12 декабря 2011
Установка компонентов на устройства 3D-MID: концепции современного сборочного оборудования
Разработка современного изделия электроники практически всегда подразумевает рост функциональности и надежности при одновременном уменьшении массы и габаритов, удешевлении проектирования и производства по сравнению с изделием-предшественником. При этом конструктор часто оказывается перед необходимостью сочетания в рамках одного устройства электрических и механических элементов и узлов. Перспективным и активно развивающимся в настоящее время направлением, решающим такие задачи, является внедрение устройств 3D-MID – монтажных оснований, изготавливаемых из термопластиков методами литья с металлизацией проводящего рисунка тем или иным способом на активированных участках трехмерной поверхности устройства. Наибольшее распространение на данный момент получили методы двухкомпонентного литья под давлением, а также однокомпонентного литья с последующим аддитивным или субтрактивным лазерным структурированием проводящего рисунка. Для некоторых устройств находит применение формирование рисунка при помощи горячего тиснения металлической фольги [1, 10, 11, 12].
Устройства 3D-MID обладают многочисленными достоинствами, среди которых следует отметить возможность реализации в рамках единого устройства монтажного основания с рисунком электрической схемы, а также таких элементов конструкции, как корпус, экран, теплоотвод, элементы фиксации, излучатели, соединители, переключатели и пр. Внедрение таких устройств означает упрощение и сокращение по времени сборочного процесса при увеличении надежности производства – прежде всего, за счет меньшего числа механических деталей. Материал устройств 3D-MID – различные термопластики – дружественен к окружающей среде и пригоден для вторичной переработки.
Особенности конструкции устройств 3D-MID предопределили области их предпочтительного применения – в настоящее время это автомобильная электроника, промышленная автоматизация, телекоммуникации, медицинские технологии, потребительская электроника. Некоторые примеры устройств 3D-MID представлены ниже на рис. 1.
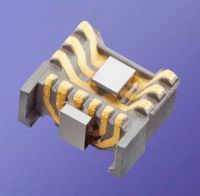
(а)
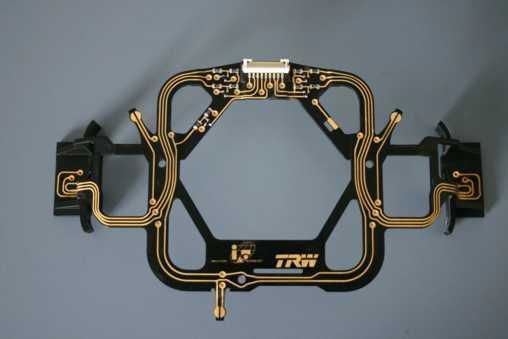
(б)

в)
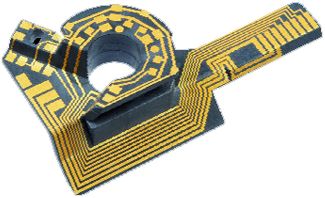
(г)
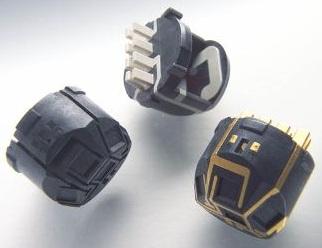
(д)
Рис. 1. Примеры изделий на базе технологии 3D MID: а) датчик магнитного поля на компонентах flip chip, установленных на непроводящий адгезив [Источник: HARTING Mitronics AG, 13]; б) концепт многофункционального автомобильного рулевого колеса [Источник: LPKF Laser & Electronics AG, I & T 3D Produktionsgesellschaft mbH и TRW Automotive Safety Systems, 14]; в) датчик угла поворота [Источник: HSG-IMAT, 15], г) датчик радиолокатора для адаптивного круиз-контроля [Источник: Iskra Automobiltechnik, 16], д) датчик автомобильных систем климат-контроля [Источник: Hella, 17].
Основные сборочные операции для устройств 3D-MID аналогичны применяемым в традиционной технологии поверхностного монтажа – это дозирование паяльной пасты/клея, установка компонентов и пайка оплавлением. Отличие их реализации заключается, в частности, в повышенных требованиях к процессу установки компонентов. При этом основная проблема заключается в необходимости установки компонентов на криволинейные поверхности либо поверхности, располагающиеся под углом, отличным от угла в 90° между осью Z сборочной головки и плоскостью расположения установленного компонента.
Для реализации операции пайки оплавлением имеет существенное значение стойкость термопластиков к воздействиям высоких температур – далеко не все из них в состоянии выдержать температуру пайки оплавлением. В то же время для них характерен более высокий ТКР, чем у традиционных материалов печатных плат на основе эпоксидной смолы. Такие материалы, как полибутилентерефталат/ полиэтилентерефталат (PBT/PET), полиамид (PA6/6T) и жидкокристаллический полимер (LCP), хорошо подходят для бессвинцовой пайки. Если требуется применение других термопластичных материалов или следует минимизировать тепловые напряжения, перспективной альтернативой является технология создания соединений с помощью изотропных проводящих адгезивов. Можно также применять точечную пайку. Монтаж бескорпусных кристаллов на 3D-MID возможно производить при помощи традиционной ультразвуковой/термокомпрессионной сварки, а компонентов flip chip – при помощи изотропных проводящих или непроводящих адгезивов [1, 10, 11].
