Скоро!
Событий нет.
|
 |
12 октября 2009
Установка и пайка BGA компонентов на смонтированную плату
В конструкциях современной электроники печатные платы с BGA компонентами давно получили широкое распространение благодаря очевидным конструктивным и технологическим достоинствам этого типа корпусов. В данной статье подробно рассматривается установка и пайка BGA компонентов на уже смонтированную плату, так как именно такой вариант техпроцесса вызывает, как правило, наибольшие трудности при производстве электроники и ее восстановлении и ремонте. Также рассмотрены конструкции применяющихся для этой цели трафаретов и нанесение пасты дозированием, приведены сведения по установке термопар, описаны некоторые особенности реализации операции пайки волной после установки BGA компонентов. Приводятся также не вошедшие в другие публикации портала дополнительные сведения по платам и их финишным покрытиям, пастам, флюсам и операции пайки BGA компонентов оплавлением. Тема восстановления шариковых выводов BGA компонентов обсуждалась в соответствующей статье портала ЭЛИНФОРМ «Реболлинг BGA компонентов: технология и оснастка для восстановления шариковых выводов».
Оборудование для установки, пайки и демонтажа BGA и типовая последовательность операций
Рассмотрим более подробно работу комбинированных систем, выполняющих полный комплекс задач по монтажу и демонтажу BGA компонентов. Такие специализированные системы (рис. 1), в общем случае, включают в себя держатель платы, устройство предварительного нагрева, вакуумный захват, головку пайки (последние два узла могут быть совмещены), блок программирования и, опционально, оптическую систему точного совмещения компонента и посадочного места на плате с монитором для контроля совмещения, мониторинга процесса пайки и реализации дополнительных функций.
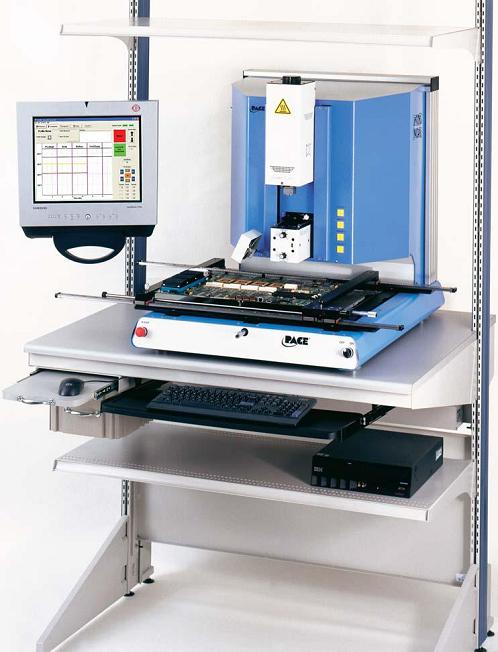
а)
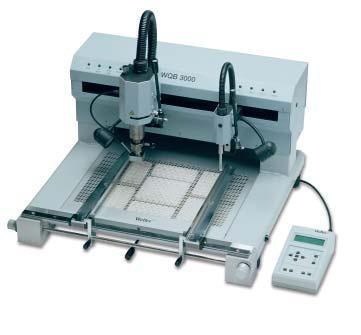
б)
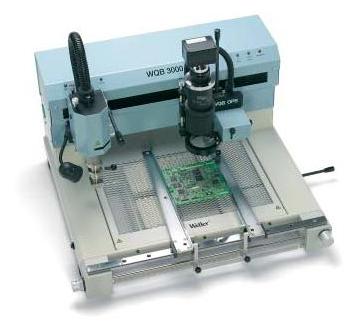
в)
Рис. 1. Примеры систем установки / демонтажа BGA компонентов: а) модель TF1700 компании PACE с оптической системой совмещения; б) модель WQB3000 компании Weller с механической системой совмещения; в) WQB3000 компании Weller с оптической системой совмещения. Источники: [10, 12]
Типовой процесс установки и пайки BGA компонента на такой системе выглядит следующим образом:
- Выбирается требуемый температурный профиль оплавления из библиотеки системы, либо производится ручная настройка/коррекция параметров. Плата устанавливается в специальный держатель и фиксируется в нем. В случае отработки или необходимости мониторинга термопрофиля производится установка одной или нескольких термопар.
- Перед установкой компонента осуществляется нижний подогрев платы с помощью, как правило, ИК-нагревателя. Существуют системы с двухзонным нагревом: меньшая мощность для небольшой по площади зоны нагрева и бо́льшая – для более крупной. В ряде систем применяется конвективный предварительный нагрев.
- В адаптер головки устанавливается требуемое сопло, и производится захват BGA компонента из технологической упаковки. В комплект поставки установок монтажа и пайки BGA входят сопла под различные типоразмеры компонентов. Пример сопел приведен на рис. 2. Существуют системы, где захват компонента происходит из специального регулируемого гнезда, куда компонент помещается перед захватом.
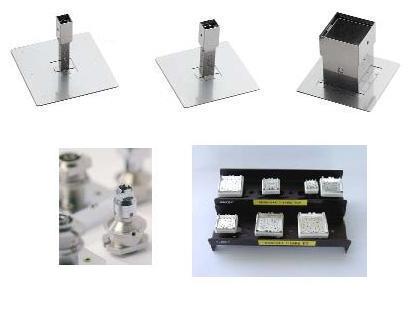
Рис. 2. Сопла для работы с BGA компонентами. Источники: [10, 12, 15]
- Далее компонент, если это необходимо, перемещается в позицию нанесения клейкого флюса или пасты методом погружения в поддон с ~300 мкм слоем наносимого материала (рис. 3).
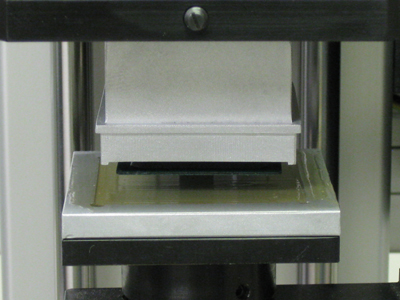
Рис. 3. Погружение захваченного BGA компонента в поддон с клейким флюсом. Источник: [14]
- Затем производится точное совмещение шариковых выводов BGA компонента и контактных площадок платы. Для этого между захваченным компонентом и посадочным местом на плате размещается блок оптики с разделением изображения (рис. 4) и дихроической призмой. В результате на экране монитора оператору показываются два увеличенных изображения в различных цветах: контактные площадки платы и выводы BGA компонента (рис. 5). Применяется бестеневая подсветка с помощью галогенных ламп или светодиодов. Оператору, пользуясь микрометрическими винтами точного перемещения платы по осям X и Y, необходимо добиться визуального наложения двух изображений до их полного совмещения. После завершения процесса совмещения блок оптики отводится в сторону.
