
http://www.emulation.com/pdf/102003BGA_Reballing_Instruction_Manual.pdf
- BGA REBALLING – QUICK GUIDE.
http://www.emulation.com/pdf/102003BGA_Reballing_Quick_Guide.pdf
Материалы компании MARTIN GmbH.
- Reballing Tools.
http://www.martin-smt.de/en_p_r_info.php
- Rework – ABC.
http://www.martin-smt.de/pdfs/abc/rework-abc-2005.pdf
- MARTIN-Rework-Set Reball-04.5.
http://www.martin-smt.de/en_p_e_reball045.php,
http://www.martin-smt.de/pdfs/product_info/pi/reball045-en.pdf
- MARTIN Reball-03.1 – Reballing for All.
http://www.martin-smt.de/en_p_e_reball031.php,
http://www.martin-smt.de/pdfs/product_info/pi/reball031-en.pdf
- New BGA Reballer From MARTIN: The All-In-One Set Reball-03.1 For All Common Packages/Press release 1/2007.
http://www.martin-smt.de/en_n_p_0701.php
Наборы для реболлинга различных компаний
- Набор для реболлинга Practical.
http://www.practicalcomponents.com/tools_supplies_training/bga-reballing-kit.htm
- Набор для реболлинга Flextac.
http://www.practicalcomponents.com/tools_supplies_training/flextac-bga-rework-stencil-kit.htm
|