В данной статье мы ограничимся операцией автоматизированной 3D-установки компонентов поверхностного монтажа и рассмотрим несколько современных подходов к ее реализации с точки зрения конструкции автоматов и их оснащения – как предлагаемых серийно, так и существующих в качестве опытных образцов.
Перед тем, как приступить непосредственно к рассмотрению подходов, приведем классификацию трехмерных монтажных оснований по критерию расположения поверхностей установки компонентов (табл. 1) [2].
Таблица 1. Классификация трехмерных монтажных оснований
Размерность |
Расположение поверхностей установки компонентов |
Схема процесса установки компонентов |
Области применения |
2D |
Плоская поверхность |
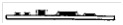 |
Обычные печатные платы |
2½D |
Плоская поверхность, 3D-элементы на обеих сторонах |
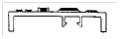 |
Простые корпуса |
2½D |
Плоская поверхность, 3D-элементы на стороне установки |
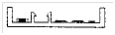 |
Простой монтаж,
Модульная конструкция |
2½D |
Несколько параллельных поверхностей |
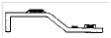 |
Фиксация тяжелых компонентов |
n x 2D |
Несколько параллельных поверхностей;
поверхности, располагающиеся под углом |
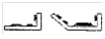 |
Простые корпуса,
Компактные печатные платы |
3D |
Регулярные поверхности, например, цилиндрические |
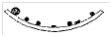 |
Телекоммуникации,
автомобилестроение |
3D |
Поверхности свободной формы |
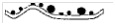 |
Камеры |
В статье мы будем касаться концепций автоматов, способных реализовать размерности установки n x 2D и 3D.
Требования, предъявляемые процессом автоматической сборки
При установке компонентов важнейшим требованием является обеспечение перпендикулярности плоскости установки компонента к оси перемещения сборочной головки. Это же требование справедливо и для операции дозирования, однако здесь оно даже более жесткое: для надежного нанесения пасты допускается меньший угол между иглой дозатора и плоскостью монтажного основания, чем в случае установки компонентов [1].
Необходима механическая фиксация компонентов на наклонных поверхностях, в противном случае весьма вероятно сползание компонентов с посадочных мест под воздействием собственной массы при изменении положения устройства 3D-MID, вибрациях, линейных ускорениях и пр. В особенности это свойственно компонентам с большой массой и малой областью контакта с паяльной пастой. Для осуществления фиксации рекомендуется выполнение механических литых конструкций вокруг таких компонентов – например, бортиков у их нижних краев, или же установка компонента в полость. Другое решение – нанесение адгезива под компонент с отверждением в процессе удержания компонента насадкой, при этом автомат должен обладать возможностью установки головки дозирования адгезива [1]. Рекомендуется применение быстроотверждаемых адгезивов или адгезивов с УФ-отверждением – это также потребует от сборочного автомата соответствующего оснащения.
Так как устройство 3D-MID может иметь совершенно произвольную форму и габариты по трем осям, важно предотвратить возможные взаимные столкновения собираемого устройства 3D-MID и технологического оснащения, служащего для фиксации и манипулирования устройством 3D-MID, со сборочной головкой и другими элементами оборудования. Достигается это расположением всех элементов технологического оснащения вне рабочей области перемещения головки по осям X, Y, т.е в области над монтажным основанием, где перемещение головки осуществляется только по оси Z, а также в области под основанием (под конвейером автомата). Следует отметить, что конструкция рабочей зоны современных автоматов очень компактна, отличается малыми осевыми перемещениями, поэтому место для размещения элементов технологического оснащения сильно ограничено.
При традиционной 2D-установке от сборочного автомата требуется обеспечить 4 распределенных между компонентом и монтажным основанием степени свободы – 3 линейных и одну вращательную, при 3D этих степеней свободы должно быть по крайней мере 6 [3].
Концепции построения сборочных автоматов для 3D-MID
Рассмотрим несколько современных концепций автоматов, применяемых для установки компонентов на устройства 3D-MID. Часть из них существует в виде отлаженных и готовых к производству моделей, часть еще не покинуло стадию опытных образцов и проходит испытания и апробацию. После рассмотрения сравним предложенные концепции, отметив их достоинства и недостатки.
Первым и самым простым решением является использование существующего оборудования для 2D-установки компонентов. Разумеется, такое оборудование позволяет собирать только изделия типа 2,5D (табл. 1), где компоненты располагаются на разных уровнях в плоскостях, перпендикулярных оси вертикального перемещения сборочной головки, поэтому мы оставим его за рамками рассмотрения.