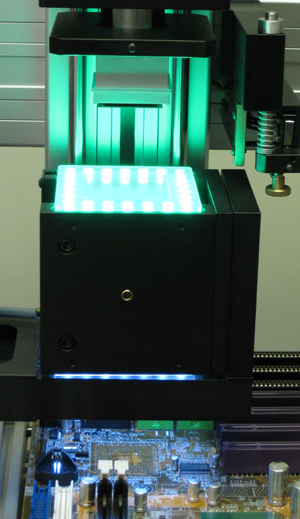
Рис. 4. Блок оптики с разделением изображения между захваченным компонентом и посадочным местом на плате. Источник: [14]
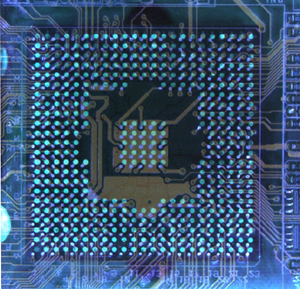
а)
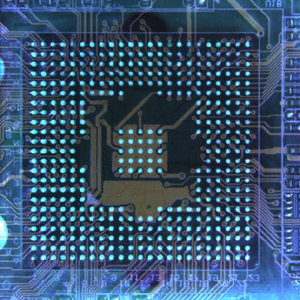
б)
Рис. 5. Совмещение шариковых выводов захваченного компонента и посадочного места на плате с помощью оптической системы с наложением изображений: а) рассовмещенное состояние; б) совмещенное состояние. Источник: [14]
Возможен и другой вариант совмещения (рис. 6) – до захвата компонента изображение посадочного места на плате совмещается на экране монитора с позиционирующей рамкой компонента, выбранного из базы данных системы, при помощи перемещения держателя платы по осям X, Y. Затем компонент захватывается, и его изображение также совмещается по осям X, Y и углу θ с рамкой его корпуса, генерируемой системой на экране монитора.
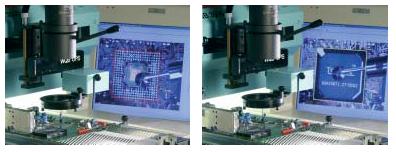
Рис. 6. Совмещение по границе корпуса BGA компонента с помощью оптической системы с позиционирующей рамкой. Источник: [10]
Также существует вариант совмещения со специальными шаблонами без использования камеры (рис. 7). В этом случае на плате размещается специальный шаблон, точно совмещается с посадочным местом компонента на плате и фиксируется на ней. Затем в него вручную устанавливается компонент, который с помощью своих шариковых выводов точно центрируется в шаблоне. Затем вакуумный захват поднимает компонент с шаблона, после чего он может быть убран с поверхности платы.
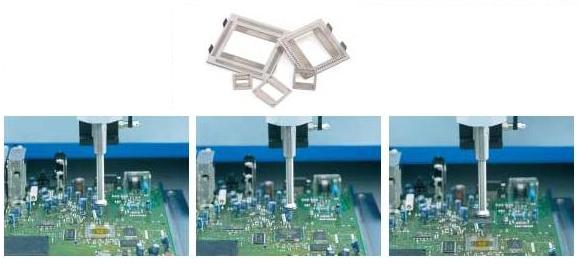
Рис. 7. Совмещение по специальному шаблону без применения оптической системы. Источник: [10]
- С помощью прецизионного привода перемещения по оси Z, компонент устанавливается на плату с контролируемым усилием, которое в большинстве систем настраивается и может быть сведено практически к нулевому. Если компонент устанавливается с помощью сопла с совмещенным вакуумным захватом, то сразу начинается процесс пайки, возможен также вариант, когда вакуумный захват снимается, и опускается сопло конвективной пайки.
- Начинается процесс пайки по заданному термопрофилю. Пайка производится, как правило, с помощью принудительной конвекции во внутреннем объеме сопла, закрывающего установленный компонент. Схема потока газа в сопле приведена на рис. 8. Обеспечивается управление скоростью потока нагретого газа и контроль температуры с замкнутой обратной связью. Пайка проводится в воздушной или инертной азотной среде. После окончания фазы охлаждения сопло снимается с компонента, и процесс завершается.
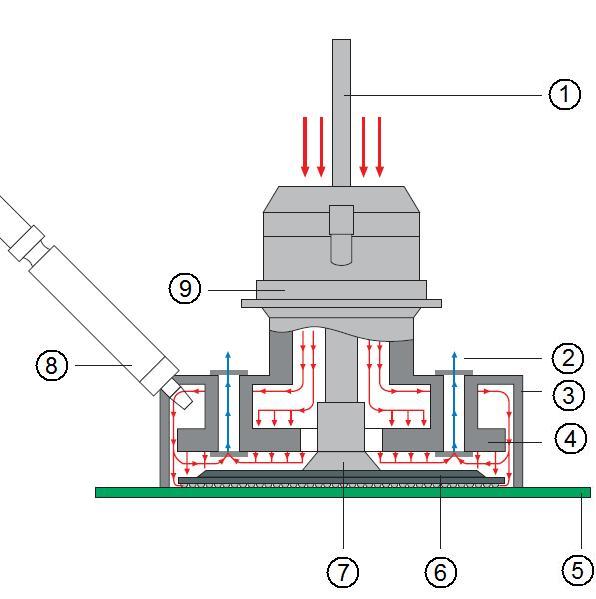
Рис. 8. Пайка BGA компонента. Схема потока газа в сопле. На рисунке обозначены: 1 – «вакуумный лифт» для поднятия компонента после окончания процесса демонтажа; 2 – канал для выхода воздуха из сопла; 3 – корпус сопла; 4 – отражательная пластина для равномерного распределения газа внутри сопла; 5 – печатная плата; 6 – BGA-компонент; 7 – вакуумный захват для демонтажа компонента; 8 – датчик температуры; 9 – кольцо установки сменных сопел в адаптер. Источник: [10]
Предварительный демонтаж компонента, в случае необходимости, осуществляется сходным образом, с применением такого же термопрофиля, как и при пайке.
Флюсование / Нанесение паяльной пасты
Флюс необходим для удаления окислов при пайке не только с поверхности контактной площадки, но и с поверхности шарикового вывода, где они могли образоваться вследствие проведения сушки в неинертной атмосфере, термотренировки либо длительного хранения BGA корпусов.
Флюсование без применения паяльной пасты имеет ряд недостатков – в частности, объем припоя в паяном соединении будет несколько меньше, чем при установке на пасту. Результатом этого станет меньший зазор между корпусом и платой (обычно на 1 – 2 mil = 25 – 50 мкм), вследствие чего может несколько снизиться надежность при термоциклировании, особенно если шариковые выводы расположены под областью кристалла, как это имеет место у корпусов с полной матрицей выводов. Также по причине меньшего объема припоя уменьшается эффект самоцентрирования корпуса. Может быть затруднено формирование правильной по форме галтели, если шариковый вывод имеет форму, отличающуюся от нормальной, либо наличествуют мелкие дефекты контактной площадки [4]. Применение пасты может уменьшить колебания высот шариковых выводов, обеспечить улучшенную смачиваемость за счет увеличения площади тесного контакта между шариком и пастой, а также обеспечить лучшие клейкие свойства, чем только флюс. Также наличие пасты поможет предотвратить потерю объема припоя в соединении в случае выполнения переходных микроотверстий в центре контактной площадки BGA компонента. При нанесении пасты рекомендуется использовать металлические ракели либо ракели, изготовленные из полимеров с высоким показателем твердости, чтобы обеспечить равномерность отпечатков и хорошее отделение пасты от трафарета при снятии, в особенности при уменьшении шага выводов [5].
Тем не менее, ряд производителей утверждает, что, так как шариковый вывод состоит из эвтектического либо близкого к эвтектическому сплава, он полностью оплавляется в процессе пайки, и добавление дополнительного объема к нему за счет относительно небольшого количества пасты на контактных площадках не является обязательным. Шарики диаметром 30 mil (~0,76 мм) обеспечивают, по данным [8], зазор между платой и корпусом в среднем от 16 до 24 mil (~ 0,41 – 0,61 мм) в зависимости от типоразмера корпуса и конструкции контактной площадки. Этого, по мнению [8], достаточно, чтобы осадка корпуса гарантировала отсутствие нарушений контакта в соединениях вследствие деформации платы при повышенных температурах. По этим же данным, добавление паяльной пасты в количестве 14% объема шарикового вывода в общем случае вызовет увеличение зазора на 1 – 2 mil (25 – 50 мкм).
Однако нанесение чрезмерно большого объема паяльной пасты при использовании более толстых трафаретов и/или апертур большего диаметра потенциально могут привести к образованию пустот в паяном соединении, особенно в сочетании с высокими скоростями подъема температуры в профиле оплавления и применением быстро испаряющихся флюсов. Пустоты образуются в процессе испарения флюса и задержки летучих веществ в объеме паяного соединения. Они формируются в нижней части соединения, у платы, но благодаря эффекту плавучести перемещаются в область соединения вывода с корпусом компонента.
Для нанесения пасты при ремонте сборки или установке отдельных BGA компонентов, когда уже смонтированные на плате компоненты делают невозможным применение полноразмерного металлического трафарета, применяют три основных вида трафаретов – традиционные металлические, гибкие полимерные и полиимидные несъемные.
Помимо нанесения пасты трафаретной печатью, применяется нанесение пастообразного флюса и пасты с помощью переноса на игле, окунания и точечного дозирования [8].
Дозирование паяльных паст
Дозирование, в свою очередь, может выполняться ручным или автоматизированным методами. Ручной метод характеризуется чрезмерно большим временем цикла и большими неточностями как с точки зрения координат нанесения доз, так и их объема. Одним из недостатков метода дозирования является возможность нанесения им паст с относительно низким (до 87%) содержанием металла, в противном случае наконечник дозатора будет часто закупориваться. Такие пасты более склонны к растеканию и расслоению. Время цикла здесь определяется скоростью работы дозатора и для BGA компонентов с большим числом выводов может достигать нескольких минут на компонент с учетом времени наладки. Перед началом работы с пастой для дозирования ее рекомендуется выдержать при рабочей температуре в течение 2-3 часов. Перед установкой на картридж с пастой дозирующего наконечника рекомендуется выдавить вручную валик пасты длиной 2-3 см; это предотвратит возможную закупорку. Идеальной температурой для дозирования является 28°С. Более низкие температуры ведут к образованию «тяжей», высокие – к закупорке и расслоению на припойную и флюсовую составляющие. Следует использовать подогрев дозирующего наконечника при наличии такой опции в системе дозирования [16] .
Диаметр наконечника определяется наименьшим размером требуемой дозы наносимого материала. Это, в свою очередь, определяет максимальный размер частиц используемой пасты. Согласно [16] для его определения следует разделить диаметр наконечника на 7. Например, в случае диаметра наконечника, равного 0,2 мм, это соответствует размеру частицы пасты, равному 0,2 : 7 = 0,028 мм = 28 мкм, поэтому в данном случае следует использовать пасту с размером частиц 10 – 25 мкм. Следует помнить, что большие размеры доз в сочетании с маленькими диаметрами наконечника приведут к неоправданному завышению времени дозирования.
Трафареты для монтажа BGA
Металлические трафареты
При ручном нанесении пасты для установки BGA через металлический ремонтный трафарет (рис. 9), он должен быть точно совмещен с контактными площадками платы, затем жестко зафиксирован каким-либо образом, чтобы не допустить его смещения в процессе нанесения пасты и обеспечить плотное прилегание к поверхности платы, после чего с помощью ракеля наносится паста, и трафарет снимается с платы.
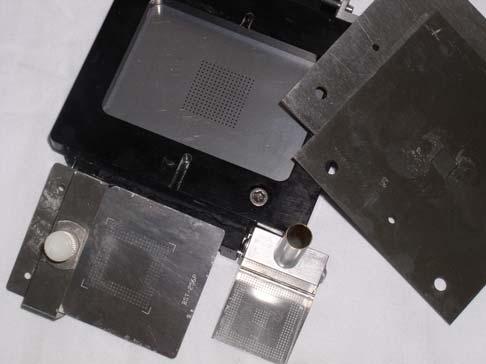
Рис. 9. Металлические трафареты. Источник: [7]
Большое значение в данном случае имеет опыт и квалификация оператора, так как обеспечение точного совмещения и плотного прилегания трафарета, подержания равномерной скорости движения и требуемого давления ракеля, а также аккуратное снятие трафарета с платы в этом случае полностью возлагается на него. Существуют механизированные приспособления с многозвенным манипулятором, предназначенные для крепления трафарета и нанесения пасты (рис. 10). Такая оснастка включает в себя устройство натяжения минитрафарета и микролифт для точного отделения его от платы после нанесения пасты.
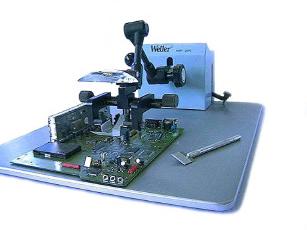
Рис. 10. Оснастка для крепления трафарета и нанесения паяльной пасты. Источник: [11]
В случае, когда размещение трафарета на плате невозможно из-за особенностей ее конструкции и компоновки, возможно нанесение пасты непосредственно на шариковые выводы BGA компонента через металлический трафарет. Пример оснастки для такого нанесения пасты представлен на рис. 11.