Линия, оснащенная 6-осевыми промышленными роботами
Установка компонентов на устройства 3D-MID имеет много общего с применяемыми в машиностроении традиционными и хорошо отлаженными за многие годы пространственными операциями обработки и сборки, поэтому неудивительно, что ряд компаний пошел по пути использования в качестве сборочной головки гибких, свободно программируемых 6-осевых промышленных роботов в составе производственной линии.
Примером такого подхода может служить гибкая комплексная производственная линия (рис. 2), служащая для выпуска трехмерных мехатронных сборок – переключателей для встраивания в руль мотоцикла (6 типов устройств с 50 различными вариантами установки компонентов, рис. 3 [5, 6]), а также прочих устройств 3D-MID с габаритами вплоть до 100 x100 x100 мм³.
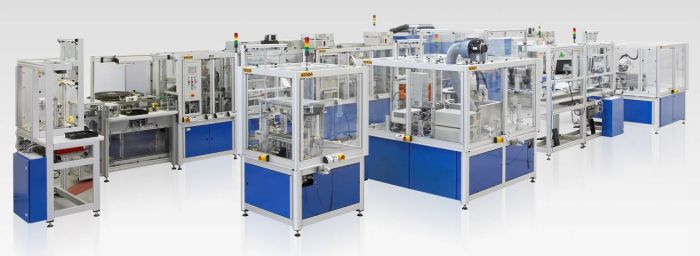
Рис. 2. Комплексная производственная линия сборки переключателей для мотоцикла на основе 3D MID. Источник: [5, 6].
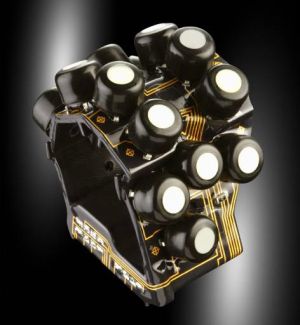
Рис. 3. Собираемое устройство 3D MID – переключатель для мотоциклов. Источник: [6].
Техпроцесс состоит из следующих основных этапов (рис. 4):
- входной контроль деталей 3D-MID;
- 3D-дозирование паяльной пасты с последующей оптической инспекции областей нанесения (рис. 4а);
- 3D-установка компонентов поверхностного монтажа, в том числе светодиодов, а также переключателей (рис. 4б);
- пайка с последующей трехмерной автоматической оптической инспекцией (рис. 4в);
- установка контактных штырьков;
- нанесение защитного покрытия;
- окончательная сборка и монтаж кабелей;
- окончательный функциональный контроль: тактильный, оптический и электрический;
- упаковка готовых изделий.
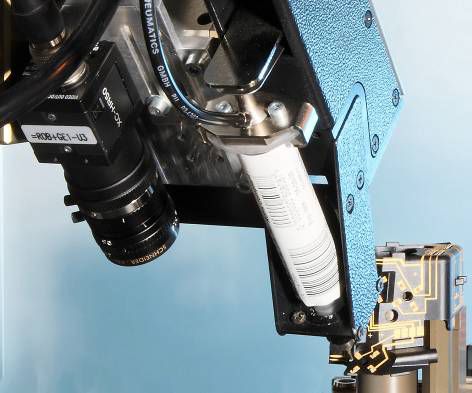
(а)
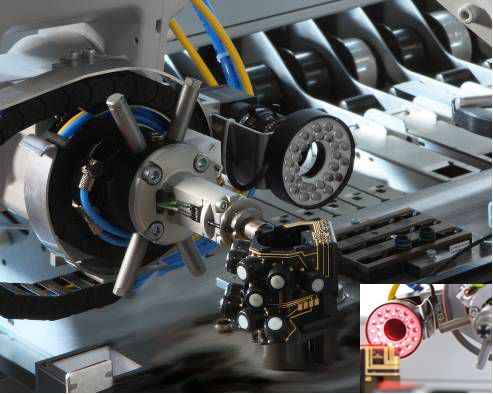
(б)
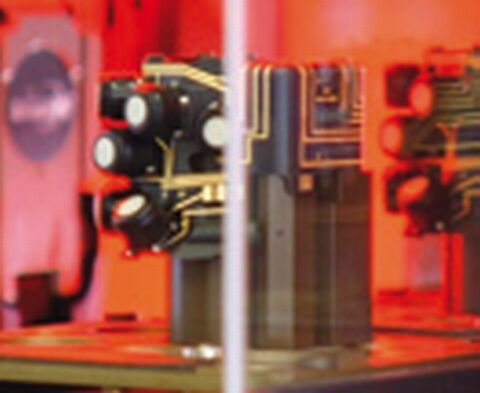
(в)
Рис. 4. Операции 3D-дозирования паяльной пасты (а), установки компонентов (б) и АОИ паяных сборок (в) на роботизированной линии.
Данные по точности линии не приводятся, заявленное время цикла составляет 2-3 с на компонент.
|