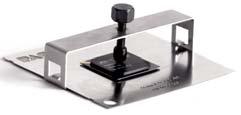
Рис. 11. Оснастка для нанесения паяльной пасты непосредственно на шариковые выводы BGA через металлический трафарет. Источник: [12]
При изготовлении трафаретов для BGA и microBGA компонентов рекомендуется применять электрополировку [20], обеспечивающую получение гладкой поверхности, сходной по характеристикам с поверхностью трафаретов, выполняемых методом гальванопластики. Такой трафарет лучше пропускает пасту через апертуры, легче моется, на нем отсутствует нагар, остающийся после лазерной резки при изготовлении трафарета.
Отметим, что для шариковых выводов диаметром ≤0,5 мм многими компаниями рекомендуется использовать квадратную форму апертур со скругленными углами и 5° уклоном стенок. Для компенсации рассовмещения трафарета и контактных площадок платы и последующего образования перемычек допускается уменьшение апертур на 25-50 мкм для BGA компонентов с малым шагом выводов (≤1,0 мм). Толщина трафарета находится обычно в пределах от 100 до 200 мкм, а твердость используемого ракеля должна быть не менее 95. Соотношение размеров трафарета, по данным [4, 5], должно составлять не менее 3:1. Например, для размеров стороны КП 0,024 дюйма (~0,61 мм) и диаметра шариковых выводов 0,030 дюйма (~0,76 мм) следует применять трафарет толщиной 150 мкм с размером апертуры 0,028 дюйма (~0,71 мм). (шаг 1 мм – апертура 0,5 мм при толщине 0,15 мм).
Пленочные трафареты
Существенным преимуществом съемных и несъемных пленочных трафаретов является возможность подрезки в случае, когда их размещению мешают конструктивные элементы сборки, что невозможно для металлических трафаретов. Однако вручную точное совмещение проще выполнять, напротив, с металлическими трафаретами, хотя и любой трафарет с обратной клеевой стороной позволяет переклеить его в случае неудачного размещения.
Съемные полимерные трафареты. Одним из распространенных вариантов нанесения паяльной пасты на контактные площадки под BGA компонент в случае ремонта сборки является использование одноразовых полимерных гибких трафаретов с клейкой нижней поверхностью (рис. 12) [17]. Трафареты изготавливаются с помощью лазера из антистатической полимерной пленки с клейким покрытием обратной стороны, не оставляющим загрязнений на поверхности платы. Выпускаются трафареты под различные корпуса, количество, шаг, размер и расположение шариковых выводов.
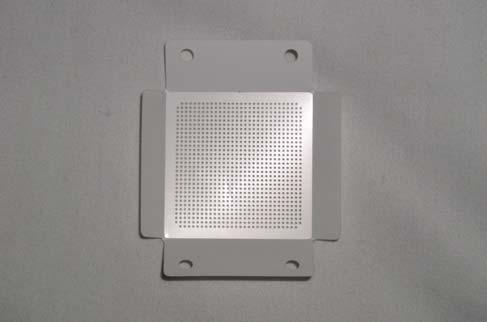
Рис. 12. Съемный полимерный трафарет. Источник: [7]
Так как трафареты являются самоклеющимися, отсутствует надобность в фиксирующей пленке или ленте. Клеевое уплотнение вокруг каждой контактной площадки BGA препятствует затеканию пасты под трафарет при ее нанесении. В противоположность металлическим трафаретам, при наличии локальных искривлений платы гибкий клеящийся трафарет будет плотно прилегать к ее поверхности, повторяя форму изгиба. Наличие отогнутых бортиков по четырем сторонам трафарета препятствует возможному загрязнению поверхности платы паяльной пастой при ее избыточном нанесении или неосторожном перемещении ракеля. Такой трафарет является одноразовым и, таким образом, не требует очистки. Если существует необходимость в его повторном использовании, то оно, как правило, допускается производителем, при этом следует учитывать, что очистка с помощью растворителя любого типа вызовет потерю части клеящего слоя. Также допускается более низкая квалификация оператора, чем при работе с металлическими трафаретами. Внешний вид и состав ремонтного набора приведен на рис. 13.
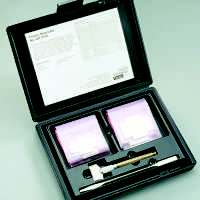
а)
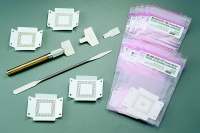
б)
Рис. 13. Внешний вид и состав ремонтного набора Flextac BGA Rework Stencil Kit
а) внешний вид набора, упакованного в антистатический кейс
б) состав набора: 20 различных гибких трафаретов, ракель для нанесения пасты с лезвиями трех видов. Источник: [17]
Процедура применения такого трафарета заключается в следующем (рис. 14) [17]:
- Выбрать необходимый типоразмер трафарета и отогнуть предварительно отформованные бортики.
- Снять защитную пленку с нижней поверхности трафарета, открыв клейкий слой.
- Точно установить трафарет на плату, держа его за бортики. При неправильной установке трафарет допускает повторное позиционирование.
- Нанести паяльную пасту, используя подходящее лезвие ракеля из набора. Так как вокруг каждой контактной площадки есть клеевое уплотнение, для окончательного заполнения апертур можно использовать столько проходов ракеля, сколько необходимо, не опасаясь выдавливания пасты за пределы площадок с нижней стороны трафарета.
- Снять трафарет выбросить или отложить для повторного использования.
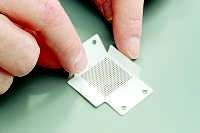

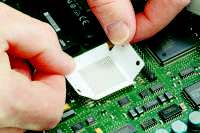
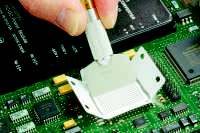
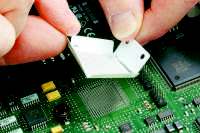
Рис. 14. Последовательность операций по нанесению паяльной пасты на контактные площадки платы под BGA компонент с помощью ремонтного набора Flextac. Источник: [17]
Несъемные полиимидные трафареты. Другим вариантом ручной установки BGA-компонентов являются специализированные ремонтные трафареты StencilQuick™ [18], которые являются одноразовыми и несъемными, т.е. после нанесения пасты, установки компонента на плату и пайки оплавлением становятся неотъемлемой частью сборки (рис. 15).
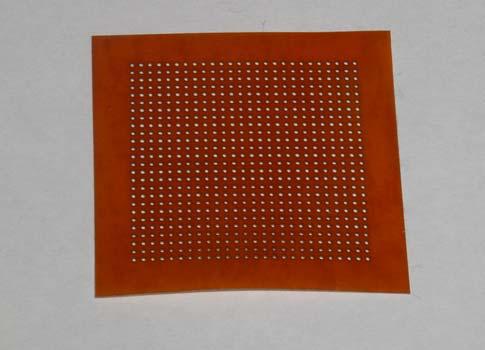
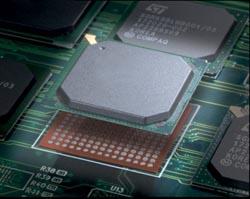
Рис. 15. Несъемный полиимидный трафарет и его применение. Источники: [7, 18]
Такие трафареты способны избавить от проблем, связанных со смазыванием нанесенной матрицы доз паяльной пасты или флюса (рис. 16) и неполным отделением пасты от апертур трафарета, а также устраняют необходимость в трудоемкой и отнимающей много времени отмывке минитрафаретов. По данным [18], с применением трафаретов StencilQuick™ возможно сэкономить более 50% времени, затрачиваемого на замену BGA компонента. В силу конструктивных особенностей эти трафареты поддерживают минимальный зазор между корпусом BGA компонента и платой, равный своей толщине, и препятствуют тем самым чрезмерной осадке корпуса, а также образованию перемычек между контактными площадками при оплавлении. При нанесении пастообразного флюса такие трафареты позволяют удерживать его непосредственно в области контактных площадок, что позволяет использовать флюс с более высокой степенью активности, не опасаясь его негативного воздействия на прочие области платы и появления на них остатков.
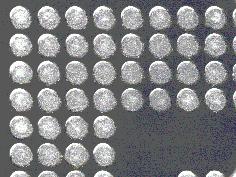
Рис. 16. Смазанная матрица доз паяльной пасты вследствие неаккуратного снятия трафарета с платы. Источник: [7]
Ремонтные трафареты StencilQuick™ изготавливаются с помощью лазерной резки из антистатической полиимидной пленки с покрытием обратной стороны клеем, устойчивым к действию высоких температур, и наложением съемной покровной пленки/бумаги.
Апертуры трафарета соответствуют контактным площадкам на ПП и определяют те области на ней, куда должна быть нанесена паяльная паста или пастообразный флюс. Как утверждает компания-разработчик, после нанесения пасты BGA компонент может устанавливаться на плату с таким трафаретом вручную без применения специального оборудования с системой технического зрения, достаточно лишь приобрести определенный навык.
Последовательность операций при работе с такими трафаретами следующая (рис. 17) [19]:
- снять дефектный компонент;
- удалить остатки припоя с посадочного места на плате под установку нового компонента с помощью плетенки или инструмента для отсоса припоя;
- очистить поверхность платы;
- удалить покровную пленку с обратной части трафарета StencilQuick;
- осуществить совмещение трафарета с контактными площадками платы вручную, ориентируясь на диагонально расположенные площадки и не прилагая давления к трафарету; убедиться, что площадки располагаются по центру апертур;
- прижать трафарет к плате для активации клея; перед прижатием убедиться в точном совмещении контактных площадок и апертур трафарета;
- наклеить каптоновую ленту по периметру посадочного места с перекрытием внешнего контура трафарета;
- нанести паяльную пасту ракелем, аккуратно заполнив все апертуры трафарета;
- удалить маскирующую пленку, которая была нанесена по периферии трафарета;
- стереть избыточно нанесенную пасту с верхней части трафарета StencilQuick с помощью безворсового материала;
- осторожно разместить правильно подготовленный компонент, совместив выводы или шарики с заполненными пастой апертурами; приобретя минимальный опыт, оператор научится «ощущать» момент попадания шариковых выводов в апертуры несъемного трафарета (рис. 18);
- произвести пайку оплавлением.
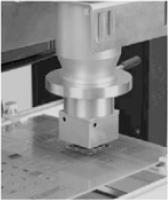
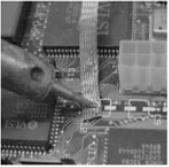
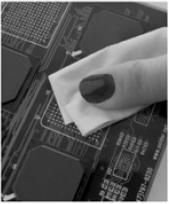
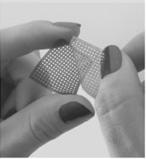
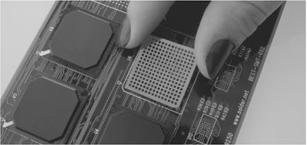
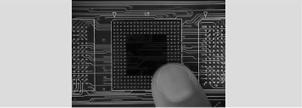
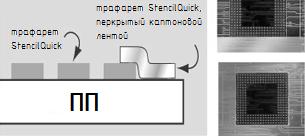
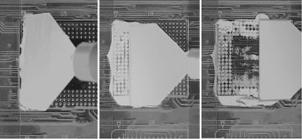
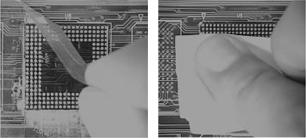

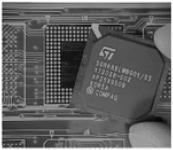
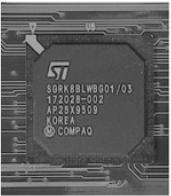
Рис. 17. Последовательность операций при установке BGA компонента с помощью ремонтного трафарета StencilQuick. Источник: [19]
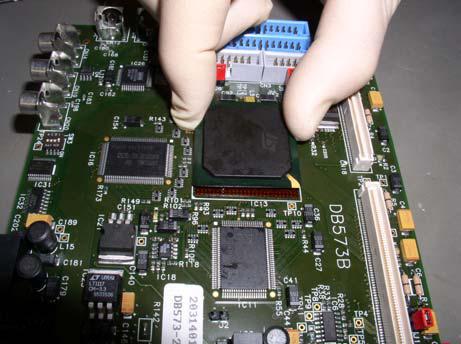
Рис. 18. Оператор устанавливает BGA компонент вручную на несъемный трафарет, «ощущая» момент попадания шариковых выводов в апертуры. Источник: [7]
Финишное покрытие платы
Для достижения хороших результатов пайки BGA компонентов важно использовать покрытие контактной площадки, обеспечивающее хорошую плоскостность и паяемость. Среди наиболее широко применяющихся покрытий такими свойствами обладают органическое покрытие (OSP) и химический никель/иммерсионное золото (ENIG).
Для золота существуют разнообразные методы нанесения покрытия: химического восстановления или электролитические, однако только ENIG-процесс является самоограничивающимся. Толщина электроосажденного золота может на порядок превосходить толщину покрытия, полученного с помощью ENIG-процесса. Для предотвращения охрупчивания паяного соединения вследствие избыточного весового содержания золота рекомендуется применять только ENIG-процесс.
Ряд компаний, в частности, [6], не рекомендуют использовать стандартное покрытие припоем с выравниванием воздушным ножом (HASL), так как применяемые припои 63Sn/37Pb или 60Sn/40Pb могут обеспечить хорошую паяемость, но плоскостность и контроль толщины покрытия при этом гораздо хуже, чем у OSP- и ENIG-покрытий. В целом, негативные моменты, связанные с применением покрытия HASL, включают в себя относительно плохую плоскостность и непредсказуемую толщину покрытия, а также бо́льшую деформацию и коробление платы.
Тем не менее, некоторые производители, в частности, [5], отмечают, что высокий уровень механических напряжений и приложенных усилий могут привести к разрушению паяных соединений на ENIG-покрытии. При этом даются рекомендации избегать ударов и чрезмерного изгиба печатных плат с такими соединениями в процессе обращения с этими платами, а также при их сборке и тестировании. Примерами приложения серьезных механических нагрузок к плате могут служить: внутрисхемное тестирование, ручная вставка разъемов, разделение групповых заготовок, двусторонняя сборка и ручные сборочные операции. Также в [5] отмечено, что важным фактором надежности паяных соединений на ENIG-покрытии является толщина печатной платы, и приемлемой считается толщина, равная 0,093 дюйма (~2,4 мм). Печатные платы с меньшей толщиной следует применять после оценки результатов сборочного процесса и тестирования изделия заказчиком или контрактным производителем. С другой стороны, печатные платы с толщиной, превышающей указанную, могут иметь пониженную надежность при долговременных циклических температурных нагрузках.
Копланарность
Максимально допустимое отклонение от копланарности выводов, согласно стандарту JEDEC, составляет 0,15 мм независимо от размера корпуса и количества выводов. Копланарность определяется в стандарте как максимальное расстояние между самым выступающим шариковым выводом и посадочной плоскостью, которая определяется тремя выводами, на которые опирается корпус в случае его посадки на идеальную плоскость. Любые отклонения от копланарности являются следствием двух факторов: короблением подложки/платы и различием расстояний между поверхностью КП и шариковыми выводами корпуса. Первый фактор вносит наибольший вклад в отсутствие копланарности, в то время как высота шариковых выводов обычно относительно равномерна. При комнатной температуре обычный PBGA корпус имеет изгиб, направленный вверх, так что корпус размером 27 х 27 мм с 225 выводами, в наихудшем случае имеет некопланарность выводов на уровне около 4 mil (~0,1 мм) [8].
Установка BGA компонента на пасту
В принципе, для установки и пайки BGA компонентов могут применяться все основные виды флюсов:
- среднеактивированные канифольные (RMA);
- водосмываемые на основе органических кислот (OA);
- не требующие отмывки (no-clean).
Ниже в таблице 1 приведены основные достоинства и недостатки этих флюсов по данным [5].
Таблица 1. Основные достоинства и недостатки флюсов RMA, OA и no-clean [5]
Тип флюса |
Достоинства |
Недостатки |
RMA |
Стабильность химического состава.
Хороший свойства при пайке. |
Необходимость в растворителе или омыляющем реагенте для отмывки. |
OA |
Отмывка водой.
Очень легко отмывается. |
Чувствительны к влажности: малый срок годности при хранении и время жизни в ванне для отмывки.
Тенденция к образованию шариков припоя.
Вода вымывает свинец в отработанный раствор. |
no-clean |
Нет необходимости в техпроцессе, оборудовании и материалах для отмывки.
Нет проблем с утилизацией или рециркуляцией стоков. |
Может оставаться видимый налет. |
Обычно при установке BGA используют пасту с флюсом, не требующим отмывки либо водосмываемым, на основе эвтектического сплава 63Pb/37Sn (температура ликвидуса 183°С) либо близкого к эвтектике с добавлением серебра – 63Sn/36Pb/2Ag (179°С), что обеспечивает более высокую усталостную прочность и бо́льшую однородность структуры паяных соединений. Большинство производителей компонентов предлагают в спецификациях типовой профиль оплавления для пайки своих компонентов.
Как правило, BGA компоненты не требуют специальных паст для пайки оплавлением. Тем не менее, многие производители паяльных материалов разрабатывают специальные пасты с низким уровнем образования пустот, которые также могут применяться и при пайке компонентов, отличных от BGA.
В [4] рекомендуется, чтобы промежуток времени между нанесением пасты трафаретной печатью и оплавлением составлял не более 45 мин. (оптимально – 30 мин.), чтобы избежать высыхания пасты и сопутствующих проблем с паяемостью, а также появления пустот в паяных соединениях. Допустимые времена воздействия воздуха на пасту, публикуемые некоторыми производителями, относятся к 500-граммовым банкам, а не маленьким дозам пасты на плате, которые высыхают значительно быстрее [4].
Важное значение имеет инспекция качества нанесения пасты на плату. Для BGA компонентов с шагом выводов ≤1 мм [6] настоятельно рекомендует проводить 100% 3D-инспекцию после нанесения пасты, при шаге выводов 1,25 мм рекомендуется осуществлять выборочную 3D-инспекцию.
Если установка компонентов производится на автоматизированном оборудовании, то благодаря тому, что поле допуска на расположение матрицы шариковых выводов от граней корпуса достаточно мало (≤75 мкм) по сравнению с величиной шага выводов, установка может производиться по контуру корпуса подобно установке чип-компонентов. Современные системы центрирования на основе лазеров или камеры нижнего обзора осуществляют центрирование непосредственно по матрице выводов и могут во многих случаях распознавать отсутствие шариков в матрице, а в некоторых случаях и определять копланарность выводов в режиме реального времени. Иногда для установки используется распознавание только внешних рядов шариковых выводов.
Для обеспечения хода установочной головки необходимо предусмотреть вокруг BGA компонента запрещенную зону радиусом по крайней мере 200 mil (51 мм). Необходимо убедиться в том, что разработчик схемы не использует это пространство для размещения каких-либо критичных компонентов, например, развязывающих конденсаторов [21].
Автоматизированное оборудование требует наличия по крайней мере двух, а предпочтительно – трех реперных знаков, предпочтительно круглой формы с диаметром 1,6 мм. Наиболее распространенное расположение реперных знаков – ортогональное в виде буквы L для оптимизации применения алгоритмов компенсации ошибок растяжения/сжатия. Если это возможно, левый нижний реперный знак должен иметь координаты 0,0 (начало координат платы). Для больших плат или панелей следует добавлять четвертый реперный знак [5].
Пайка BGA компонентов
Все типовые рекомендации по пайке обычных SMD компонентов могут быть применены и для BGA компонентов. Если на плате присутствуют несколько PBGA-компонентов, то параметры профиля оплавления необходимо проверять в различных местах их установки, так как температурные условия в них могут отличаться вследствие различного окружения другими компонентами, различной плотности расположения этих компонентов, а также различных координат установки. В случае необходимости проведения пайки прочих компонентов волной припоя, следует жестко контролировать температурный профиль этого процесса, так как перегрев волны может привести к короблению платы и разрушению паяных соединений BGA компонента [4].
Так как компоненты PBGA имеют небольшую массу, в ряде случаев их снятие и монтаж могут производиться с применением локального нагрева только сверху, преимущественно при помощи принудительной конвекции. Если масса корпуса компонента относительно велика, либо плата имеет большую толщину и большие внутренние области металлизации, следует применять предварительный нагрев сборки снизу до 80°C – 145°C, если это позволяют установленные на ней компоненты [8]. Это также помогает предотвратить появление проблем с короблением платы. Чтобы избежать дополнительного цикла нагрева, следует сразу же удалять остатки припоя с посадочного места компонента, пока плата еще горячая. Рекомендуется применять вакуумный отсос припоя, так как использование плетенки связано с дополнительным нагревом, давлением и более значительными затратами времени. Большое значение имеет опыт и навык оператора, производящего работу по снятию/монтажу компонента.
С уменьшением толщины плат может возникнуть проблема, связанная с короблением платы в процессе пайки. Это может вызвать появление открытых паяных соединений, соединений в виде «песочных часов» или неоднородности в распределении припоя. Помочь справиться с ней может правильная поддержка платы в печи или, в самом худшем случае, использование дополнительного груза для придания жесткости плате. В целом, меньший размер CSP компонентов создает меньше проблем при пайке по сравнению со стандартными BGA компонентами, которые, в свою очередь, испытывают проблемы такого рода реже, чем выводные компоненты [5]. Примеры профилей оплавления см. в таблице 2.
Таблица 2. Пример параметров рекомендуемого температурного профиля для пайки оплавлением BGA-компонентов [4, 5]
Зоны |
Характеристика протекающих процессов |
Окно параметров/Ограничения |
[4] |
[5] |
Предварительный нагрев |
Начальный нагрев выводов/компонента
Пиковая температура |
1–3 °C/с
100–140 °C |
1,5–3 °C/с
120–140 °C |
Выдержка |
Удаление растворителей и активация пасты
Время выдержки |
120 –170 °C
120 с |
120 –170 °C
60 – 180 с |
Оплавление |
Время нахождения при температуре больше 183°С
Максимальная температура корпуса компонента |
45 – 120 с
205 – 225 °C
220 °C макс. |
60 – 90 с
220±5 °C макс. |
Охлаждение |
Скорость охлаждения |
2 –3 °C/c |
2 –3 °C/c |
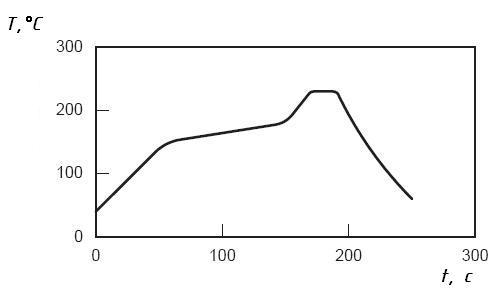
Рис. 19. Рекомендуемый профиль оплавления для пайки BGA компонентов с применением эвтектического сплава SnPb. Источник: [5]
Некоторые производители среди общих рекомендаций называют использование принудительной конвекции с обеспечиваемым градиентом температур по поверхности плат в пределах ±5°С и менее, защитной азотной атмосферы с содержанием частиц O2 менее 100 ppm и пиковой температуры 215 – 220°С для сплавов 63Sn/37Pb или 63Sn/36Pb/2Ag. При этом для пластиковых корпусов выдержка при максимальной температуре должна быть кратковременной и составлять 10 – 20 с [6].
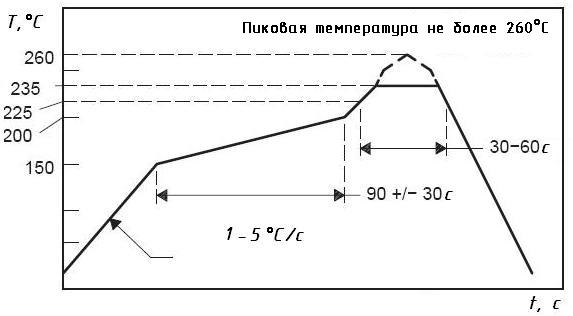
Рис. 20. Рекомендуемый профиль оплавления для пайки BGA компонентов с применением бессвинцового сплава SnAgCu. Источник: [5]
При выполнении последующей пайки волной рекомендуется избегать повторного оплавления паяных соединений BGA компонентов. Компоненты PBGA обладают малой теплоемкостью и быстро нагреваются, ситуацию усугубляют многочисленные сквозные металлизированные отверстия под проекцией корпуса (рис. 21). При нагреве только снизу может произойти коробление PBGA компонента. Эти и другие причины могут привести к образованию открытых паяных соединений (рис. 22).
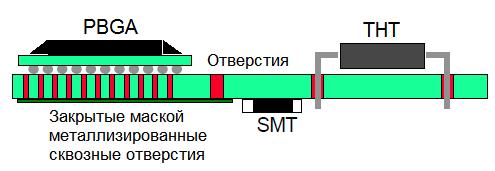
Рис. 21. Схематичное изображение с установленными BGA , прочими SMD и THT компонентами. Источник: [9]
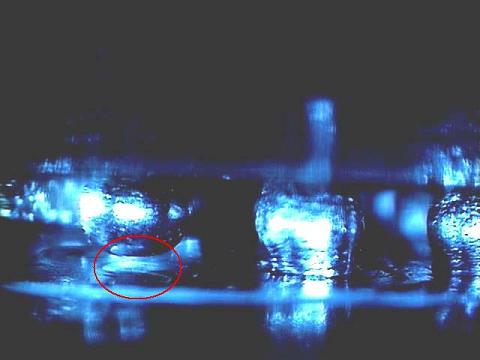
Рис. 22. Открытое паяное соединение BGA компонента. Источник: [7]
Вследствие этого рекомендуется [9]:
- оптимизировать операцию пайки волной с тем, чтобы компонентам BGA передавалось минимальное количество теплоты;
- блокировать подачу припоя к BGA компонентам, применяя специальную паллету для пайки волной;
- блокировать передачу теплоты к BGA компонентам, покрывая нижнюю часть платы со сквозными металлизированными отверстиями паяльной маской (следует отметить, что это нежелательно с точки зрения последующего тестирования, если в этом месте располагаются контрольные точки);
- использовать корпуса с расположением рядов выводов по периметру корпуса и не имеющих отверстий, расположенных ближе 5 мм к контактным площадкам шариковых выводов;
- наносить на область BGA компонента каптоновую ленту (нежелательная ручная операция);
- перепроектировать плату с целью применения только поверхностно монтируемых компонентов;
- использовать другие методы пайки THT компонентов, в частности, селективную пайку.
Расположение термопар при термопрофилировании
Термопары для термопрофилирования должны располагаться под корпусом BGA компонента и предпочтительно внутри паяного соединения. Рекомендуется использовать тонкий провод калибра 30 – 36, который в большинстве случаев позволит произвести пайку компонента в обычном режиме с минимальным числом шариковых выводов со смещением либо отсутствием контакта с платой [9]. При подготовке платы для термопрофилирования рекомендуется выполнить паяное соединение наконечника термопары с шариком, предпочтительно центральным в матрице выводов, так как он испытывает минимальную пиковую температуру при пайке и поэтому находится в самых худших условиях. Полезно также прикрепить термопару к шарику во внешнем ряде выводов, как испытывающему максимальную тепловую нагрузку. Затем компонент помещается на предварительно профлюсованное посадочное место на плате, закрепляется с помощью каптоновой ленты и подвергается оплавлению.
Альтернативным методом более надежного крепления термопары является удаление с помощью плетенки центрального шарика и последующее крепление наконечника термопары высокотемпературным припоем или теплопроводящим эпоксидным компаундом. Также для крепления термопары, в особенности для керамических (CBGA) компонентов, успешно может применяться сверление компонента сверху или платы снизу. В этом случае последовательность действий следующая (рис. 23):
- плата сверлится через контактную площадку в центре посадочного места под компонент, устанавливаются прочие компоненты, и производится их оплавление обычным способом,
- используя то же самое сверло, производится сверление шарикового вывода на глубину около 0,5 мм,
- термопара крепится в центре вывода с использованием небольшого количества теплопроводящего эпоксидного компаунда.
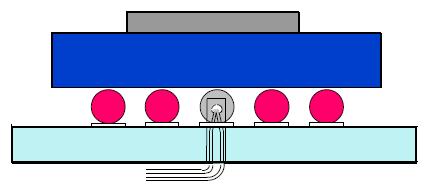
Рис. 23. Крепление термопары через просверленное отверстие в плате и шариковый вывод CBGA компонента. Источник: [9]
Иногда удовлетворительные результаты обеспечивает вставка наконечника термопары с предварительно нанесенной термопастой под корпус уже установленного на плату компонента [9].
Заключение
Конечно, в рамках небольшой статьи не представляется возможным осветить все аспекты, связанные с BGA компонентами. За рамками рассмотрения остались такие вопросы, как конструирование плат под BGA компоненты, работа по бессвинцовой и смешанной технологии, нанесение материалов под корпус, контроль и отмывка. В дальнейших статьях цикла, освещающего вопросы работы с BGA компонентами, портал ЭЛИНФОРМ планирует обязательно вернуться к их обсуждению.
Список использованных источников
- Нинг-Ченг-Ли. Технология пайки оплавлением, поиск и устранение дефектов: поверхностный монтаж, BGA, CSP и flip chip технологии. – М.: Издательский Дом «Технологии», 2006.
- Майкл Джюд, Кейт Бриндли. Пайка при сборке электронных модулей. – М.: Издательский Дом «Технологии», 2006.
- Ray P. Prasad. Surface Mount Technology – Principles and Practice. 2nd ed. – Kluwer Academic Publishers, Boston, USA, 2002. – 772 p.
- Intel Corp. Ball Grid Array (BGA) Packaging/ Packaging Databook – 2000.
http://www.intel.com/design/packtech/ch_14.pdf
- Texas Instruments Inc. MicroStar BGA™ Packaging Reference Guide. – Sept. 2000.
http://focus.ti.com/lit/wp/ssyz015b/ssyz015b.pdf
- Micron Technology, Inc. SMT RECOMMENDATIONS FOR BGA ASSEMBLY/TN-00-11 – 2001.
http://www.solder.net/PDFs/BGAAssembly_Issues_Micron.pdf
- Ray Cirimele, BEST, Inc. BGA REWORK. A COMPARITIVE STUDY OF SELECTIVE SOLDER PASTE DEPOSITION FOR AREA ARRAY PACKAGES
http://www.smtnet.com/adsystem/redir.cfm?adid=770
- Motorola, Inc. Plastic Ball Grid Array (PBGA)/AN1231. – 1996.
http://www.analysistech.com/downloads/PBGAExample.pdf
- Motorola, Inc. Customer Applications Support and Reliability Test Center/PBGA Presentation.
http://www.freescale.com/files/32bit/doc/package_info/PBGAPRES.pdf?fpsp=1&WT_TYPE=Packaging%20Information&WT_VENDOR=FREESCALE&WT_FILE_FORMAT=pdf&WT_ASSET=Documentation
- Cooper Industries, Inc. BGA/QFP Repair and Rework.
http://www.yeinternational.fi/files/products/BGA_QFP_Broch_GB.pdf
- Cooper Industries, Inc. The Weller MSP 2000 Micro Stencil Printer makes SMD repairs easier.
http://www.ronenright.co.nz/press/MSP2000.pdf
- PACE Inc. AREA ARRAY REWORK TF 1700 & TF 2700.
http://www.paceworldwide.com/uploads/TF%201700-TF2700%20Manual_EN.pdf
- PACE Inc. SMT & Area array rework.
http://www.paceworldwide.com/uploads/Pace%20SMT%20Area%20Brochure%20final%20lo%20res.pdf
- Advanced Techniques US, Inc. BGA Rework. – 2009
http://www.atco-us.com/data/applications/4301919874a1c3d6d90468.pdf
- MARTIN GmbH. Rework – ABC – 2005.
http://www.martin-smt.de/pdfs/abc/rework-abc-2005.pdf
- MARTIN GmbH. Dispense – ABC – 2002.
http://www.martin-smt.de/pdfs/abc/dispense-abc-cd.pdf
- Flextac BGA Rework Stencils.
http://www.circuitmedic.com/products/201-3120.shtml
- Best, Inc. StencilQuik™.
http://solder.net/stencilquik/default.asp
- Best, Inc. StencilQuik™. User Instructions.
http://solder.net/stencilquik/User_Instructions.pdf
- «Лазер-Трафарет». Трафареты для поверхностного монтажа печатных плат.
http://laser-trafaret.ru/lazer.php
- Вейн Паллием. Проектируем платы с BGA/EDA Expert, №5(68), май 2002, с. 48 – 51.
http://www.circuitry.ru/pdf/2_2008/1786.pdf
- Материалы компаний-производителей оборудования и оснастки для установки, пайки BGA-компонентов, ремонта/восстановления сборок, реболлинга:
ERSA GmbH
http://www.ersa.de/en/index.html
MARTIN GMBH
http://www.martin-smt.de/index.php
PACE INC.
http://www.paceworldwide.com/
Weller (торговая марка компании Cooper Industries, LLC.)
http://www.cooperhandtools.com/europe/electronics_products/weller/index.htm
|
 |
|